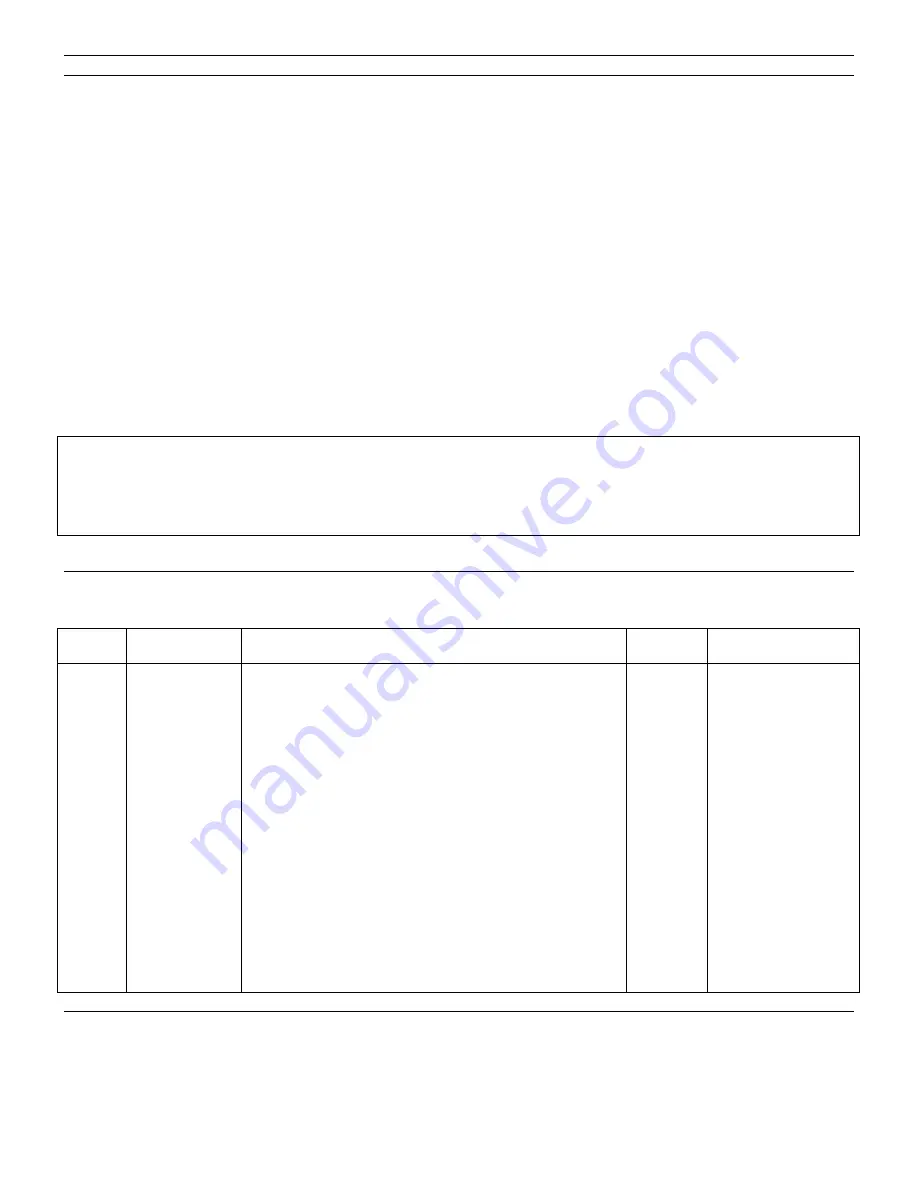
Fault Finding - Page 22
SYMPTOM
UNEXPLAINED SHUT-DOWN OF THE APPLIANCE
This appliance contains an Energy Cut-Off Device which reacts the water in the heat exchanger exceeds the anticipated
temperature limit. Although it is intended to guard against failure of the automatic gas valve, it may be triggered inadvertently
by other causes, especially during the summer months when the inlet water temperature is unusually high.
POSSIBLE CAUSE
SOLUTION
Failure of the appliance thermostat.
Repair or replace.
However, if the energy cut-off device reacts to a slowly closing automatic gas valve, the shut down of the appliance may be
accompanied by noises from the heat exchanger and pipework. The pressure relief valve located on top of the water
governor may also have vented water into the case. In this situation it is possible that STEAM will come out of the hot water
tap when turned on.
POSSIBLE CAUSE
SOLUTION
Excessive resistance of push rod.
Exchange push rod and seals. Lubricate with Dow Corning III
silicone grease and ensure free movement.
IMPORTANT NOTE
To ensure continued safe operation, we recommend that if the pressure relief valve has operated, it should be
replaced immediately
8. SHORT SPARE PARTS LIST - Page 22
Key No
G.C. Part No.
Description.
No. Off.
Makers Part No.
1
284 957
Seal Pack - Chassis to Flue Terminal
1
31/1 2299
11
285 907
Case Assembly
1
10/17543
14
285 910
Case Seal - Self Adhesive Rubber
1
10/1 7501
12
285 908
Viewing Aperture Seal
1
1 0/1 7499
13
285 909
Viewing Aperture Glass
1
10/17500
40
285 513
InjectorN.G.1.2mm
14
19/12196
43
285 678
Flame Safety Device Assembly
1
10/13477
54
285 930
Thermocouple - Special
1
10/17461
53
285 929
Thermocouple Connection - Special
1
10/1 7790
52
397 688
Interrupter Insert
1
10/1 3846
55
285 931
Electrode Assembly
1
10/1 7493
58
285 679
Pilot Injector - Special
1
19/1 2690
44
393 492
PiezoUnit-RV1174
1
10/11935
59
285 934
Igniter ‘IGN’ Button
1
10/1 7507
60
285 935
Starter ‘ON’ Button Assembly
1
10/17540
61
285 936
Stop ‘OFF’ Button Assembly
1
10/1 7541
83
285 944
Diaphragm Assembly
1
10/1 7534
114
285 691
Thermostat Assembly
1
10/13486
62
285 937
Energy Cut-Off Device Assembly - Includes Grommets
1
10/1 7792
78
285 942
Pressure Relief Valve Assembly
1
10/17866