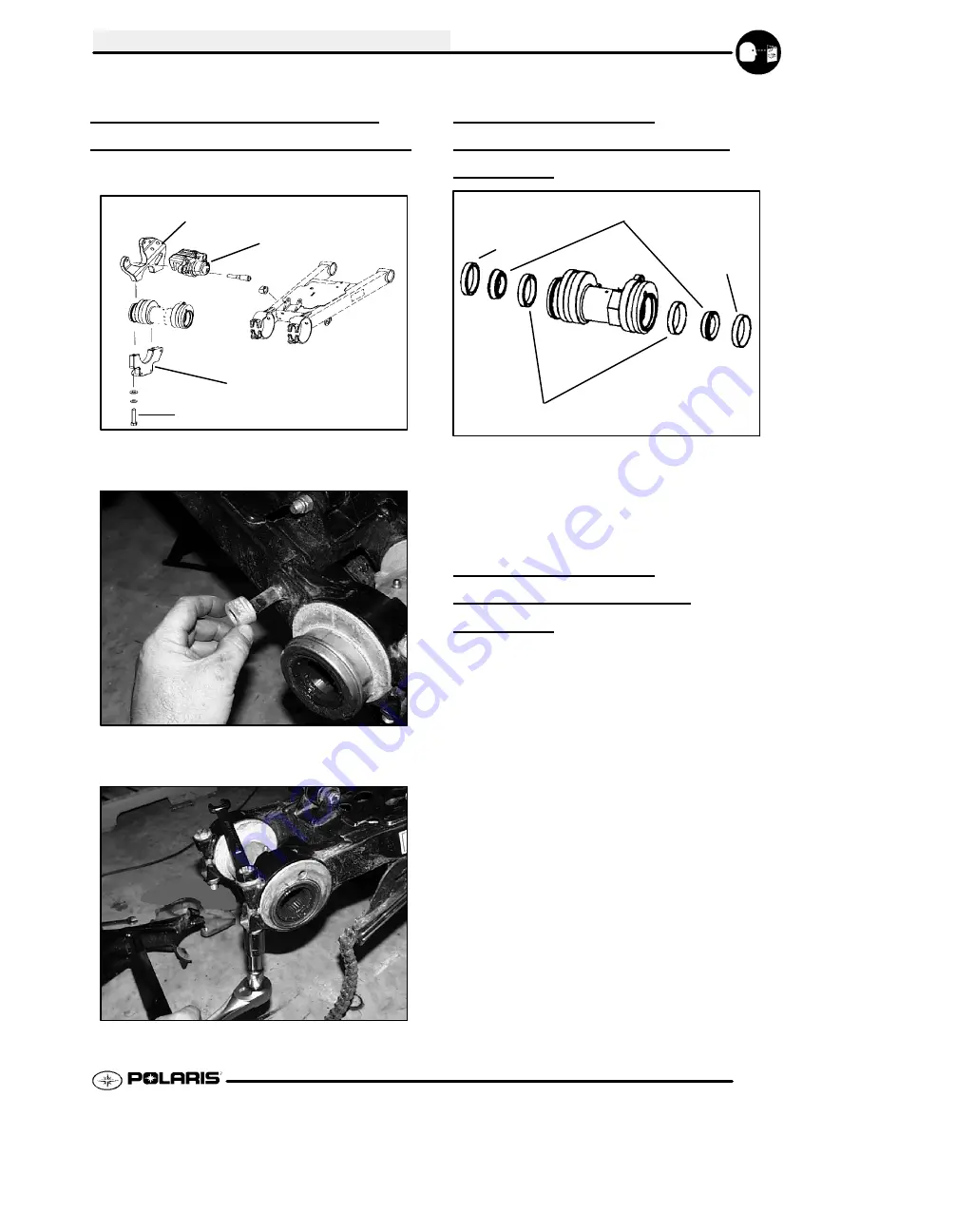
GENERAL INFORMATION
7.27
CONCENTRIC SWINGARM
MIDDLE HOUSING REMOVAL
1. Remove middle axle. (See Page 7.20)
Lower
Caliper Mount
Upper
Caliper Mount
Caliper
Mount Bolts
2. Remove the upper and lowerbrake caliper
mounting brackets.
3. Remove brake caliper pivot bushing from stud.
NOTE:
Flange inward as shown.
4. Loosen pinch bolts and remove middle axle
housing.
MIDDLE HOUSING
DISASSEMBLY/BEARING
SERVICE
Seal
Bearing
Bearing Race
Seal
1. Remove seals from housing.
2. Remove bearings.
3. Drive bearing race out from opposite sides.
4. Inspect housing for cracks or wear. Replace if
damaged.
MIDDLE HOUSING
ASSEMBLY/BEARING
SERVICE
1. Drive in new bearing race with brass drift.
2. Lubricate and install new tapered bearings.
3. Lubricate and install new seals.
Summary of Contents for 2004-2005 Sportsman 6x6
Page 1: ...SPORTSMAN 6X6 6 59 0 18 31 504 SPORTSMAN 6X6 6 59 0 18 31 504...
Page 58: ...MAINTENANCE 2 38 NOTES...
Page 78: ...GENERAL INFORMATION 3 20 CYLINDER HEAD EXPLODED VIEW EH50PL EH50PL...
Page 126: ...GENERAL INFORMATION 4 14 NOTES...
Page 142: ...GENERAL INFORMATION 5 16 NOTES...
Page 198: ...GENERAL INFORMATION 7 30 NOTES...
Page 276: ...ELECTRICAL 10 48 NOTES...
Page 277: ...ELECTRICAL WIRING DIAGRAM 2004 SPORTSMAN 6X6...
Page 278: ...ELECTRICAL WIRING DIAGRAM 2004 SPORTSMAN 6X6 NOTES...
Page 279: ...ELECTRICAL WIRING DIAGRAM 2005 SPORTSMAN 6X6 BUILT BEFORE JULY 12 2004...
Page 280: ...ELECTRICAL WIRING DIAGRAM 2005 SPORTSMAN 6X6 BUILT BEFORE JULY 12 2004 NOTES...
Page 281: ...ELECTRICAL WIRING DIAGRAM 2005 SPORTSMAN 6X6 BUILT AFTER JULY 12 2004...
Page 282: ...ELECTRICAL WIRING DIAGRAM 2005 SPORTSMAN 6X6 BUILT AFTER JULY 12 2004 NOTES...
Page 289: ...31 504 3ULQWHG LQ 86...