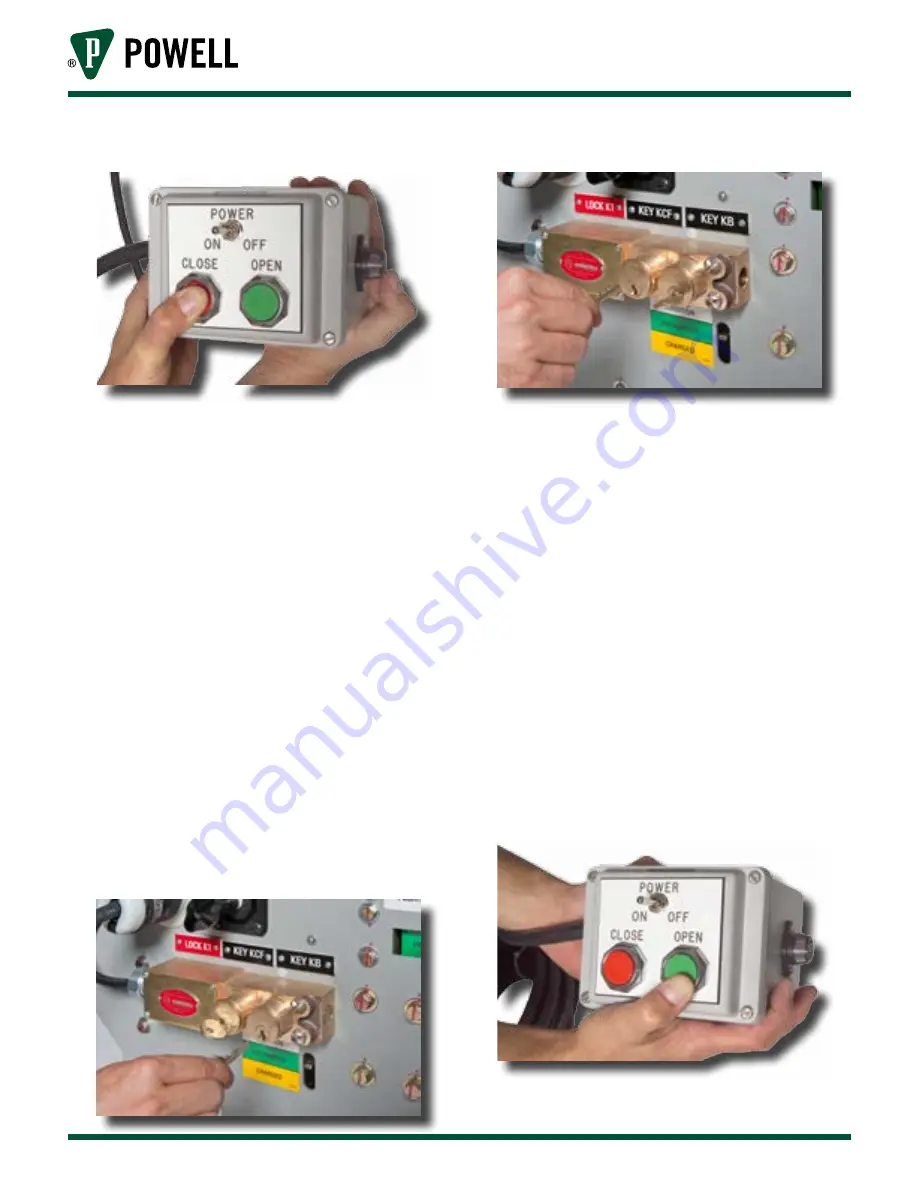
Powered by Safety
®
28
Operating Procedures
PowlVac® Electrically Operated 5kV & 15kV G&T Device
per ConEd Specification EO-2022-15 for ConEd CUSTOMER
01.4IB.50026A
Figure 19 Press Close on Control Box
16. Unplug the remote control box from the
120V power supply.
17. Move the control selector switch from the
“Close” position to the “Off” position.
18. Disconnect the control box umbilical cord
from the ground and test device.
19. Rotate key KCF in key lock K1. Remove key
KB from key lock K1.
20. Ground and test device can no longer be
operated.
21. Secure key KB in lock box on premises.
B. r
emovInG
G
round
1. Obtain key KB from lock box on premises.
2. Transfer key KB to key lock K1 (Figure 20)
and rotate key. Key KB is now captive and
key KCF is released (Figure 21). The control
circuit for the ground and test device is now
enabled.
Figure 20 Inserting Key KB into Key Lock K1
Figure 21 Key KCF is Released from Key Lock K1
3. Verify that the control selector switch on
the front of the ground and test device is in
the “Off” (center) position (Figure 16).
4. Connect the umbilical cord of the remote
control box to the ground and test device
(Figure 17). Ensure the cord is locked into
the connected position by turning the plug
clockwise.
5. Move the selector switch from the “Off”
position to the “Open” position.
6. From a safe distance, connect the ground
and test device remote control box to a
120VAC, 15 ampere power supply.
7. Depress the “Open” push button switch
on the control box (Figure 22) to open the
ground and test device ground making
switch.
Figure 22 Press Open on Control Box