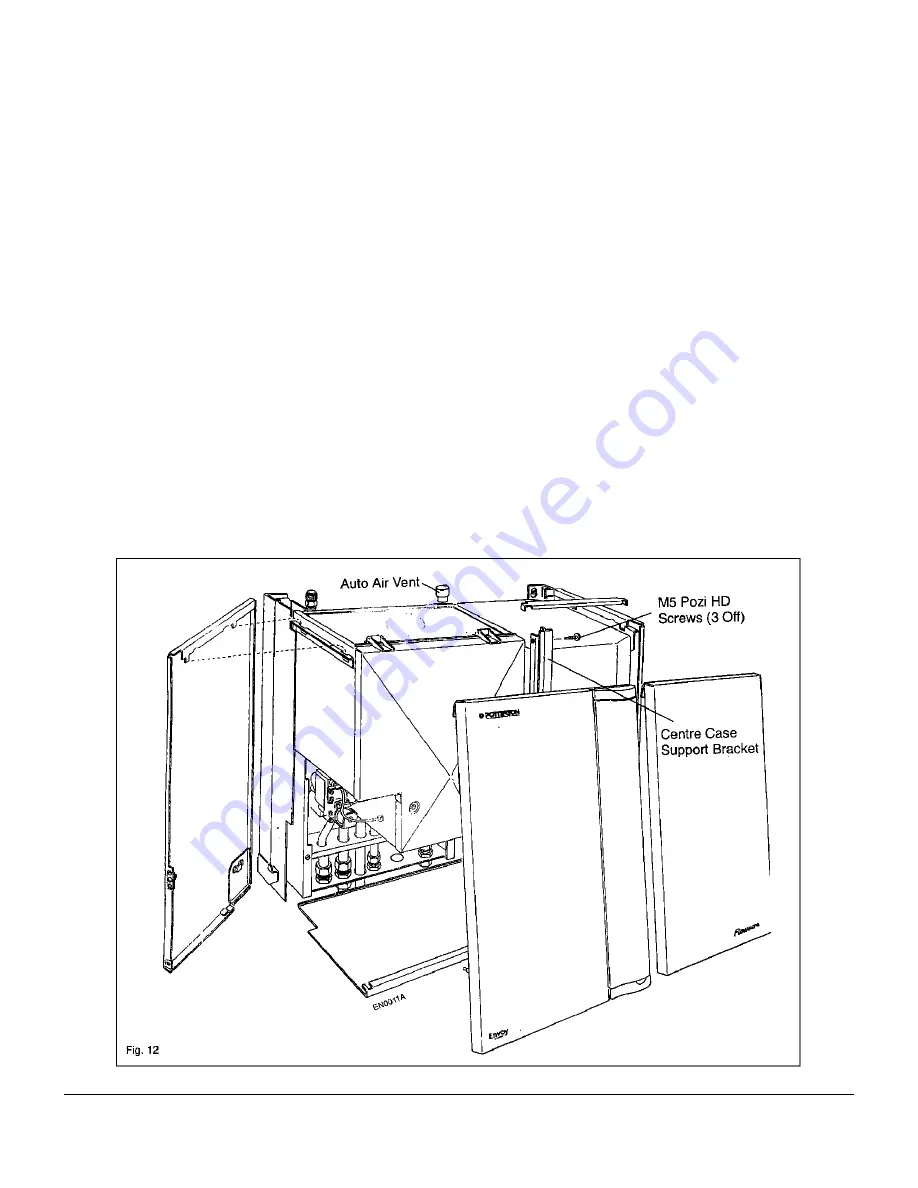
Commissioning
Publication No. 559779
18
Commissioning – Page 18
Final Assembly
Remove the three M5 pozi head screws from the right hand
side of the boiler as shown, Secure the centre case support
bracket using the three screws previously removed. Attach
casing side panels onto the boiler as illustrated (Fig. 12)
ensuring that the three lugs on each panel are correctly
located. Slide in the bottom panel and push fully home.
Engage hooks on the top rear of the front panel into the slot in
the top front corner of each side panel. Lower the front panel
to engage brass studs into the retaining clips, press fully home
to lock panel into position.
External Controls
Check that any other external control connected in the
system, such as timers and thermostats, control the boiler
as required.
User's Instructions
A User's Guide is provided with this boiler but the
householder must have the operation of the boiler and
system explained by the installer. The householder must
also be advised of the importance of annual servicing and
of the precautions necessary to prevent damage to the
system and building, in the event of the system remaining
out of commission in frost conditions.
Information must also be passed to the customer on the
type of corrosion inhibitor that has been added to the
system and of the need to maintain the correct
concentration levels as recommended by the
manufacturer.
Summary of Contents for Envoy Flowsure
Page 4: ...Technical Data Publication No 559779 4 Technical Data Page 4 Fig 2 ...
Page 13: ...Publication No 55977 Installation 13 Installation Page 13 ...
Page 32: ...Fault Finding Chart Publication No 559779 32 Fault Finding Page 32 ...
Page 33: ...Publication No 55977 Fault Finding Chart 33 Fault Finding Page 33 ...
Page 34: ...Fault Finding Chart Publication No 559779 34 Fault Finding Page 34 ...
Page 36: ...Boiler Wiring Layout Publication No 559779 36 8 Boiler Wiring Layout Page 36 ...