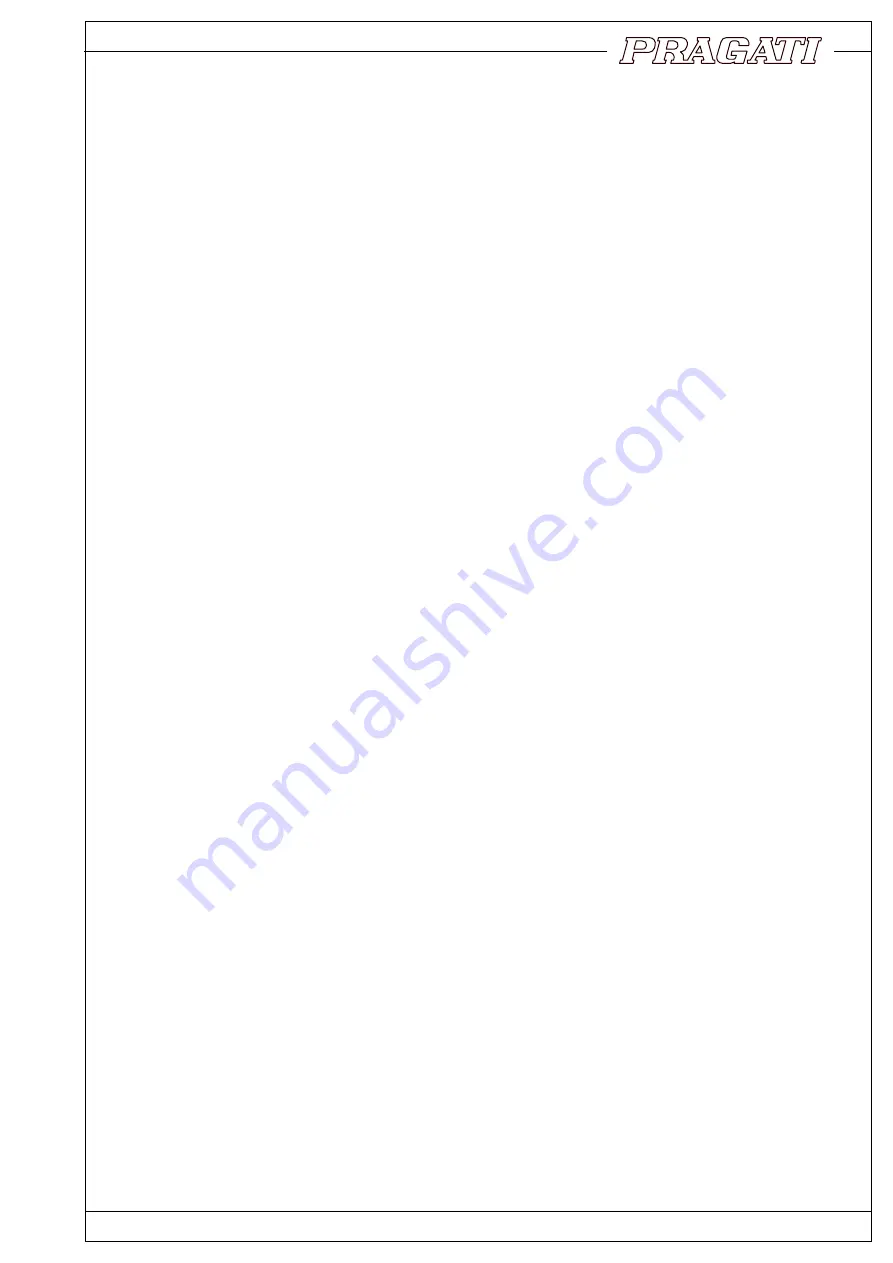
BI-DIRECTIONAL TOOL TURRETS 13
11. Requirements of turret control :
11.1 Sequence of operation :
Suggested flow chart is given in the diagram on page 12. It might be necessary to modify the program
depending on individual applications. However, following general points should be noted while selecting
the control system and its program :
* Indexing times of these turrets are short. It is therefore necessary to select a particularly fast PLC
(programmable logic controller) for the control of turret operation.
* Referring to the electrical signal diagram on page 10 ; time ‘T3’ is particularly critical. Motor must come
to a physical halt within this time. Otherwise, the turret will get declamped, and the turret clamp switch signal
will be lost.
For stopping the motor in minimum possible time, following measures are required :
* Control should be capable of detecting the turret clamp switch signal within a period 5 ms.
* Motor should be switched off by solid state relays, which give fastest possible operation.Contactors take
much longer time (30 to 40 ms). Suggested electrical circuit is on page 9.
* In case of doubt ,time delay between 'turret clamp signal' and 'motor switch off signal' should be monitored
on a dual beam oscilloscope, with memory.
11.2 Safety interlocks :
11.21. 'MOTOR OVERHEAT' SIGNAL
Thermal relay has been provided in the motor winding to give indication of motor overheating. In the event
of overheating relay should trip the motor contactor, and also give ‘Motor overheating’ signal to the control
circuit. Motor contactor should be tripped without depending on PLC software. Typical circuit diagram is
given in page 9.
11.22. 'TIME FAULT'’ SIGNAL
Time required for indexing through 180° is between 1.3 seconds to 3.1 seconds depending on the model.
This is the maximum time required for completing the indexing operation. If the ‘cycle complete’ signal is
not received even after this time, this will be an indication of some fault in the indexing cycle. Control circuit
should be programmed to give a ‘Time Fault’ signal, if the ‘Cycle complete’ signal is not received within
a specified time (say 1 second more than the maximum expected time) after the ‘Cycle Start’ signal.
11.23.'TURRET NOT LOCKED' SIGNAL.
Turret clamp switch should be continuously monitored. If the clamp signal is missing, a Feed Hold signal
should be generated to stop the machine movements. Simultaneously, ‘Turret not locked’ alarm signal
should also be generated.
11.24. 'POSITION FAULT' SIGNAL
At the end of indexing cycle, a check should be made to ensure that the turret has indexed to the demanded
position. If the actual position and demanded position do not match, then ‘Position fault’ alarm signal should
be generated.
11.25. 'INVALID DEMAND' SIGNAL
An eight position turret cannot react to a tool demand other than 1 to 8. If any other tool position
(say 12) is demanded, the control should give out 'INVALID DEMAND' signal.
All these signals should stop the operation of the machine, and an indication should be available on the
control panel regarding the nature of the fault.