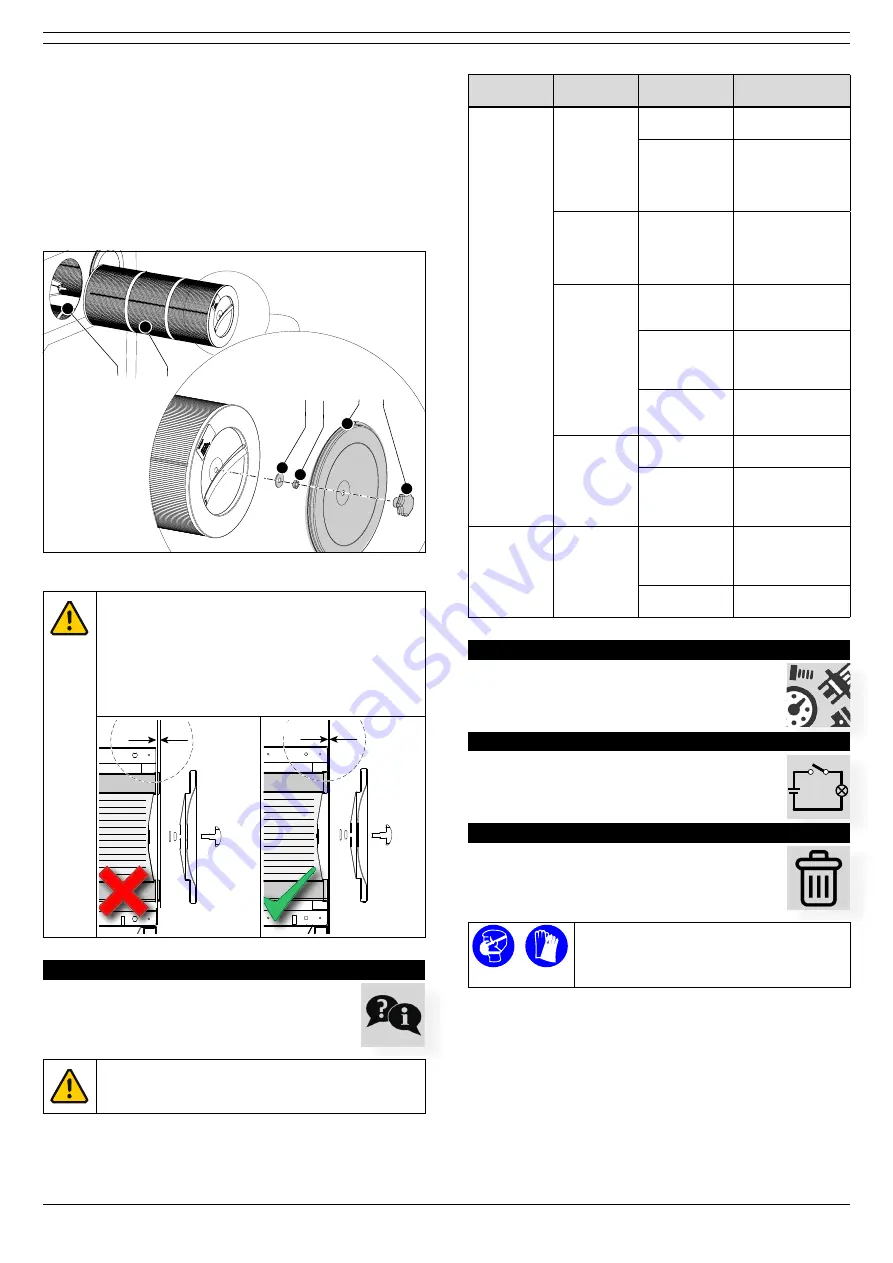
0000100513/050719/C MDB GO | MDB PRO
14
• Seal the sack securely.
• Put a new filter cartridge on the cartridge holder (A) and
attach it with the disassembled parts.
• Do the same procedure for the lower filter cartridges.
• Connect the compressed air.
• Energize the system.
• Dispose of the used filter cartridges in accordance with
federal, state or local regulations.
• Clean the environment of the system.
Fig. 6.2
A
B
D
C
E
F
Filter replacement
ATTENTION
Make sure that the front of the filter cartridge
aligns
*)
with the filter housing, so that the cover
plate closes well. If this is not the case, the filter
cartridge is not positioned correctly. This can cause
leakage and less efficient operation of the filter
cartridge.
*)
tolerance: max. 2 mm (0.1 in.)
>2 mm
max. 2 mm
>2 mm
max. 2 mm
>2 mm
max. 2 mm
>2 mm
max. 2 mm
7
TROUBLESHOOTING
If the system does not function (correctly), consult
the checklist below to see if you can remedy the
error yourself. Should this not be possible, contact
your supplier.
WARNING
Obey the safety regulations that are written in
chapter 3 when you carry out the activities below.
Symptom
Problem
Possible
cause
Solution
Poor
extraction
capacity
The system
does not
function
properly
Clogged filter
cartridges
Replace the filter
cartridges
Inverted
direction of
rotation of the
motor of the
connected fan
Change the
direction of rotation
Pollution of
the facility
Filter
cartridge(s)
ripped or
placed
incorrectly
Replace the filter
cartridges(s) or
place them
correctly (ref.
No filter
cleaning
Loose
compressed air
connection
Repair the
compressed air
connection
No compressed
air available or
air pressure too
low
Repair the
compressed air
supply
Membrane
valve(s)
defective
Replace the
membrane valve(s)
No pressure
in the
compressed
air tank
Drain valve is
loose
Tighten the drain
valve
Tank not
connected to
compressed air
supply
Repair the
compressed air
connection
Hissing sound No filter
cleaning
Membrane
valve(s)
defective or
worn
Replace the
membrane valve(s)
Wrong or
damaged wiring
Correct or repair
the wiring
8
SPARE PARTS
Refer to the exploded view Fig. VI on page 19.
9
ELECTRICAL DIAGRAM
Refer to the electrical diagram that is supplied with
the control equipment.
10
DISPOSAL
Dismantling and disposal of the
system
must be
done by qualified persons.
Personal protective equipment (PPE)
Wear respiratory protection and protective
gloves when you dismantle and dispose of
the
system
.
10.1
Dismantling
To safely dismantle the filter system, obey the safety
instructions that follow.
Before dismantling of the filter system:
- disconnect it from the mains
- disconnect it from the compressed air
- clean the outside