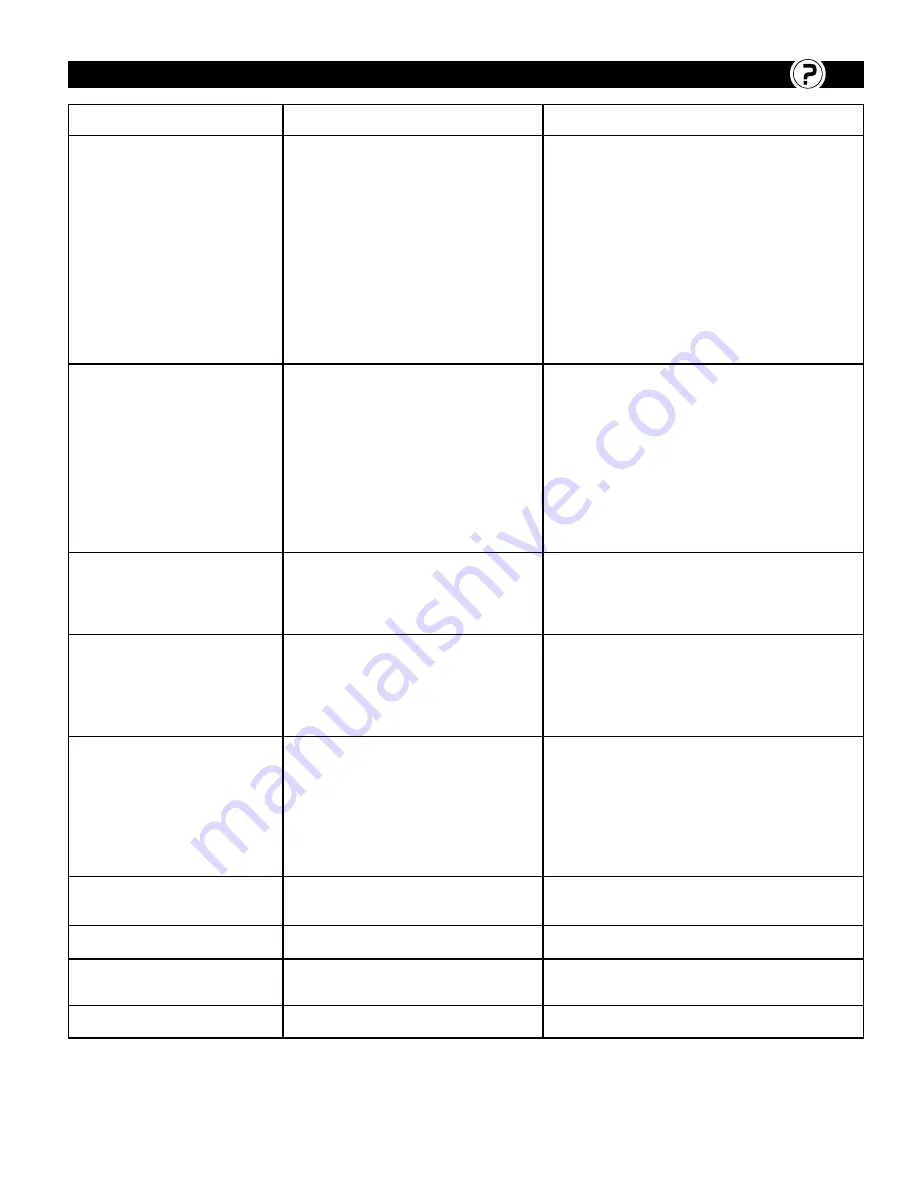
TROUBLESHOOTING
SYMPTON
POSSIBLE CAUSE(S)
1. Low voltage
2. Short circuit in line cord or plug
3. Short circuit in motor
4. Open circuit or loose connection in
motor
5. Incorrect fuses or circuit breakers
6. Defective switch
7. Defective capacitor
8. Motor overload results in circuit
breaker tripped
SOLUTIONS
1. Check power supply for proper voltage
2. Inspect line cord and plug for faulty
insulation or shorted connection
3. Inspect connection on motor.
4. Inspect connection on motor
5. Replace with correct fuses or circuit
breakers
6. Replace switch
7. Replace capacitor
8. Turn the machine off and reset overload
protection.
Frequent tripping of circuit
breaker
Motor stalls or fails to reach
full speed
1. Power overload
2. Low voltage from power supply
3. Undersized line cord
4. Motor overload
5. Short circuit or loose connection in
motor
6. Incorrect fuses or circuit breakers
7. Wood chips clogged
1. Reduce workload on the power supply
2. Check power supply for proper voltage
3. Use line cord of adequate size or reduce
length of wiring
4. Reduce load on motor
5. Inspect the connection in motor for loose or
shorted connection
6. Replace with correct fuses or circuit breakers
7. Inspect chip blower assembly and fan belt.
Remove excessive wood chips
Motor overheats
1. Motor overloaded
2. Excessive dust build-up results in
decreased air circulation
1. Reduce load on motor. Turn off the machine
until motor cools down
2. Remove dust build-up
1. Motor overload
2. Inadequate capacity of circuit
breaker
3. Circuit overload
4. Blades are dull
1. Reduce load on motor
2. Replace with correct circuit breaker
3. Reduce circuit load
4. Sharpen or replace blades
Brake does not Stop the blade
Within 6 seconds
1. Motor brushes not sealed or lightly
sticking
2. Motor brake overheated from use
of defective or wrong size blade
3. Arbor bolt loose
4. Cracked or damaged brushes
5. Other
1. Replace brushes
2. Use a recommended blade. Let cool Down
3. Retighten the arbor bolt
4. Replace brushes
5. Contact Service Center
Brush spark When switch
released
1. Brush worn
2. Other
1. Replace brushes
2. Contact Service Center
Blade hits table
1. Misalignment
1. Adjust cutting head
11
Motor will not start
Angle of cut not accurate
1. Miter table unlocked
2. Sawdust under table
1. Lock miter table
2. Vacuum or blow out dust
Cutting arm wobbles
1. Loose pivot points
1. Contact service center