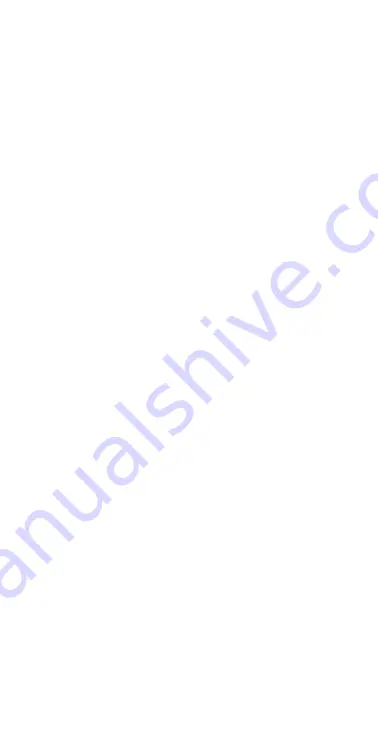
21
steP 2. laYout tRansFeR
Using a black marker, transfer the panel layouts
to the bottom plate. Include all window and
door openings as well as the vertical electrical
chases in each wall panel. If electrical chases
are being utilized, drill the chase holes as you
set each panel using a minimum 1 1/2” bit.
(Do not drill all the chase holes down the entire
wall, because as panel joints grow you will be
off center as you get to the end of the wall.)
steP 3. Panel tilt
Determine the best place to start the
installation and get your panels to that area.
Most of the time it is best to start in a building
corner. The corners are locked together using
Premier Panel Screws secured through the
panel spaced 2’ o.c. maximum. (Normally you
will use a screw two inches longer than the wall
thickness.) Install the screws into the panel
close to the lumber plate. Use a drill to finish
tightening and the panels will cinch together.
Set the underside of the screw heads flush with
the OSB, do not break the skin of the panel.
Always check the fastening or engineering
schedule on your shop drawings.
Summary of Contents for Floors
Page 55: ...55...