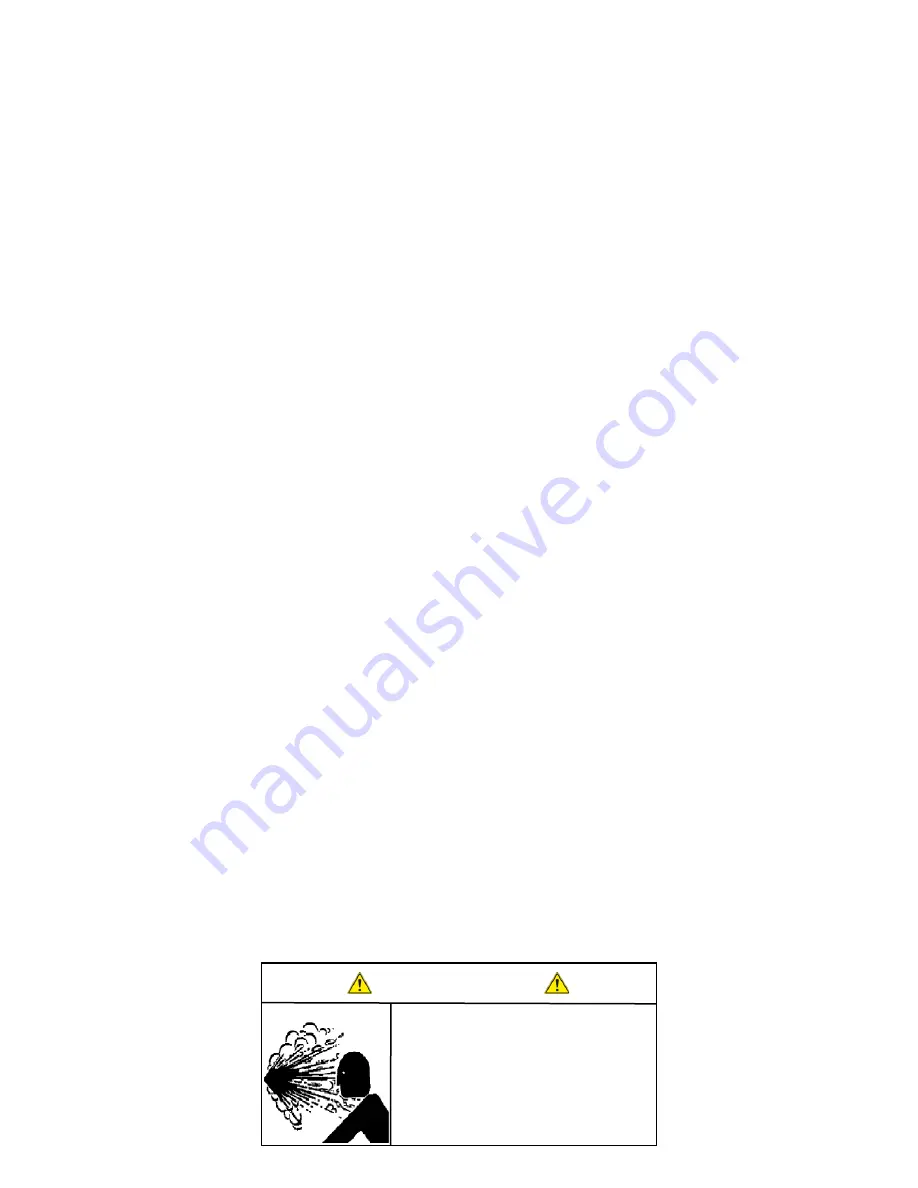
FILTER SYSTEM START-UP PROCEDURE
Prior to turning on the flow to the inlet service, please make the following checks:
1. Check inside filter unit to be sure basket and filter bag (if applicable) are in housing and do not require
cleaning or replacement. If necessary install a clean filter basket and bag (if applicable).
2. Check that filter unit cover is securely fastened to housing. You are now ready to open the flow to the inlet
service line. Slowly open the inlet service line approximately 25% of normal operational flow (open slowly
so as not to displace filter bag inside the housing). After filter unit is pressurized and vented, slowly open
outlet service line unit valve until completely open. Complete opening of inlet service line until desired flow
rate is reached.
Once the desired service flow has been established, the filter will operate efficiently until dirty. However,
under no circumstances should more than 5 PSI differential pressure through the filter be obtained.
Operating the filter unit with a high differential may cause filter bags to rupture and/or cause damage to filter
system and downstream equipment.
To prevent excessive drop through the filter unit, regular inspection of the filter media is required. Monitoring
of differential pressure through the housing can be utilized as a means of determining whether or not the
filter media needs cleaning or replacement.
MAINTENANCE
When it becomes necessary to clean or replace filter media, follow the procedure outlined below:
1. First close the flow from the inlet service line.
2. Close the flow to the outlet service line. (In some applications closing flow to outlet is not required.)
3. Relieve the pressure from the filter unit.
OPERATION
WARNING
CONTENTS UNDER PRESSURE
Relieve Pressure in accordance
with Manufacturer’s instructions
before opening the Filter Vessel.
FAILURE TO DO SO MAY RESULT
IN SERIOUS BODILY INJURY.
Page 4
Maintenance Manual for EU-1000 & EU-1000-2