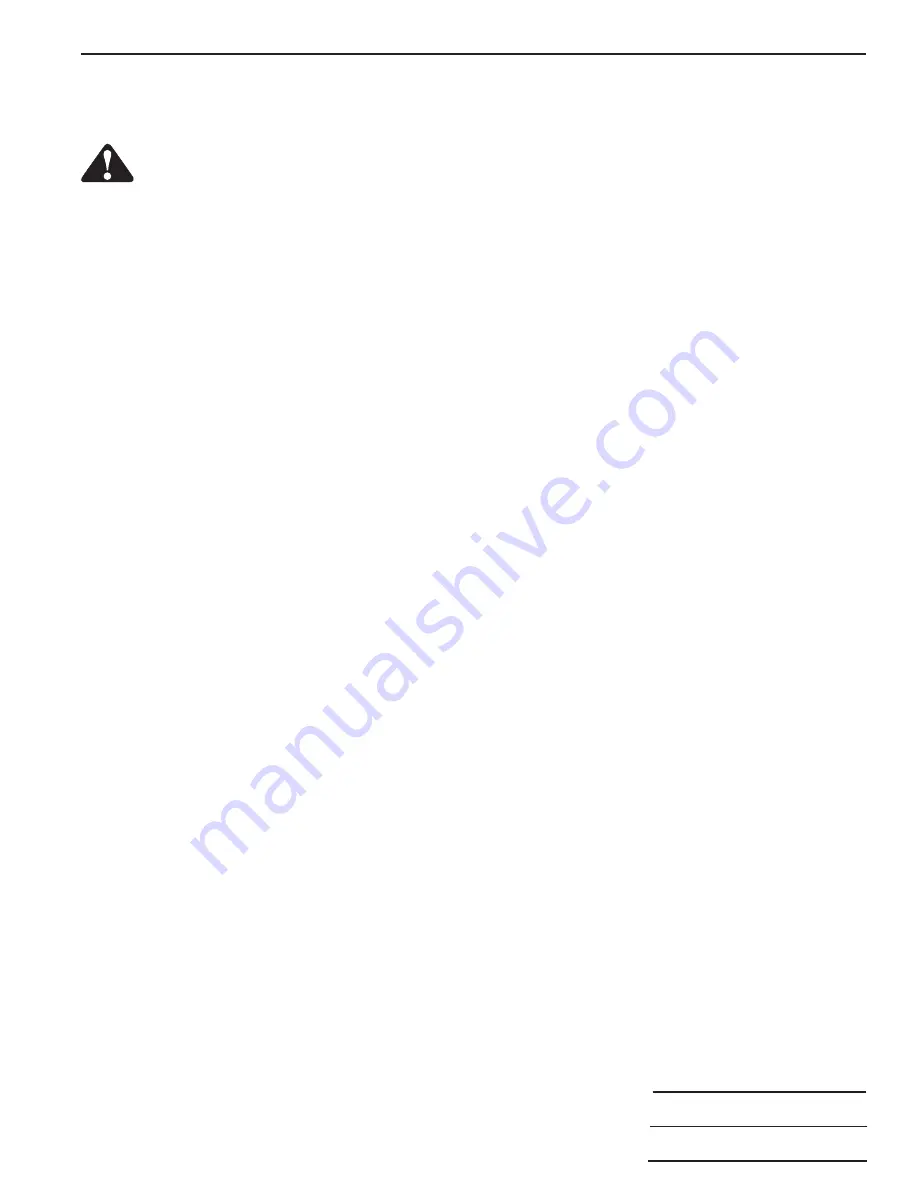
Parts List and Operating Instructions Form No. 102646
PREVENTIVE MAINTENANCE
WARNING:
To help avoid personal injury,
●
Repairs and maintenance are to be performed in a dust-free area by a qualified technician.
Bleeding Air from the System
Upon initial start up or after prolonged use, air can accumulate within the hydraulic system. This entrapped air can
cause the system to respond slowly or behave in an unstable manner. To remove the air, loosen a fitting that is
situated higher than the rest of the fittings in the system. Run the pump until a steady flow of oil free of suspended air
bubbles is observed. Tighten the fitting.
Inspecting the Hydraulic Fluid Level
Check the oil level in the reservoir periodically. The oil level should be 1/2" from the top of the filler hole with all
cylinders retracted. Drain, clean and replenish the reservoir with Power Team hydraulic fluid yearly or more often if
necessary. The frequency of oil change will depend upon the general working conditions, severity of use and overall
cleanliness and care given the pump.
Maintenance Cleaning
1. Keep the outer surface of the pump as free from dirt as possible.
2. Protect all unused couplers.
3. Keep all hose connections free of dirt and grime.
4. Keep the filler/vent cap clean and unobstructed at all times.
5. Equipment connected to the pump must be kept clean.
6. Use only Power Team hydraulic fluids in this pump. Change as recommended.
Draining and Cleaning the Reservoir
IMPORTANT: Clean the pump exterior before the pump interior is removed from the reservoir.
1. Remove the ten screws that fasten the motor and pump assembly to the reservoir. IMPORTANT: Lift the pump
and motor off the reservoir carefully to avoid damaging the gasket or any internal components.
2. Clean the inside of the reservoir and fill half full with clean Power Team hydraulic fluid.
3. Place the pump and motor assembly back onto the reservoir and secure with two machine screws assembled on
opposite corners of the housing. IMPORTANT: Connect a hose to the pressure port on the valve. Place the
other end of the hose into the oil filler plug hole.
4. Run the pump for several minutes. Then disconnect the motor and pump assembly, and drain and clean the
inside of the reservoir.
5. Fill the reservoir with Power Team hydraulic fluid. Place the pump and motor assembly (with gasket) on the
reservoir and install all the screws. Tighten securely and evenly.
Adding Oil to the Reservoir
1. Cylinder(s) must be fully retracted and the gas engine off when adding oil to the reservoir.
2. Clean the entire area around the filler/vent cap before removing the filler/vent cap.
3. Use a clean funnel with filter when adding oil.
4. Use only Power Team hydraulic fluids.
Sheet No.
2 of 7
Issue Date:
Rev. 7-20-94