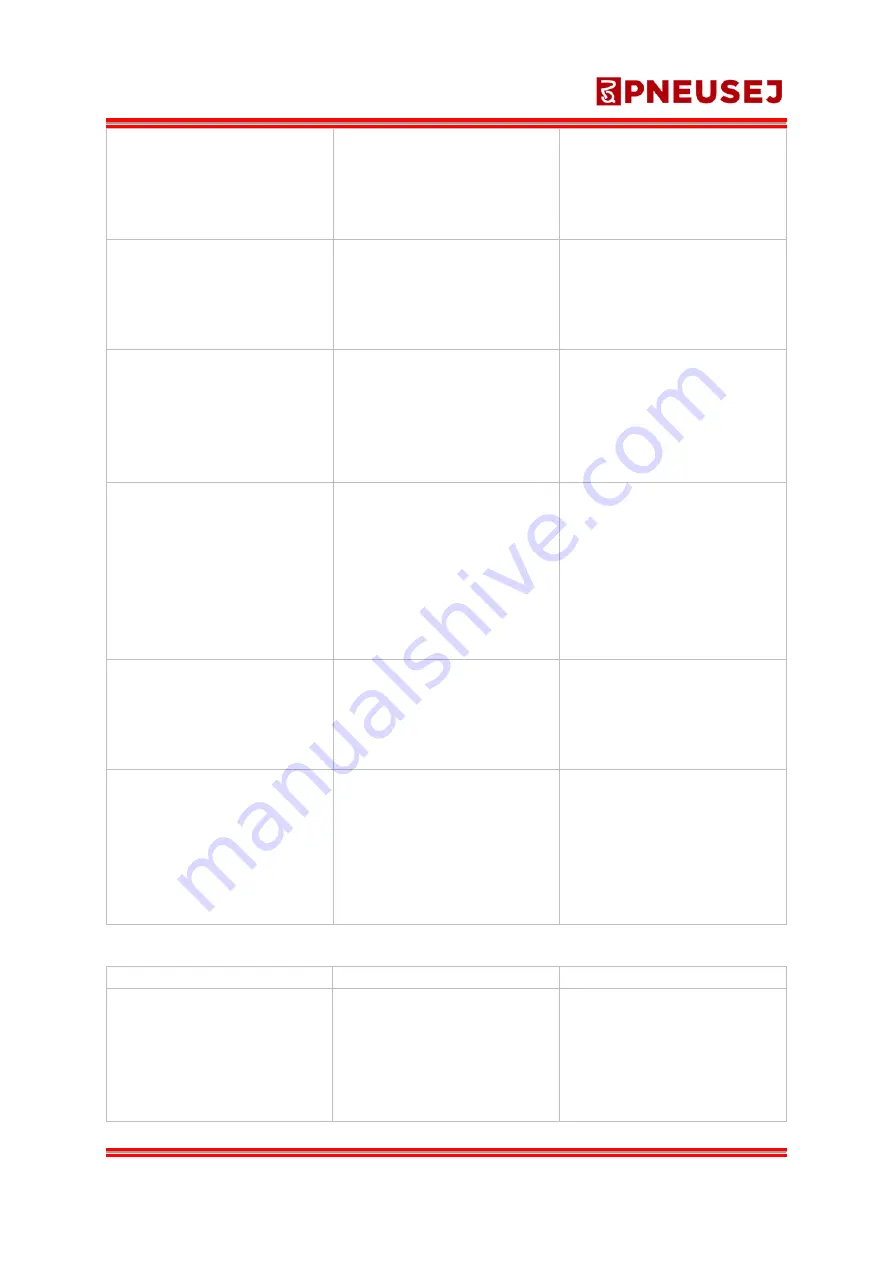
Amount of seed changes by
itself.
Seed has drawn moisture.
Crank on seed rate setting is
moving too easily
Seed hopper has to be
emptied overnight.
Tighten the nut on the
crank.
In case of fine seeding and
microdosing, seeding
amount doesn’t go under 4
-
5 kg/ha.
Sealing cuff on dosing unit is
weared.
The sealing cuff doesn’t fit
correctly with the roller.
Replace sealing cuff.
Place sealing cuff correctly.
Seeding amount is too high.
High speed in calibration
test.
Wrongly fitted red tooth-
wheel for microdosing.
Do calibration test with
maximum 1 rotation per
second
.
Turn on microdosing
correctly.
Seeding amount is too high
or too low.
Wrongly set value.
Mistake in seed weight.
Set the value correctly.
Check weighing scale
functionality.
Don’t count weight of
box/bag.
Check weight unit on
weighing scale.
Seeding amount is too low.
Microdosing is on.
Chambers are dirty.
Brush doesn’t move.
Turn off microdosing.
Clean chambers.
Clean or replace the brush.
No seed comes to any seed
coulter.
Injector is clogged.
Fan is off.
Restriction flap on the fan is
closed.
Remove clogging and check
fan speed.
Turn on the fan.
Open restriction flap.
Seeding coulters
Problem
Cause
Fix
Tramlines are not set.
Too low power on
connector.
Electromagnetic closing
valve doesn’t
switch.
Check connection by
corrosion.
Change electromagnetic
closing valve.
Summary of Contents for Venga 400
Page 1: ......
Page 14: ...Machine description Venga...