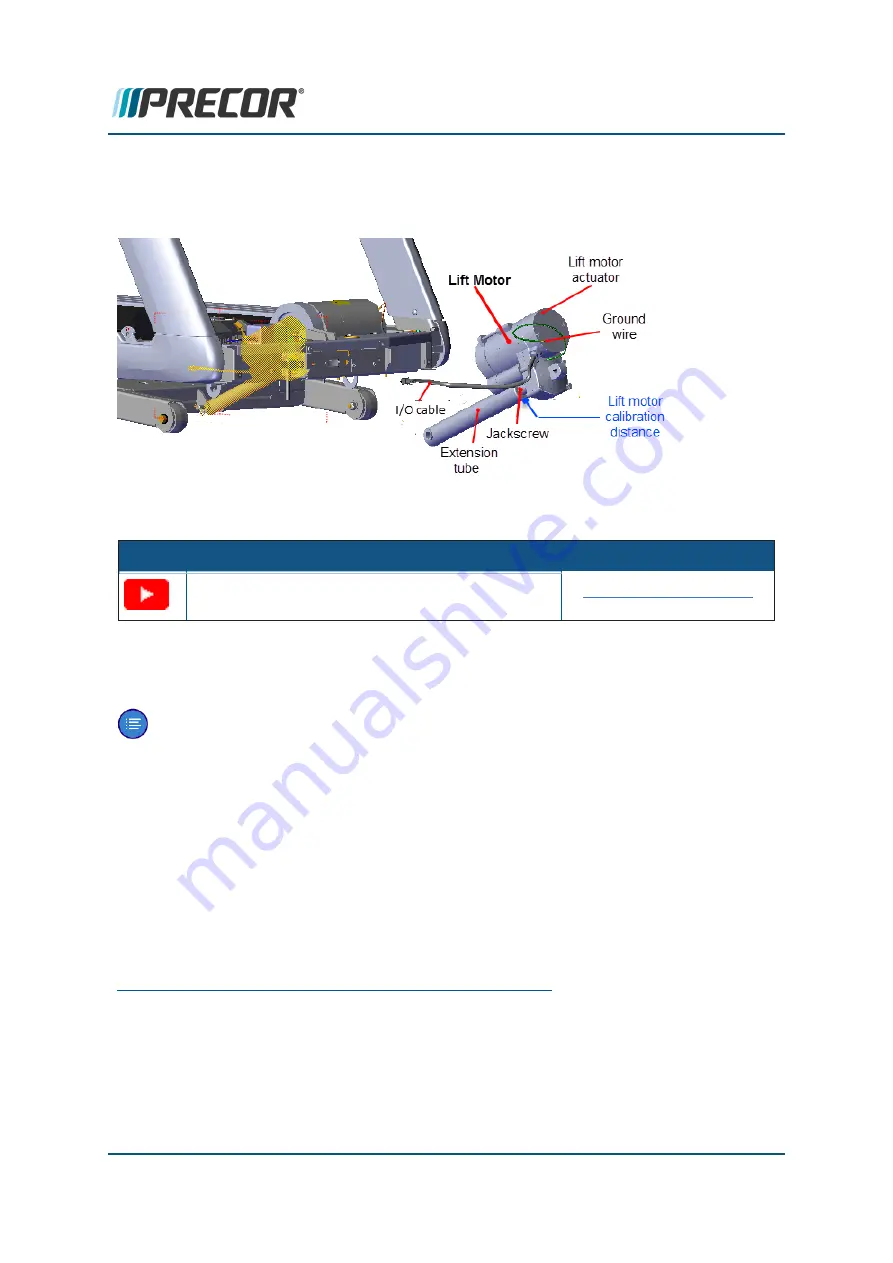
Lift Motor Replacement
This procedure provides instruction to remove and replace the Lift Motor.
Videos
Service Video
Link
TRM400 Lift Motor Replacement
Procedure
Review entire procedure before starting.
Note
: The replacement lift motor must be calibrated prior to installation.
1. If not already set to 0% incline, set the incline to 0%.
2. Switch the treadmill power “OFF” and
unplug
1
the power cord.
3. Disconnect the lift motor cable connectors from
LPCA
2
J1 and J7 connectors.
4. Remove the lift motor’s green frame ground wire from the frame.
1
Disconnect a device power cord plug or cable connector from the power receptacle or out-
let.
2
Lower Printed Circuit Assembly board; also refered to as the Lower PCA or simply as the
lower board. On treadmills, it is the console to base function interface and the motor con-
troller unit (MCU). On self-powered units, it is the lower PCA console to base function inter-
face.
Contact Precor Customer Support at [email protected] or 800.786.8404 with
any questions.
Page 80
6 Replacement Procedures
Lift Motor Replacement