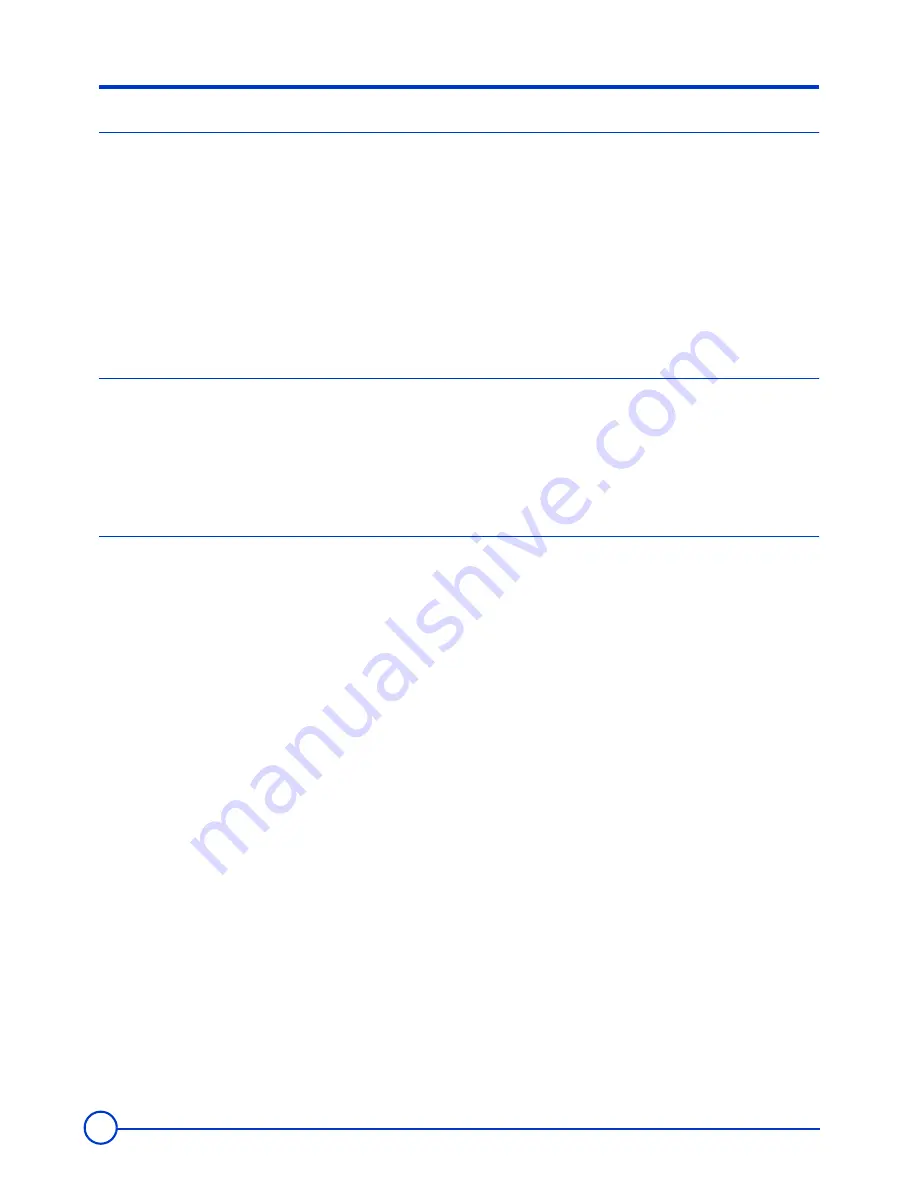
14
NXR4i
09/06/2011 - 300025088-001-B
4.
Installation
4.5 Hydraulic connections
4.5.1
Flushing the system
Installing the boiler in new installations
(installations less than 6 months old)
`
Clean the installation with a universal cleaner to eliminate
debris from the appliance (copper, flaxen thread, flux).
`
Thoroughly flush the installation until the water runs clear and
shows no impurities.
Installing the boiler in existing installations
`
Remove sludge from the installation.
Z
See: Sludge removal
`
Flush the installation.
`
Clean the installation with a universal cleaner to eliminate
debris from the appliance (copper, flaxen thread, flux).
`
Thoroughly flush the installation until the water runs clear and
shows no impurities.
4.5.2
Sludge removal
A tapped Rp 2’’ 1/2 hole with a plug has been provided on the bottom
of the front of the boiler.. Fit a 1/4 turn valve (not supplied) on the
opening to remove the sludge.
Sludge removal leads to the draining of large quantities of water, so
remember to refill the system after the operation.
After this operation, go ahead and fill the installation.
Z
See: Filling the system
never replace a boiler in an existing system without carefully
rinsing the system first. Install a sludge decanting pot on the
return pipe, very close to the boiler.
4.5.3
Hydraulic connection of the heating circuit
Water flow in the boiler
The water flow in the boiler when the burner is operating must
correspond with the following formulae:
- Nominal water flow Qn = 0.86 Pn/20.
- Minimum flow Qmin = 0.86 Pn/45 (this flow also corresponds with
the minimum recycle flow in the boiler).
- Maximum water flow Qmax = 0.86 Pn/5.
Qn = flow in m
3
/h
Pn = Nominal output (full boiler output) in kW.
Connect the flow controller to the terminal blocks
UV
in the
control panel KSF CE. For the control panel KSF, refer to the
instruction manual of the panel.
Operation in cascade
After stopping the burner:
- Timeout required before the order to close a 2 way valve: 3 min.
- Switch a possible shunt pump (located between the boiler and a
butterfly valve) off via the end of run contact of the butterfly valve.
Operation with 2-stage burner
- The water temperature in the boiler is maintained at 50°C or more ;
The first stage must be set to a minimum of 30% of the nominal
stage.
- Operation at modulated low temperature (minimum outlet
temperature: 40°C) ; The first stage must be set to a minimum of
50% of the nominal stage.
Z
Refer to the installation and service manual for the KSF CE
control panel.
Operation with modulating burner
- The water temperature in the boiler is maintained at 50°C or more:
The burner can modulate down to 30% of the nominal stage.
- Operation at modulated low temperature (minimum outlet
temperature: 40°C) ; The burner can modulate down to 50% of the
nominal stage.
Z
Refer to the installation and service manual for the KSF ISR
control panel.