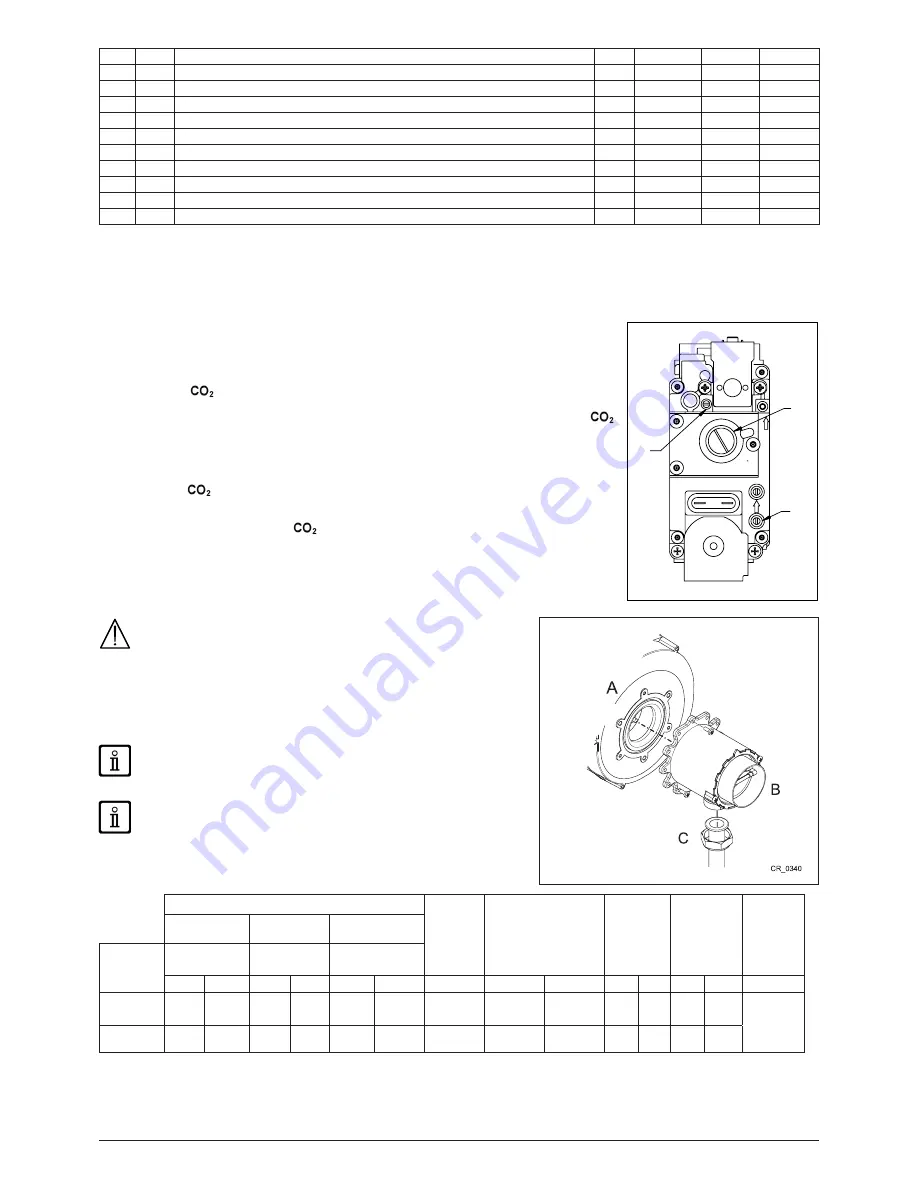
7108686.02 (1-11/12)
16
IN
S
T
A
L
L
E
R
S
e
c
ti
o
n
(e
n
)
MAINTENANCE
P57
7045
Time after maintenance
month
xxx
0
240
P58
6704
View/Hide secondary fault internal code (0=no)
-
1
0
1
BURNER CONTROL
P59
9512
Required ignition speed
rpm
xxx
0
8000
P60
9524
Required minimum operating speed
(low speed)
rpm
xxx
0
8000
P61
9529
Required maximum operating speed
(high speed)
rpm
xxx
0
8000
BOILER CONTROL PANEL PARAMETERS
P62
-
Unit of measurement (1=bar, °C – 2=PSI, °F)
-
1
1
2
P63
-
Control panel operation: (1=central, 0=local)
-
1
0
1
P64
-
Software version
-
xx
0
999
*
see “Accessories not included in supply”
xx
: the value depends on the software version
xxx
: the value depends on the type of boiler
(a)
:
parameters read on the front boiler panel (fixed control panel)
(b)
: parameters read on the Remote Control
15. GAS VALVE COMMISSIONING
To commission the gas valve, enable the commission function as described in section 12.2
and carry out the following operations:
1)
Commissioning
MAXIMUM heat output.
Check that the
measured on the flue duct, with the boiler operating at maximum heat
capacity, matches that indicated in table 2 (allowed tol/- 0.5%). If it does not, turn the
adjustment screw (
V
) on the gas valve. Turn the screw clockwise to decrease the level of
and anti-clockwise to increase it (allowed tol/- 0.2%).
2)
Commissioning
REDUCED heat output
Check that the
measured on the flue duct, with the boiler operating at minimum heat
capacity, matches that indicated in table 2 (allowed tol/- 0.5%). If it does not, remove
the threaded brass cap on the gas valve and turn the adjustment screw (
K
). Turn the screw
clockwise to increase the level of
and anticlockwise to decrease it (allowed tolerance
+/- 0.2%).
15.1 GAS CONVERSION
When converting from natural gas to propane (LPG), before calibrating
the gas valve as described above, replace the venturi assembly ( B) as
indicated in the figure. To achieve this, dismount the gas pipe (thre-
aded nut G1”) and remove the three screws securing the flange. Afterwards,
make sure there are no gas leaks. Modify the parameters (fan rpm) as indicated
in table 2 following the procedure described in section 14.
To simplify commissioning of the gas valve, set the “commissioning
function” directly on the boiler control panel as described in section
12.2.
For cascade ducts, change the parameter P60(a) increasing the num-
ber of fan revolutions (rpm) by 200 (see table in chapter 10.2).
TABLE 2
PARAMETERS - rpm
VENTURI
Ø (mm)
GAS NOZZLES
Ø (mm)
CO
2
Min
(%)
CO
2
Max
(%)
Max. CO
(ppm)
P60 (a)
P30 – P61 (a)
P59 (a)
Boiler
model
Min. power
Max. power
Ignition power
G20
G31
G20
G31
G20
G31
G20-
G31
G20
G31
G20
G31
G20
G31
G20/G31
WH 90
1250
1500
6500 6200
2400
2400
34
5.6 (n°2)
4.5 (n°2) *8,5 *9,9 *9,0
*10
< 250
WH 110
1300
1300
6900 6700
2500
3000
38
6.4 (n°2)
5.0 (n°2)
*9,0 *9,5 *9,2
*10
*
CO
2
with cover closed. Without cover (chamber open) the value is less than
0.2%.
(a)
value read on the boiler front panel display to multiply
x 10
(e.g.: 160 corresponds to 1600 rpm)
Summary of Contents for Sirius two WH
Page 21: ...21 I N S T A L L E R S e c t i o n e n 7108686 02 1 11 12 ...
Page 25: ...25 S E C T I O N C 7108686 02 1 11 12 ...
Page 28: ...7108686 02 1 11 12 28 S E C T I O N F WEATHER COMPENSATION CURVE GRAPHS QAC34 ...
Page 29: ...29 S E C T I O N G 7108686 02 1 11 12 AGU 2 550 CR_0349 CR_0349 AVS 75 ...
Page 30: ...7108686 02 1 11 12 30 S E C T I O N G CG_2482 SAFETY THERMOSTAT Tmax 50 C free contact ...
Page 31: ...31 7108686 02 1 11 12 MODIFIED PARAMETERS Nr VALUE NOTE ...