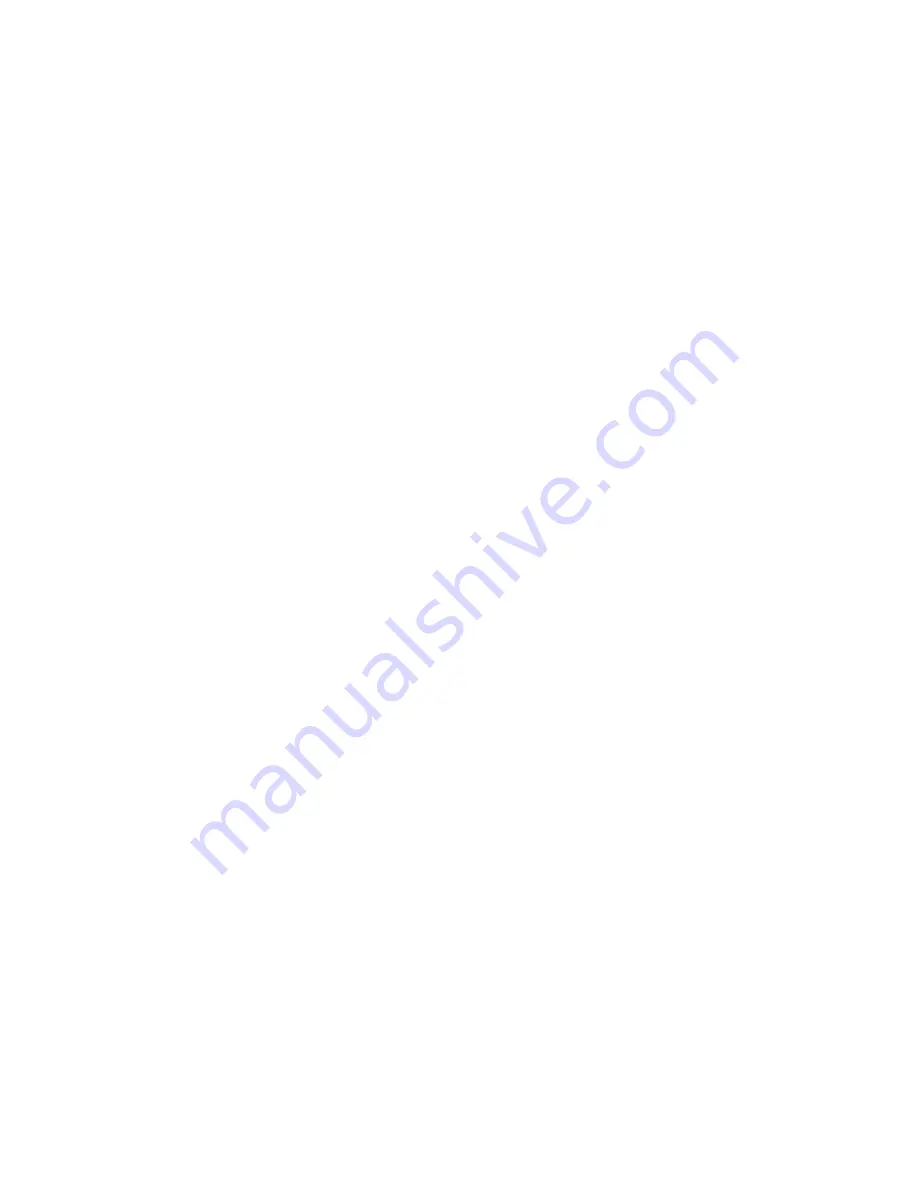
6
6.1.2. Adjusting the Set Point
It is not recommended (or necessary) to remove the Hand Wheel during service as this will
affect the set point of the regulator. Should it be required to adjust the set point please
follow the instructions below:
i.
Remove the Nameplate (22) and Cap from the Hand Wheel (23) and loosen the
Lock Nut (12) such that the Hand Wheel is able to spin freely on the Adjusting
Screw (11)
ii.
Connect the correct fittings to the Inlet and Outlet ports of the regulator. Ensure
that any gauge ports are plugged or that the correct gauge is fitted
iii.
With the Regulator Body (1) secured in a vice apply the Maximum Working
Pressure (MWP) to the Inlet of the regulator
iv.
Connect the Outlet port to a calibrated pressure test gauge appropriate to the
required set pressure. As the regulator is non-venting, ensure that a ball/needle
valve is fitted to allow pressure to be relieved downstream of the regulator
v.
Using a slotted screwdriver, turn the Adjusting Screw (11) clockwise until the
desired set point has been reached
vi.
Ensure repeatability by allowing flow through the regulator using the ball/needle
valve
vii.
With the outlet pressure set, screw the first Lock Nut (12) to the base of the
Adjusting Screw (11) against the Bonnet (10)
viii.
Position the Hand Wheel (23) onto the Lock Nut (12). Ensure that the Lock Nut
and Hand Wheel become engaged
ix.
Fasten the second Lock Nut (12) against the Hand Wheel (23) and gently begin to
tighten using a 13mm socket until it begins to secure itself
x.
At this point, whilst holding the Hand Wheel (23) continue to tighten whilst
simultaneously turning slightly anti-clockwise to prevent it from locking against
the Bonnet (10)
xi.
Ensure that the Lock Nut (12) is sufficiently tightened, taking care not to adjust
the set point
xii.
Turning of the Hand Wheel (23) should now also turn the Adjusting Screw (11)
which will control the pressure
xiii.
Turn the Hand Wheel clockwise until it reaches its set point and check to make
sure that the desired outlet pressure is correct.
xiv.
If the set point is not correct, repeat steps v. to xiii.
xv.
Reduce the pressure downstream by venting the pressure through ball/needle
valve and then turning the Hand Wheel anti-clockwise until the regulator closes
xvi.
The Cap and Nameplate (22) can now be placed into the Hand Wheel (23).
Ensure that the information stated on the Nameplate is in accordance with the
set pressure of the regulator