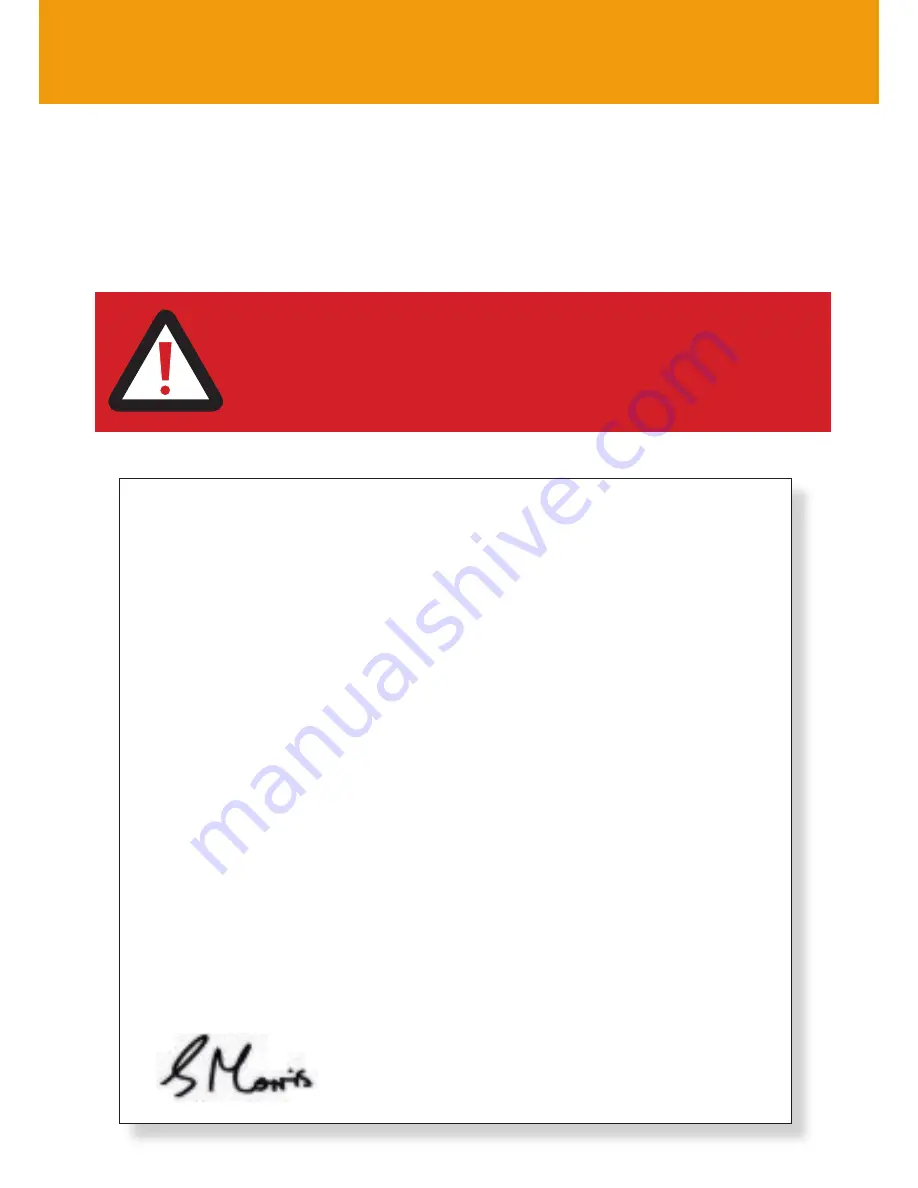
9
CE Certificate of Conformity
EC Declaration of Conformity
Portek Ltd, Bryn Hall, Knolton Bryn, Overton on Dee,Wrexham, LL13 0LF declare that, in ac-
cordance to the following directives,
2006/42/EC (Machinery Directive)
2004/108/EC (EMC Directive)
the “QuikSplit 7” has been designed to comply with the relevant sections of the below
BS EN ISO standards:-
12100-2: 2003
14121-1: 2007
13857: 2008
953:1997 + A1: 2009
1037: 1995 +A1: 2008
BS EN 609-1:2017
The unit complies with all applicable Essential Requirements of the Directives.
Declaration made by Stephen Morris, Designer
on 18/01/2017.
Excessive force will cause the trip switch to operate, protecting
the motor from damage. After a short period, usually less than
a minute, the trip can be rest by pressing. The unit can then be
restarted with the green switch as normal.
DISCONNECT POWER SUPLY BEFORE ATTEMPTING TO
REMOVE STUCK LOGS OR ANY ISSUES WITH RAM
POSITION AFTER ENCOUNTERING PROBLEMS