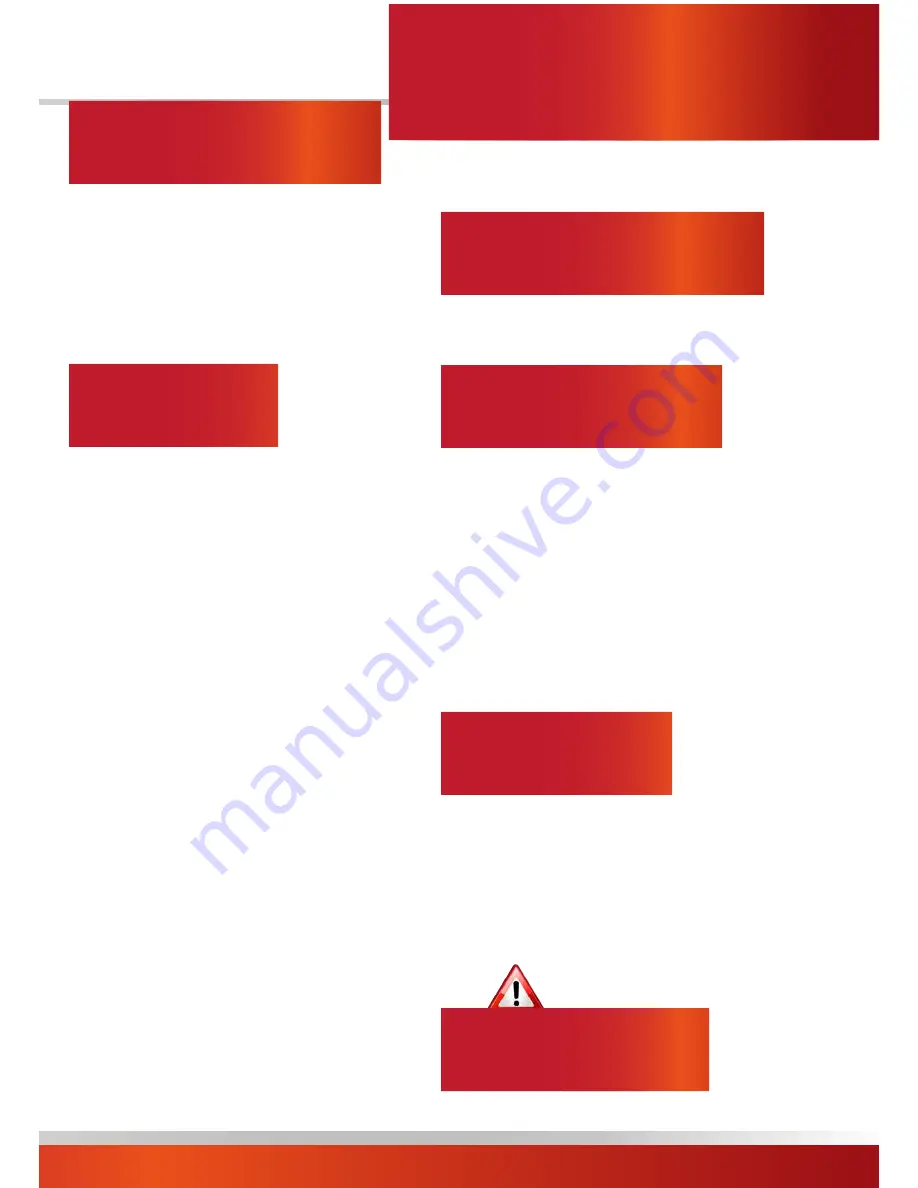
page no. 15 of 48
LNVx Range Users, Installation & Servicing Instructions Doc Ref M104 issue 1.0 Sep 2018.
All LNVx heaters comply with the following European
Directives:
Energy Related Product Directive:
2009/125/EC*
Gas Appliance Directive:
2009/142/EC
Electromagnetic Compatibility Directive: 2004/108/EC
Low Voltage Directive:
2006/95/EC
Machinery
Directive:
2006/42/EC
Air heater(s) must be installed in accordance with
BS6230
and
BS5440
plus any relevant requirements of local and
national building codes.
* where appropriate.
Powrmatic LNVx units are designed to operate within an
ambient temperature range of -10 to 25°C.
LNVx heaters can be installed in several ways: i)
suspended from ‘drop rods’ via purpose designed M10
suspension fixing points on the heater, ii) attached to our
optional wall support brackets or iii) positioned on a level,
non-combustible base. In all cases, it is important that all
supporting structures have been assessed with regard to
the relevant weight loadings.
Consideration should be given to flue routes and points of
exit, gas, electrical and control connections. Consideration
should also be given to the throw characteristics of the
heater, issues of public access and siting of environmental
control stations and/or remote temperature sensors
where the position needs to be representative of the zone
temperature to which they refer.
Where the location of the air heater is such that it might
suffer external mechanical damage e.g. from overhead
cranes, fork lift trucks, it must be suitably protected.
Heaters should not be installed in hazardous areas or
areas where there is a foreseeable risk of flammable
or corrosion inducing particles, gases or vapours being
drawn into the combustion air or main fan circuits.
Areas where special consideration or advice may be
required could include but is not limited to –
•
Where de-greasing solvents are present, even in
minute concentrations
•
Where paint spraying is carried out
•
Where styrenes or other laminating products are
used
•
Where airborne silicone is present
•
Where petrol engine vehicles are stored or
maintained
•
Where dust is present (i.e. wood working or
joinery shops)
•
Where high levels of extract persist.
Installation in such areas may be possible under specific
conditions. Please consult our Technical Department for
further information.
The heater should be correctly sized for the area that it is
heating, Full calculations need to be preformed to ensure
the correct KW output heater is fitted (CIBSE elemental
methodology can be used, or the Powrmatic Technical
Department can provide guidelines).
Wiring external to the air heater must be installed in
accordance with the I.E.E. Regulations for Electrical
Installations and any local regulations which apply.
All standard heaters are supplied by 230V - 1ph, 50Hz.
The method of connection to the main electricity supply
must:-
- facilitate the complete electrical isolation of the unit(s)
via a suitable fused isolator (see section 2.4.5 for ratings)
- be in a readily accessible position adjacent to the unit(s)
- serve only the unit(s)
- have a contact separation of at least 3mm in all poles.
See the accompanying wiring diagram for the heater
electrical connections
LNVx CCF and fan/silencer units can also be supplied for
400V 3N, 50Hz.
A servicing valve and union to facilitate servicing must
be fitted to the gas inlet pipe work of the heater. The
gas supply must be completed in solid pipe work and be
adequately supported.
Heaters suspended by drop rods, straps or chains must
have a flexible connection as the final link between the
gas supply pipe work and the heater. Sufficient slack
must be left in the connection to take account of normal
movement of the heater.
WARNING: When completing the final gas
connection to the heater do not place undue
strain on the gas pipe work of the heater
.
The local gas undertaking should be consulted at the
installation planning stage in order to establish the
availability of an adequate supply of gas to suit the