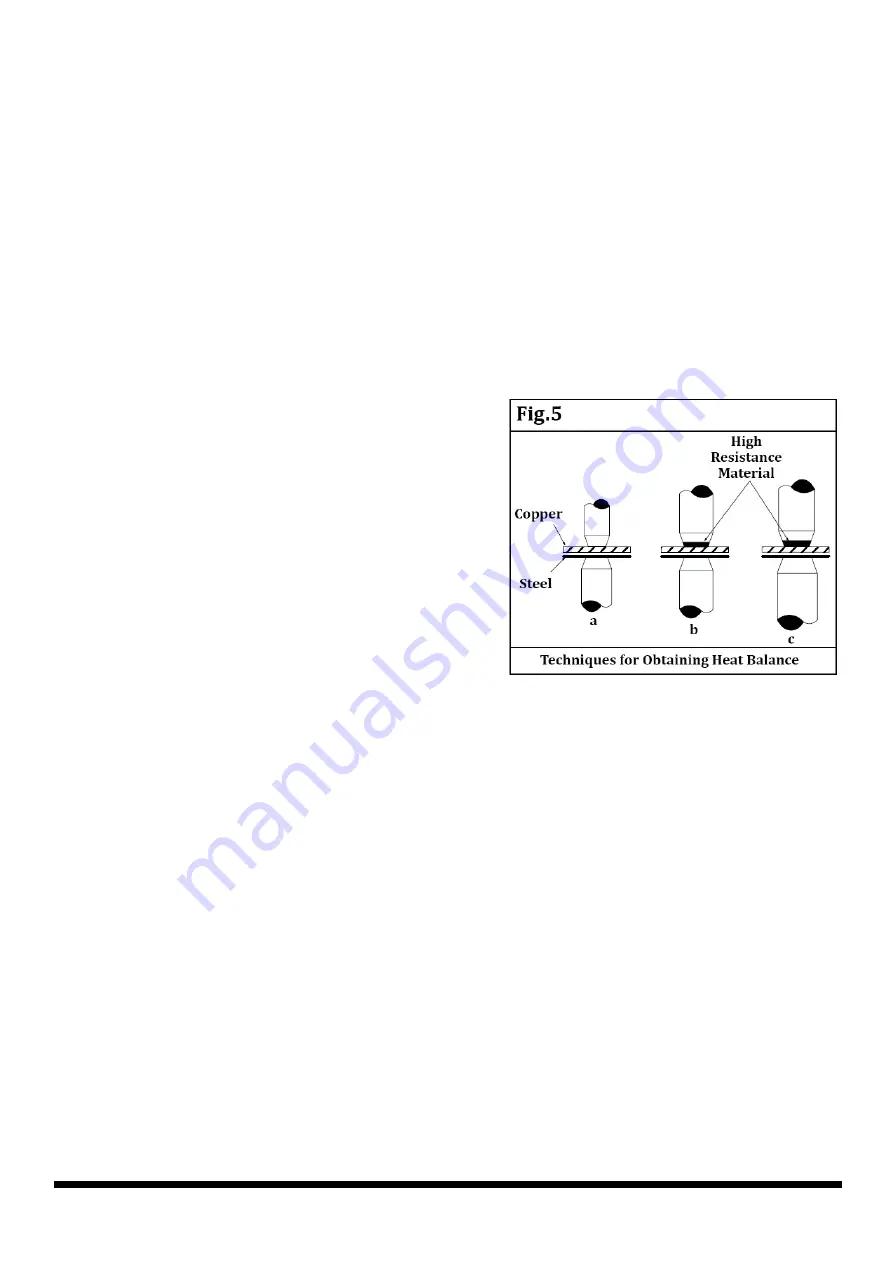
V 4.2
120 Volt Spot Welder
8630196
Visit www.princessauto.com for more information
17
ADDITIONAL DATA
This section of the manual is designed to provide information regarding several of the variables that occur in
some resistance spot welding applications.
HEAT BALANCE
There is no particular problem of heat balance when the materials to be welded are of equal type and
thickness. The heat balance, in such cases, is automatically correct if the electrode tips are of equal diameter,
type, etc. Heat balance may be defined as the conditions of welding in which the fusion zone of the pieces to
be joined are subjected to equal heat and pressure.
When the weldment has parts of unequal thermal characteristics, such as copper and steel, a poor weld may
result for several reasons. The metals may not alloy properly at the interface of the joint. There may be a
greater amount of localized heating in the steel than in the copper. The reason would be because copper has
low electrical resistance and high thermal transfer characteristics, while steel has high electrical resistance and
low thermal transfer characteristics.
Correct heat balance may be obtained in a weldment of this
type by one of several methods. Figure 5 illustrates three
possible solutions to the problem. Figure 5 (a) shows the use
of a smaller electrode tip area for the copper side of the joint
to equalize the fusion characteristics by varying the current
density in different materials. Figure 5 (b) shows the use of
an electrode tip with high electrical resistance material, such
as tungsten or molybdenum, at the contact point. The result
is to create approximately the same fusion zone in the copper
as in the steel. A combination of the two methods is shown
in Figure 5 (c).
SURFACE CONDITIONS
All metals develop oxides which can be detrimental to resistance spot welding. Some oxides, particularly those
of a refractory nature, are more troublesome than others. In addition, mill scale found on hot-rolled steels will
act as an insulator and prevent good quality resistance spot welding. Surfaces to be joined by this process
should be clean, free of oxides, chemical compounds, and have a smooth surface.
MATERIALS DATA FOR RESISTANCE SPOT WELDING
This section of the manual will consider methods used for resistance spot welding some of the common
metals that are used in fabrication work. It is not intended that all the possible problems that could arise will
be answered. The purpose of this section of the manual is to provide general operational data for use with
resistance spot welding machines. Where applicable, the data provided will be related to specific models and
size (kVA) of units.
CAUTION! The units listed in this section are not recommended for aluminum or copper alloys.
MILD STEEL
Mild or low-carbon steel comprises the largest percentage of material welded with the resistance spot
welding process. All low-carbon steels are readily weldable with the process if proper equipment and
procedures are used.
The carbon steels have a tendency to develop hard, brittle welds as the carbon content increases if proper
post-heating procedures are not used. Quick quenching of the weld, where the nuggets cools rapidly,
increases the probability of hard, brittle micro-structure in the weld.