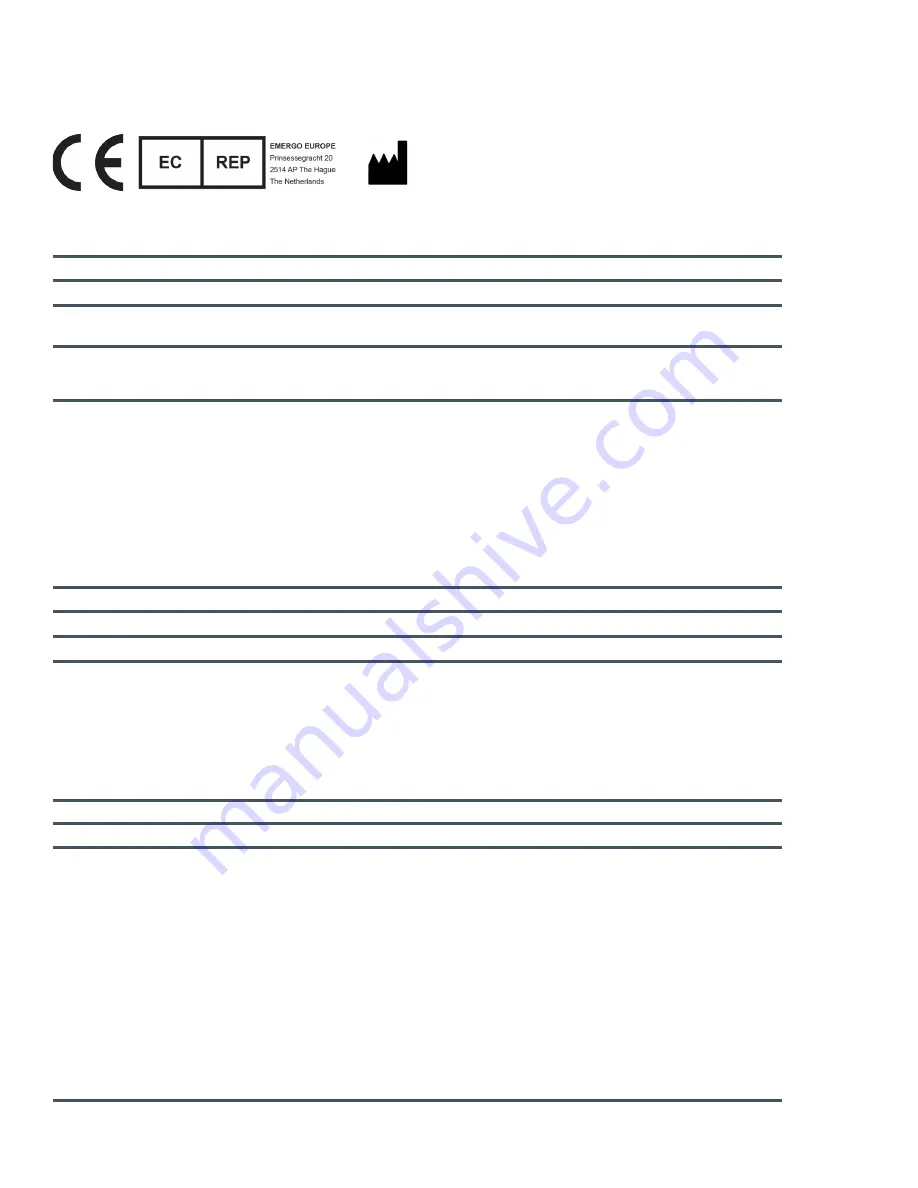
Planmeca PlanMill 40 S User Manual
Mill System Specifications
27
Mill System Specifications
D4D Technologies LLC
2920 Telecom Parkway Ste 100
Richardson, TX 75082 USA
The components use standard electrical current and do not need to be attached to a water supply or drain.
Model Number: Mill
PlanMill 40 S
Electrical Ratings:
100-240 Vac, 1000 W, 50-60 Hz
Air Requirements:
50 - 130 psi, minimum 2 cfm, filtered, dry air
Data Connection
Requirements:
Cat5 Ethernet cabling
Storage conditions
-4
o
F to 140
o
F (-20
o
C to 60
o
C)
5% to 95% RH “non-condensing”
Operating conditions for
Planmeca equipment
Indoor use only
41
o
F to 104
o
F (5
o
C to 40
o
C)
Transient overvoltage category II per IEC 60364
Maximum altitude 6,562 ft (2,000 m)
Maximum 80% non-condensing relative humidity for temperatures up to 88 °F
(31 °C)
Pollution degree 2
Dimensions:
17.5 in. (445 mm) tall x 26 in. (661 mm) wide x 20 in. (508 mm) deep
Minimum Clearance
Sides: 2 in.; Rear: 1 in.; Top: 12 in.
Weight:
170 lb. (77 kg)
Applicable Standards
Electrical and Mechanical
Safety
UL 61010-1:2015, 3rd Edition
CSA C22.2 No 61010-1:2012, 3rd Edition
IEC/EN 61010-1:2010, 3rd Edition
EMC
IEC/EN 61326
Packaging and Environmental
ISTA 3 Series
Additional Standards
ISO 14971:2007
EN ISO 14971:2012
EN ISO 13485:2012
ISO 13485: 2016
European Directive
•
2006/42/EC for Machinery
•
2004/108/EC for EMC
•
2002/96/EC for WEEE
•
2011/65/EU for RoHS