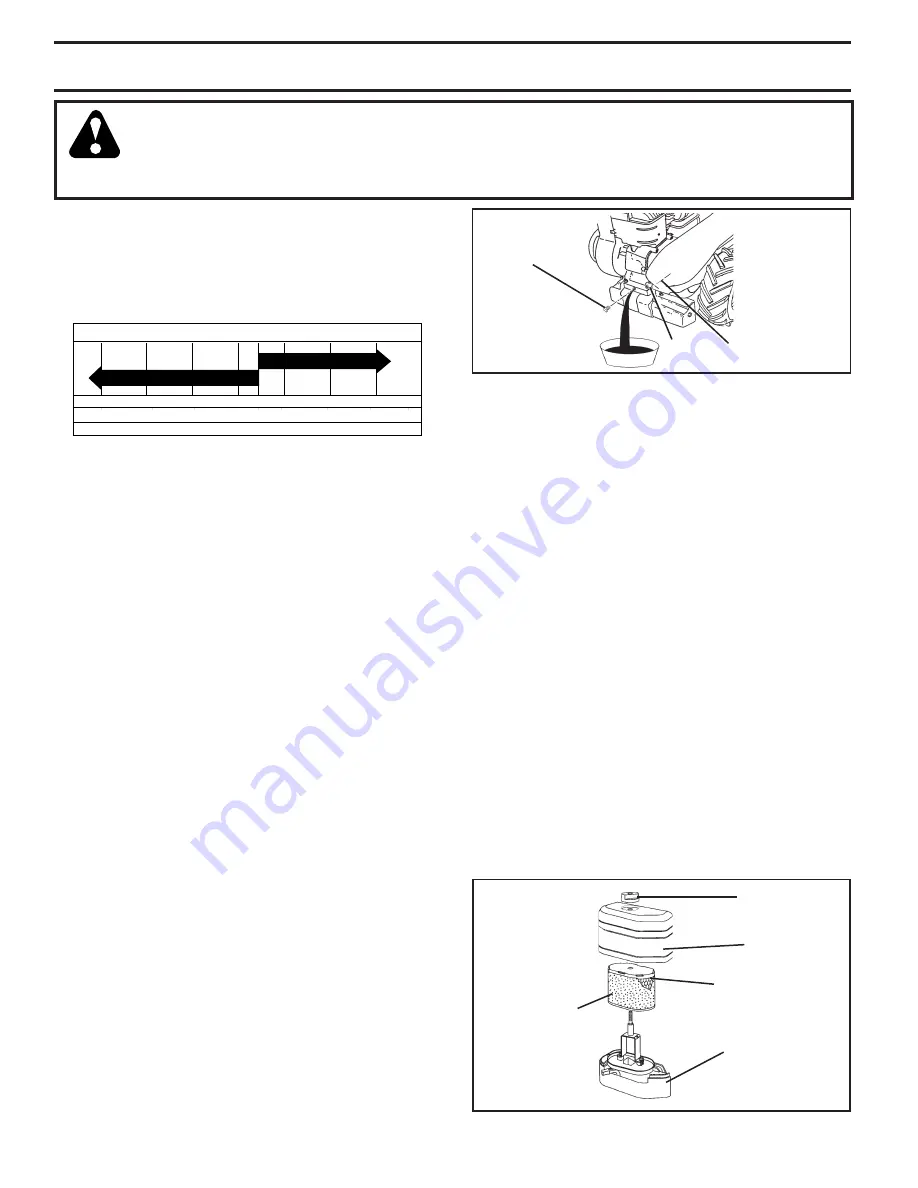
12
MAINTENANCE
OIL FILLER
PLUG
OIL LEVEL
OIL
DRAIN
PLUG
FIG. 16
Disconnect spark plug wire before performing any maintenance (except car bu re tor adjustment) to
prevent accidental start ing of engine.
Prevent fi res! Keep the engine free of grass, leaves, spilled oil, or fuel. Re move fuel from tank
before tipping unit for maintenance. Clean muffl er area of all grass, dirt, and debris.
Do not touch hot muffl er or cylinder fi ns as contact may cause burns.
FIG. 17
TO CHANGE ENGINE OIL (See Figs. 16 and 17)
Determine temperature range expected before oil change.
All oil must meet API service classifi cation SG-SL.
• Be sure tiller is on level surface.
• Oil will drain more freely when warm.
• Use a funnel to prevent oil spill on tiller, and catch oil
in a suitable con tain er.
• Remove drain plug. For easier removal of plug use
7/16 12 Pt. socket with extension.)
• Tip tiller forward to drain oil.
• After oil has drained completely, replace oil drain plug
and tighten securely.
• Remove oil fi ller plug. Be careful not to allow dirt to
enter the engine.
• Refi ll engine with oil. See “CHECK ENGINE OIL LEVEL”
in the Operation section of this manual.
ENGINE
LUBRICATION
Use only high quality detergent oil rated with API service
classifi cation SG-SL. Select the oil’s SAE vis cos i ty grade
according to your expected temperature.
NOTE:
Although multi-viscosity oils (5W-30, 10W-30, etc.)
improve starting in cold weather, these multi-viscosity oils
will result in increased oil consumption when used above
40°F (4°C). Check your engine oil level more frequently to
avoid possible engine damage from running low on oil.
Change the oil after every 25 hours of operation or at
least once a year if the tiller is not used for 25 hours in
one year.
Check the crankcase oil level before starting the engine
and after each fi ve (5) hours of continuous use. Add SAE
30 motor oil or equivalent. Tighten oil fi ller plug securely
each time you check the oil level.
TEMPERATURE RANGE ANTICIPATED BEFORE NEXT OIL CHANGE
SAE VISCOSITY GRADES
-20
0
30
40
80
100
-30
-20
4
20
30
40
F
C
-10
10
60
10W-30 / 5W-30
SAE 30
oil_visc_chart5_e(drt)
FIG. 18
COVER
KNOB
BASE
FOAM
PRECLEANER
COVER
AIR FILTER (See Fig. 18)
Your engine will not run properly using a dirty air fi lter. Clean
the foam pre-cleaner after every 25 hours of op er a tion or
every season. Service paper cartridge every 100 hours of
operation or every season, which ev er occurs fi rst.
Service air cleaner more often under dusty conditions.
• Remove cover screw and cover.
TO SERVICE PRE-CLEANER
• Remove foam pre-cleaner from air cleaner cover.
• Wash it in liquid detergent and water.
• Squeeze it dry in a clean cloth.
• If very dirty or damaged, replace pre-cleaner.
• Reinstall pre-cleaner into air cleaner cover.
• Reinstall cover and secure screw.
TO SERVICE CARTRIDGE
• Carefully remove cartridge to prevent debris from
en ter ing carburetor. Clean base carefully to pre vent
debris from entering carburetor.
• Clean cartridge by tap ping gen tly on fl at surface. If
very dirty or damaged, replace cartridge.
• Re in stall cartridge, cover with pre-cleaner and se cure
with screw.
IMPORTANT:
PETROLEUM SOLVENTS, SUCH AS KER O SENE,
ARE NOT TO BE USED TO CLEAN THE CAR TRIDGE. THEY
MAY CAUSE DETERIORATION OF THE CARTRIDGE. DO NOT
OIL CARTRIDGE. DO NOT USE PRESSURIZED AIR TO CLEAN
OR DRY CARTRIDGE.
AIR CLEANER
CARTRIDGE