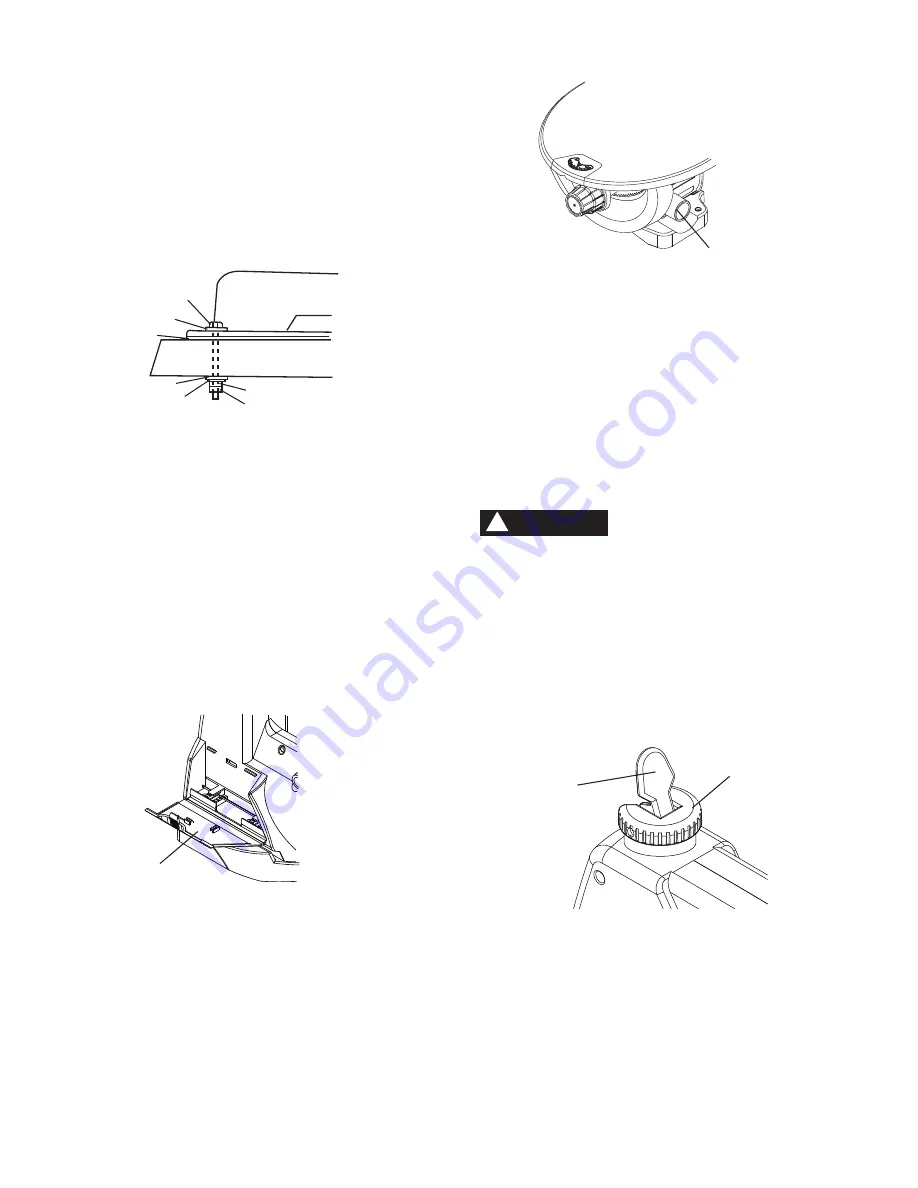
13
MOUNTING SCROLL SAW TO WORK SURFACE
(FIG. C)
1. If mounting the scroll saw to a workbench, a solid
wood bench is preferred over a plywood board to
reduce noise and vibration.
2. The hardware to mount this saw is NOT supplied with
the saw. The hardware as shown in Fig. C should be
used:
Fig. C
1. (3) Hex head bolts; length as required
2. (6) Flat washers
3. Foam pad or carpet (optional)
4. (3) Lock washers
5. (3) Hex nuts
6. (3) Jam nuts
BLADE STORAGE (FIG. D)
Blade storage is located on the left rear side of the scroll
saw body. Pull out the blade storage door (1) to open.
The compartment can conveniently store your hex
wrenches and both Pin-end and Plain-end blades.
Fig. D
SAWDUST COLLECTION PORT (FIG. E)
This scroll saw will accept a hose or vacuum accessory
(not provided) to be connected to the port (1) on the
right side of base. If excessive sawdust buildup occurs
inside the base, use a wet /dry vacuum cleaner or
manually remove sawdust by removing the screws on
the left side of saw. Reattach the metal plate and screws
before starting the saw. This will keep your saw cutting
efficiently.
1
2
3
5
6
2
4
1
Fig. E
BLADE REMOVAL AND INSTALLATION
PLAIN-END BLADE REMOVAL AND INSTALLATION
This scroll saw accepts 5-inch (127 mm) Plain-end or
Pin-end blades to cut a wide variety of materials.
Plain-end type blades are recommended whenever fine,
accurate and intricate work is being performed on 3/4 in.
(19 mm) or thinner material. It will take slightly longer to
assemble the blade and blade tension, but you will also
be able to use finer blades for cutting a thinner kerf.
To avoid injury from accidental starting, always turn
the switch OFF (O) and remove power cord plug
from power source before removing or replacing the
blade.
Plain-end blade removal (FIG. F, G, H)
1. To remove the blade (1-Fig. G), loosen the blade
tension by lifting the quick release tension lever
(2-Fig. F).
Fig. F
2. Loosen the upper blade holder (3) by turning the
blade holder lock knob (4) counterclockwise. (Fig. G)
NOTE:
The hex set screw (5) on the left side is used
for fine adjustments and is only adjusted if the blade
is not perpendicular to the table.
1
WARNING
!
2
1
Summary of Contents for PCB370SS
Page 9: ...9 UNPACKING YOUR SCROLL SAW OFF A B E H F G C D...
Page 27: ...27 NOTE...