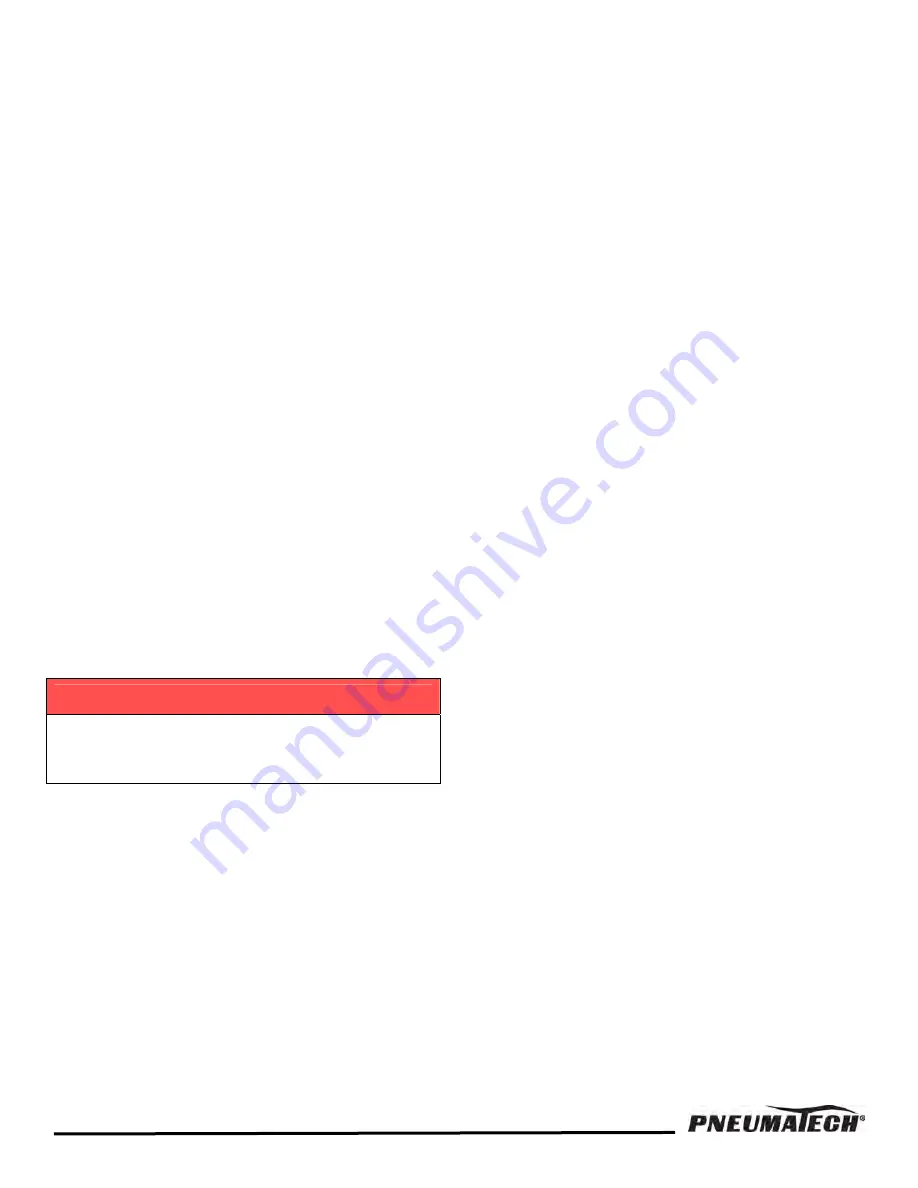
PH/EH SERIES HEATLESS AIR DRYER
INSTALLATION & OPERATION
General
1. Install dryer on a level base, indoors or under a
shed.
2. During shipment, flange and connecting bolts can
come loose. All bolts should be checked and
tightened as needed.
3. Make sure when the piping is in place that no undue
stress is placed on dryer connections. Union joints
or flexible connections are recommended to relieve
stress. Also, properly support the pipes as needed
with hangers or brackets. Air piping must be
installed by an experienced pipe fitter.
4. Equip dryer with inlet and outlet isolation valves and
a bypass valve for ease of servicing and start-up.
5. Connect electric power to the dryer through a
properly sized fused disconnect switch.
6. Reactivation exhaust may be piped away from the
dryer, making sure proper pipe size is used. The
pipe size should be increased by one size at the
valve, and one additional pipe diameter size for
every ten-foot run to reduce back pressure.
7.
ELECTRICAL CONNECTIONS:
Follow the
recognized local and municipal electrical codes. All
components must be load rated as approved by
NEC, NEMA, CSA and UL.
DANGER
High voltage could cause death or serious injury.
Disconnect all power supplies before installing or
working on electrical components.
8. During shipment, wire connections may become
loose. Per U.L. specification, torque screws inside
enclosure to 20 in-lbs.
9.
GROUNDING:
It is mandatory that the dryer be
grounded. Use an adequate ground with the
conductor sized to NEC.
10.
STORAGE:
In case of extended storage period
before the installation, follow these simple
procedures:
a. Seal or cover all the parts
b. Wrap the electrical enclosure
c. Wrap the mufflers
d. If the desiccant is shipped loose, store it inside
to avoid any rain or water damage.
11.
LEAK TEST:
All the dryers are tested at the factory
for any leaks before shipment. An air leak could
develop during transportation or installation.
Pressurize the system and check for any leaks.
Start-Up Procedure
1. Keeping the dryer isolation outlet valve closed,
slowly pressurize both the adsorbent chambers to
the line pressure.
2. Check for any leaks in the system.
3. When both adsorbent chambers are at line pressure,
push the ON button.
4. One inlet valve will close, and one purge valve will
open and depressurize one adsorbent chamber.
This may take as long as 3 minutes.
5. Adjust the purge pressure to the recommended
setting, and lock the valve locking mechanism in
place.
6. Slowly open the dryer isolation outlet valve to
pressurize the downstream system.
7. Observe the dryer operation through one or two
complete cycles.
Adjustments & Settings
1. Adjust the purge pressure to the recommended level
____________PSIG.
2. Dewpoint Demand Setpoint: ______________
High Humidity Alarm Setpoint: _____________
(See dewpoint display settings on Page 17)
DMP Microprocessor Control with Cycle
Sight ™
For standard PH & EH Series Air Dryers.
INTRODUCTION
1.
GENERAL:
The DMP controller is a microprocessor
controlled, seven (7) channel sequence timer with
LED display features. The DMP controller consists of
the main control unit and a remote LED and timer.
8