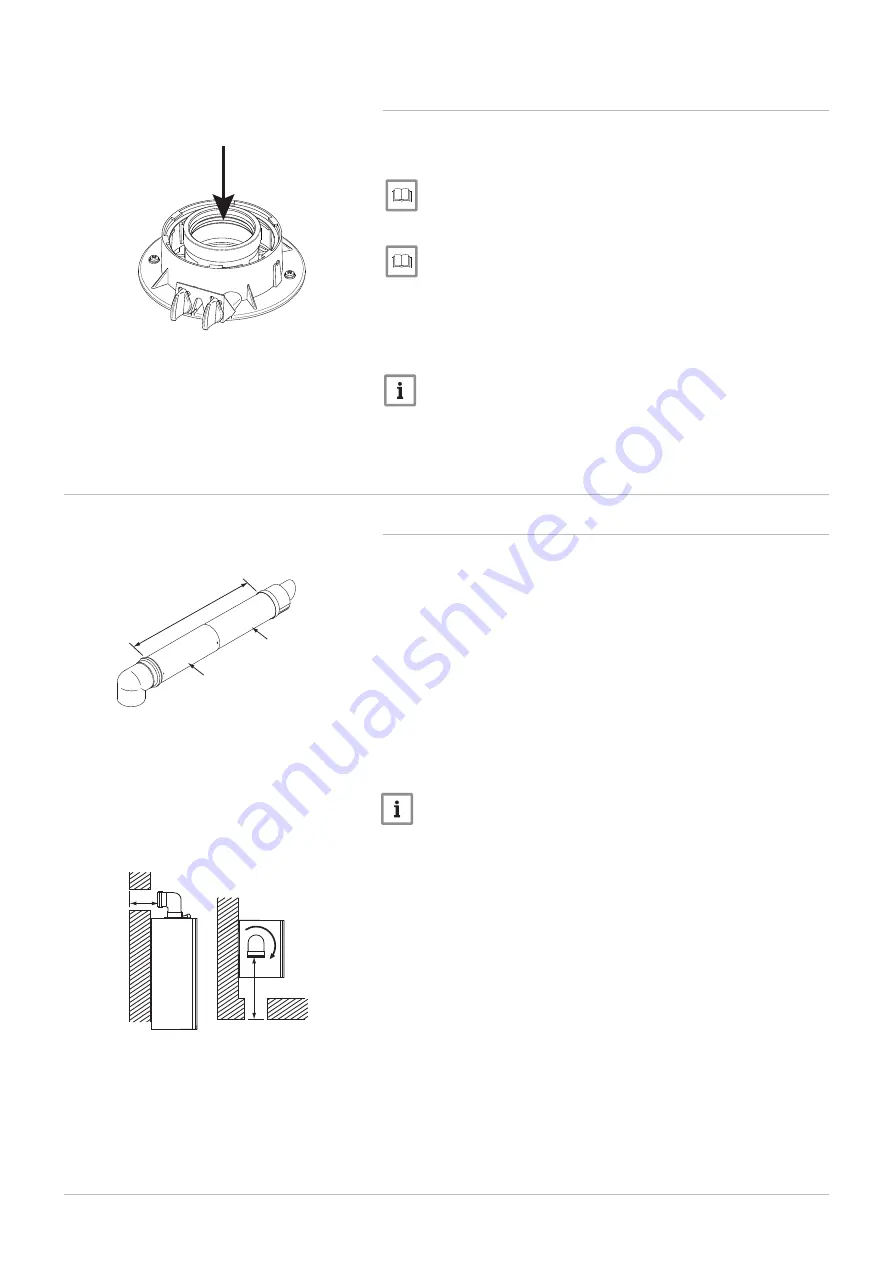
6.2.2
Connecting the condensate drain
1. Remove the blanking cap, and using the elbow supplied, connect the
condensate drain pipework to the boiler condensate trap outlet pipe.
See
Ensure the discharge of condensate complies with any national or
local regulations in force (see HHIC recommendations).
See
2. The elbow will accept 21.5mm (
3
/
4
in) plastic overflow pipe which
should generally discharge internally into the household drainage
system. If this is not possible, discharge into an outside drain is
acceptable.
Important
The boiler condensate trap should be primed by pouring
approximately 300ml of water into the flue spigot. Do not allow any
water to fall into the air inlet.
6.3
Air supply/flue gas connections
6.3.1
Connecting the flue/chimney
HORIZONTAL TELESCOPIC FLUE (concentric 60/100)
1
315mm to 500mm
2
Connection assembly
3
Terminal assembly
There are two telescopic sections, the terminal assembly and the
connection assembly, a roll of sealing tape and two self tapping screws. A
93° elbow is also supplied.
The two sections can be adjusted to provide a length between 315mm and
500mm when measured from the flue elbow (there is 40mm engagement
into the elbow).
1. Locate the flue elbow on the adaptor at the top of the boiler. Set the
elbow to the required orientation.
Important
The flue elbow is angled at 93° to ensure a fall back to the boiler.
2. Measure the distance from the outside wall face to the elbow. This
dimension will be known as " X" .
3. If the distance from the flue elbow to the outside face of the wall is
less than 250mm the connection assembly can be discarded and the
terminal assembly fitted directly into the elbow.
4. In instances where the dimension " X" is between 250mm and 315mm
it will be necessary to shorten the terminal assembly by careful cutting
to accommodate walls of these thicknesses.
Fig.28
Pour 300ml of water into flue spigot
PN-0000602
Fig.29
Telescopic flue
PN-0000462
3
1
2
Fig.30
Flue dimension X
PN-0000463
X
X
6 Installation
36