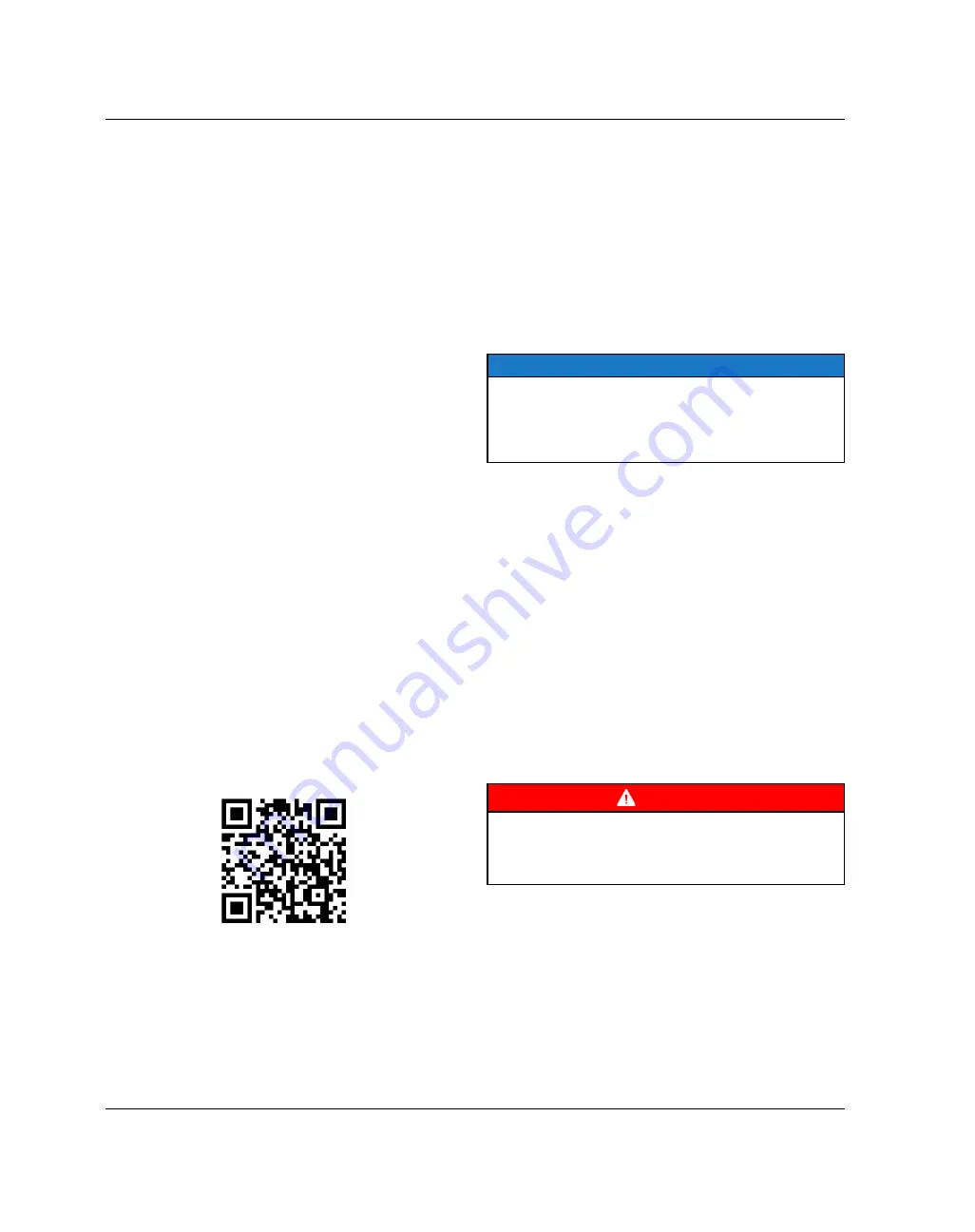
11.12
TESTING FOR A SHORT TO VOLTAGE
There are three possible short to voltage causes:
1. Internal electronic component short.
2. Harness chaffing leading to contact of the circuit
being diagnosed to one with B + or a different
reference voltage.
3. Moisture in a connector or component.
TESTING PROCEDURE
1. Consult the wiring diagram. Determine which circuit
you will be testing.
2. Ensure that any static voltage checks advised in
relation to the DTC or concern you are diagnosing
have been performed and are in spec.
3. Ensure you have checked continuity of the circuit. ,
4. Ensure you have checked for a short to ground. ,
5. Ensure that neither end of the circuit is connected.
6. Set your DMM to DC volts.
7. Connect one meter lead securely to the battery
negative post.
8. Connect the other lead to either end of the
disconnected circuit. Ensure you are using the correct
adapter., page 11.9
9. If there is voltage present, the harness is damaged
and should be repaired or replaced. You may need to
remove the protective tape and tubing to inspect.
10. If the DMM reads 0 volts, the concern may be in a
component related to the circuit. If so, checking
internal continuity of non-electronic components may
reveal the concern, but diagnosis at this point may
require using known good parts.
For a video demonstration, scan the QR code below, or
right click it and select “open in new tab”.
TESTING FOR INTERMITTENT CONDITIONS
Intermittent conditions are very difficult to diagnose, as
when you are testing the circuit, you may not have the
circuit failing to indicate where the issue is. Intermittent
electrical failures are almost always related to a poor
connection that only goes open in specific situations,
such as going over a certain kind of bump, at a certain
temperature, or when the machine is torque loaded in
one way.
Here is a list of possible failures that can be associated
with an intermittent electrical failure:
• Loose female terminal in an electrical connector.
NOTE
If the terminals in question are the correct size/series,
always use PV–43526 to test the drag when inserting
and removing the test terminal adapters. Compare the
effort to the drag against the known good tester
terminal for reference.
• Poor terminal to wire crimp.
• Terminal crimp that occurred at least partially on
insulation instead of the conductor wire strands.
• Terminal fretting corrosion
• Contamination/moisture corrosion
• A full or partial break of the conductor wires in the
insulation, with or without visible insulation damage.
• Improper routing, especially when it leads to chaffing
or heat damage, especially near exhaust.
You may need to use different techniques to duplicate
these concerns. These include but are not limited to:
• Moving the harness by wiggling it or flexing certain
areas.
• Pulling at or near the suspected connector.
• Pushing in different directions to flex the connector
body and try to isolate poor connections.
• Changing the temperature. This can be accomplished
with either heat guns or cold air guns.
WARNING
Always exercise caution when using these tools, and
use them for short periods of time when changing the
temp of an area. Failure to do so can lead to Serious
injury and/or damage to the machine.
Summary of Contents for Sportsman 850 Touring EPS
Page 4: ......
Page 6: ......
Page 72: ...2 40 NOTES MAINTENANCE ...
Page 78: ...3 6 OIL FLOW DIAGRAM ENGINE COOLING SYSTEM ...
Page 93: ...3 3 21 WATER PUMP ASSEMBLY TORQUE SPECIFICATIONS ENGINE COOLING SYSTEM ...
Page 94: ...3 22 STATOR COVER ASSEMBLY TORQUE SPECIFICATIONS ENGINE COOLING SYSTEM ...
Page 100: ...3 28 VALVE COVER ENGINE COOLING SYSTEM ...
Page 101: ...3 3 29 CAMSHAFT CARRIER CAMSHAFT ROCKER ARM ENGINE COOLING SYSTEM ...
Page 102: ...3 30 CYLINDER HEAD VALVES INTEGRATED THROTTLE BODY ENGINE COOLING SYSTEM ...
Page 103: ...3 3 31 VALVE AND SPRING HEIGHT DETAIL SPM850 ENGINE COOLING SYSTEM ...
Page 104: ...3 32 VALVE AND SPRING HEIGHT DETAIL SPM1000 ENGINE COOLING SYSTEM ...
Page 105: ...3 3 33 PISTON CONNECTING ROD ENGINE COOLING SYSTEM ...
Page 106: ...3 34 CRANKSHAFT ENGINE COOLING SYSTEM ...
Page 107: ...3 3 35 CRANKCASE ENGINE COOLING SYSTEM ...
Page 108: ...3 36 CRANKCASE UPPER ENGINE COOLING SYSTEM ...
Page 109: ...3 3 37 BALANCE SHAFT BALANCE SHAFT TIMING ENGINE COOLING SYSTEM ...
Page 110: ...3 38 CRANKCASE LOWER WITH OIL PUMP ENGINE COOLING SYSTEM ...
Page 111: ...3 3 39 STATOR COVER FLYWHEEL WATER PUMP COUPLER ENGINE COOLING SYSTEM ...
Page 112: ...3 40 WATER PUMP WATER PUMP COUPLER STATOR ENGINE COOLING SYSTEM ...
Page 113: ...3 3 41 DRIVE COUPLER REAR STARTER GEAR ENGINE COOLING SYSTEM ...
Page 141: ...3 3 69 CRANKCASE ASSEMBLY UPPER ENGINE COOLING SYSTEM ...
Page 143: ...3 3 71 BALANCE SHAFT TIMING ENGINE COOLING SYSTEM ...
Page 145: ...3 3 73 CRANKCASE SEALANT AND TORQUE VALUES ENGINE COOLING SYSTEM ...
Page 154: ...3 82 NOTES ENGINE COOLING SYSTEM ...
Page 160: ...4 6 FUEL TANK FUEL TANK ASSEMBLY VIEW FUEL SYSTEM ...
Page 170: ...4 16 EFI SYSTEM LAYOUT EFI SYSTEM ASSEMBLY VIEW FUEL SYSTEM ...
Page 204: ...4 50 NOTES FUEL SYSTEM ...
Page 217: ...5 5 13 DRIVE CLUTCH SERVICE DRIVE CLUTCH EXPLODED VIEW ALL MODELS PVT SYSTEM ...
Page 245: ...6 6 11 Primary Shaft Rear Output Shaft Reverse Shaft Coupler Input Shaft TRANSMISSION ...
Page 246: ...6 12 Cam Shift Shaft Bellcrank Shift Shaft TRANSMISSION ...
Page 254: ...6 20 TRANSMISSION EXPLODED VIEW TRANSMISSION ...
Page 330: ...7 74 NOTES FINAL DRIVE ...
Page 338: ...8 8 STEERING EPS STEERING ASSEMBLY VIEW EPS MODELS STEERING SUSPENSION ...
Page 372: ...8 42 NOTES STEERING SUSPENSION ...
Page 377: ...9 9 5 BRAKE SYSTEM ASSEMBLY VIEWS SPORTSMAN SCRAMBLER 850 BRAKE SYSTEM BRAKE SYSTEM ...
Page 378: ...9 6 SPORTSMAN SCRAMBLER 1000 BRAKE SYSTEM BRAKE SYSTEM ...
Page 379: ...9 9 7 SPORTSMAN SCRAMBLER INTERNATIONAL BRAKE SYSTEM BRAKE CALIPER EXPLODED VIEW BRAKE SYSTEM ...
Page 381: ...9 9 9 BRAKE SYSTEM ...
Page 436: ...11 22 INSTERMENT CLUSTER TROUBLESHOOTING INSTRUMENT CLUSTER KEY OFF NO POWER ELECTRICAL ...
Page 437: ...11 11 23 INSTRUMENT CLUSTER KEY ON NO POWER ELECTRICAL ...
Page 438: ...11 24 INSTRUMENT CLUSTER NO HIGH BEAM INDICATOR ELECTRICAL ...
Page 439: ...11 11 25 INSTRUMENT CLUSTER NO INCORRECT FUEL LEVEL ELECTRICAL ...
Page 492: ...11 78 EPS TROUBLESHOOTING ELECTRICAL ...
Page 500: ...11 86 NOTES ELECTRICAL ...