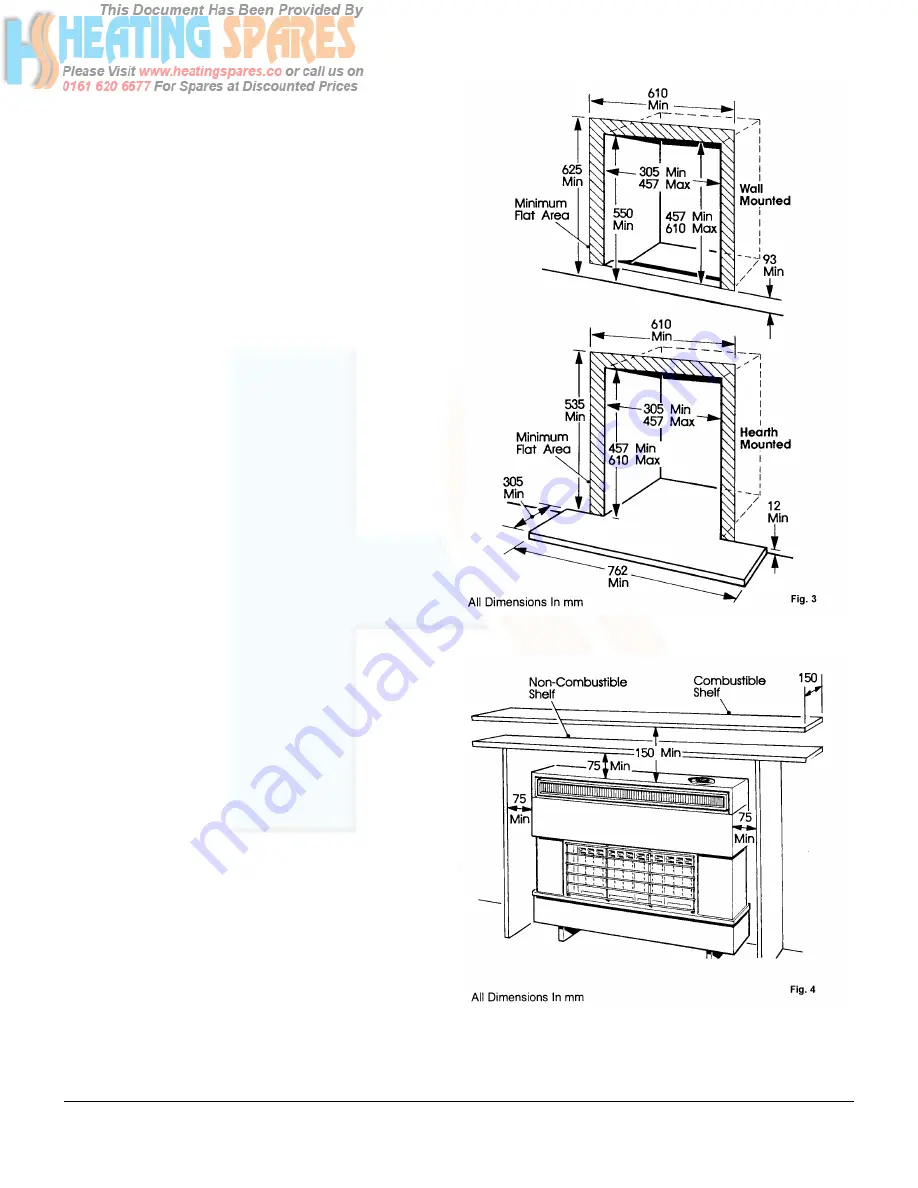
Supplied By www.heating spares.co Tel. 0161 620 6677
Part No. 900/9350/1
Installation Requirements 5
3. Installation Requirements - Page 5
3.3. Combustible Wall
If the wall against which the fire is to be installed has
combustible cladding or surround, the following conditions
must be met:
Note:
Certain types of wall coverings may be prone to
discolouration.
a)
The cladding must fit snugly to the wall face, any air
cavities must be sealed to prevent air leakage into the
chimney, which would spoil the flue pull.
b)
Any combustible cladding (i.e. Wallpaper, etc) must not
extend more than 13mm behind the outer case of the
fire.
c)
The cladding material must not extend inside the area
of the fireplace opening. Under no circumstances can it
be present inside the fireplace openings or flue
passage, or in any position which will allow direct
contact with the hot flue products.
d)
The fire must discharge all its products inside the
fireplace opening in the wall. Use a flue spigot
extension (not Supplied) if necessary.
e)
The engagement points for the fixing screws must be
adequate to support the fire solidly in all circumstances
through its life.
f)
The minimum flat area is required to ensure that a
satisfactory seal can be made between the fireplace
and the appliance.
3.4. Fireplace Opening
For the dimensions of both wall mounted and
floor mounted fires, see Fig. 3.
3.5. Fire Surrounds & Shelves
a)
This fire can be fitted to a non-combustible fire surround
and hearth or a propriety fire surround and hearth with a
1000C rating.
b)
The surround must comply with the same minimum flat
area requirements as the fireplace opening. See Fig. 3.
The surround and hearth must be sealed to the floor &
wall to prevent air entrainment.
c)
The hearth MUST be to the dimensions shown in Fig. 3.
and located centrally about the fireplace opening.
d)
No permanent restriction should be placed within 75mm
of either side or top of the fire this will enable the outer
case to be removed for installation & servicing.
A combustible shelf can be fitted a minimum of 150mm
above the top point of the fire
provided that it does not stand out from the wall more than
150mm.
A shelf of non-combustible material up to 150mm deep may
be fitted above with a
minimum space of 75mm between the top
of the fire. See Fig 4.