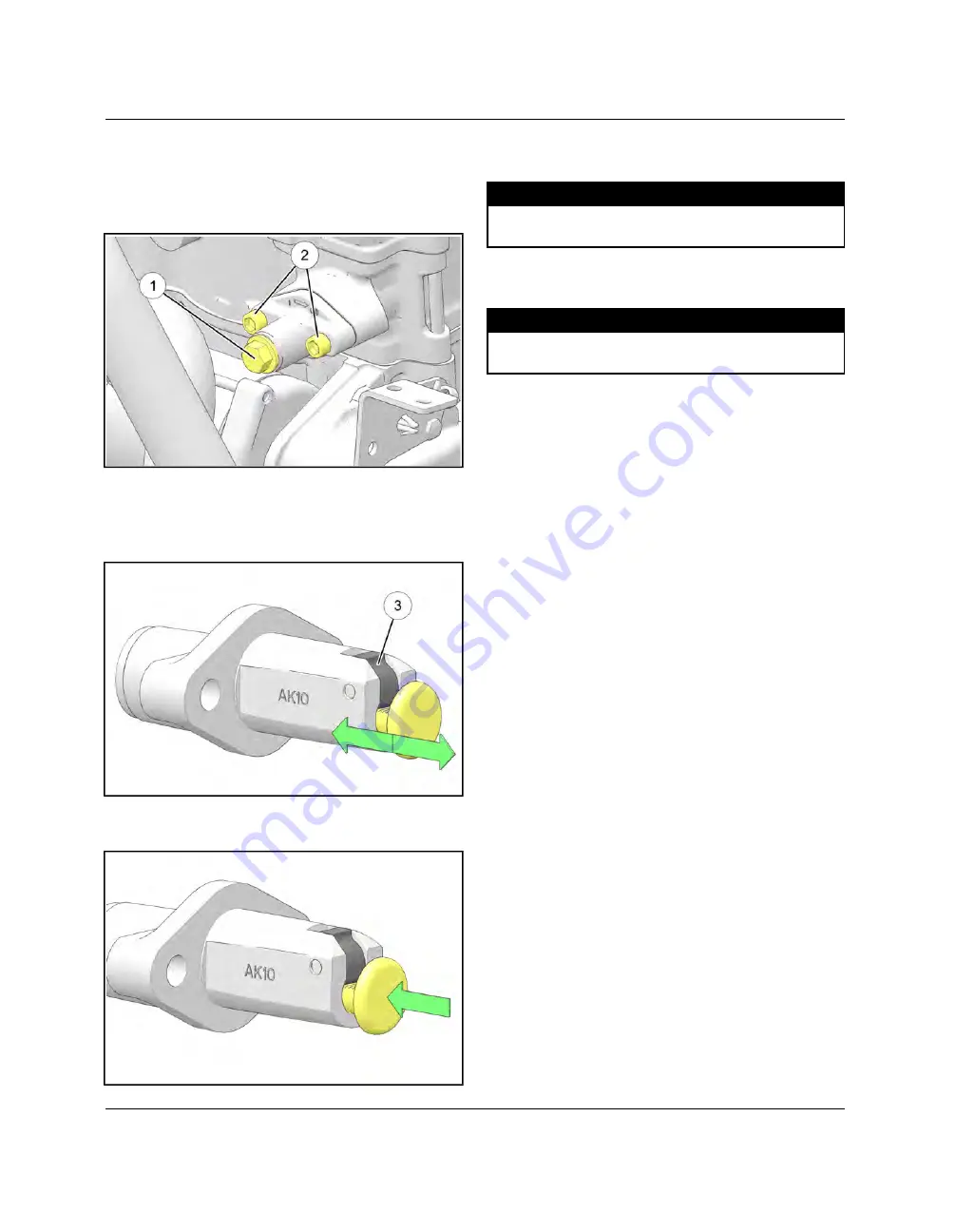
2.20
9929375 R02 - 2016-2019
GENERAL
/
GENERAL 4
Service Manual
© Copyright Polaris Industries Inc.
CAM CHAIN TENSIONER INSPECTION
1. Locate the cam chain tensioner on the MAG side of
the engine near the starter.
2. Remove the plunger bolt
q
and the spring.
3. Remove the two tensioner mounting bolts
w
.
4. Push on the tensioner lock
e
and manually move the
plunger in and out. It should move freely. If it does not
move freely, replace the tensioner assembly.
5. Retract the plunger all the way in and install into the
cylinder.
6. Install the two mounting bolts. Torque fasteners to
specification.
TORQUE
Tensioner Mounting Bolts:
7 ft-lb (10 Nm)
7. Install
the
plunger
bolt.
Torque
fastener
to
specification.
TORQUE
Plunger Bolt:
15 ft-lb (20 Nm)