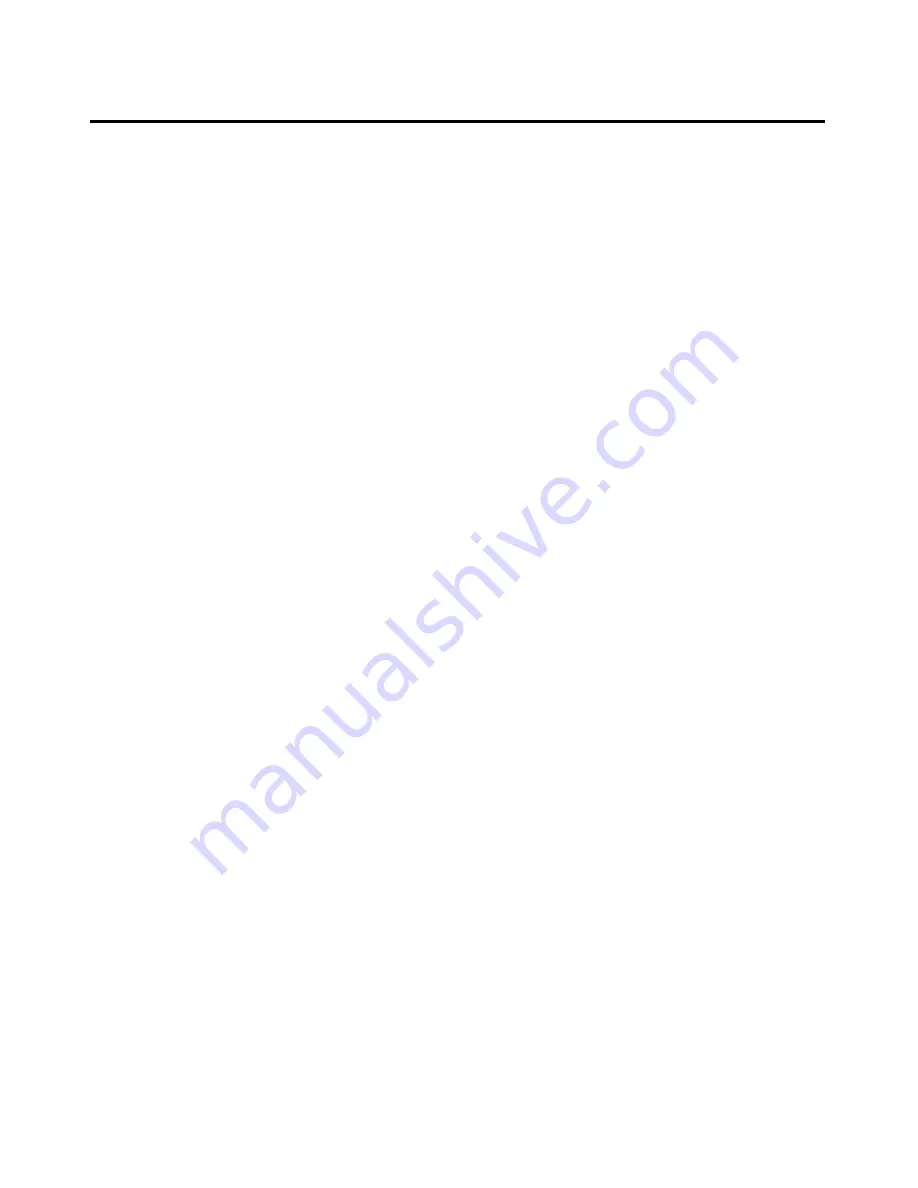
INSTALLATION OF HARNESS.
Before installing the harness plate on the magneto, check the mating surfaces for cleanliness. Spray the
entire face of the grommet with a light coat of Plastic Mold Spray, SM-O-O-TH Silicone Spray or equivalent.
This will prevent the harness grommet from sticking to the magneto distributor block.
1. Place the harness terminal plate on the magneto and tighten the nuts around the plate alternately to seat
the cover squarely on the magneto. Torque the nuts to 18 to 22 inch-pounds.
2. Route the ignition wires to their respective cylinders as shown in Figure 74-21.
3. Clamp the harness assembly in position.
4. Connect the leads to the spark plugs.
SPARK PLUGS.
REMOVAL OF SPARK PLUGS.
1. Loosen the coupling nut on the harness lead and remove the terminal insulator from the spark plug
barrel well. (A crows foot adapter is needed to remove the lower spark plugs.)
—NOTE—
When withdrawing the ignition cable lead connection from the
plug, care must be taken to pull the lead straight out and in line
with the center line of the plug barrel; otherwise, a side load will
be applied which frequently results in damage to the barrel
insulator and connector. If the lead cannot be removed easily in
this manner, the resisting contact between the neoprene collar
and the barrel insulator will be broken by a rotary twisting of the
c o l l a r. Avoid undue distortion of the collar and possible side
loading of the barrel insulator.
2. Remove the spark plug from the engine. In the course of engine operation, carbon and other
combustion products will be deposited on the end of the spark plug and will penetrate the lower threads to
some degree. As a result, greater torque is frequently required for removing a plug than for its installation.
Accordingly, the torque limitations given do not apply to plug removal, and sufficient torque must be used to
unscrew the plug. The higher torque in removal is not as detrimental as in installation, since it cannot stretch
the threaded section. lt does, however, impose a shearing load on this section and may, if sufficiently severe,
produce a failure in this location.
—NOTE—
Torque indicating handle should not be used for spark plug
removal because of the greater torque requirement.
3. Place spark plugs in a tray that will identify their position in the engine as soon as they are removed .
—NOTE—
Spark plugs should not be used if they have been dropped.
Effectivity
74-22-01
PA-28RT-201T
Page 74-19
December 1, 1978
3E4
PIPER AIRCRAFT
PA-28RT-201 / 201T
MAINTENANCE MANUAL
Summary of Contents for Arrow IV
Page 18: ...CHAPTER AIRWORTHINESS LIMITATIONS 1A18...
Page 21: ...THIS PAGE INTENTIONALLY LEFT BLANK 1A21 PIPER AIRCRAFT PA 28RT 201 201T MAINTENANCE MANUAL...
Page 22: ...CHAPTER TIME LIMITS MAINT CHECKS 1A22...
Page 39: ...THIS PAGE INTENTIONALLY LEFT BLANK 1B15 PIPER AIRCRAFT PA 28RT 201 201T MAINTENANCE MANUAL...
Page 40: ...CHAPTER DIMENSIONS AND AREAS 1B16...
Page 52: ...THIS PAGE INTENTIONALLY LEFT BLANK 1C4 PIPER AIRCRAFT PA 28RT 201 201T MAINTENANCE MANUAL...
Page 53: ...CHAPTER LIFTING AND SHORING 1C5...
Page 56: ...THIS PAGE INTENTIONALLY LEFT BLANK 1C8 PIPER AIRCRAFT PA 28RT 201 201T MAINTENANCE MANUAL...
Page 57: ...CHAPTER LEVELING AND WEIGHING 1C9...
Page 61: ...THIS PAGE INTENTIONALLY LEFT BLANK 1C13 PIPER AIRCRAFT PA 28RT 201 201T MAINTENANCE MANUAL...
Page 62: ...CHAPTER TOWING AND TAXIING 1C14...
Page 65: ...THIS PAGE INTENTIONALLY LEFT BLANK 1C17 PIPER AIRCRAFT PA 28RT 201 201T MAINTENANCE MANUAL...
Page 66: ...CHAPTER PARKING AND MOORING 1C18...
Page 69: ...THIS PAGE INTENTIONALLY LEFT BLANK 1C21 PIPER AIRCRAFT PA 28RT 201 201T MAINTENANCE MANUAL...
Page 70: ...CHAPTER REQUIRED PLACARDS 1C22...
Page 74: ...THIS PAGE INTENTIONALLY LEFT BLANK 1D2 PIPER AIRCRAFT PA 28RT 201 201T MAINTENANCE MANUAL...
Page 75: ...THIS PAGE INTENTIONALLY LEFT BLANK 1D3 PIPER AIRCRAFT PA 28RT 201 201T MAINTENANCE MANUAL...
Page 76: ...THIS PAGE INTENTIONALLY LEFT BLANK 1D4 PIPER AIRCRAFT PA 28RT 201 201T MAINTENANCE MANUAL...
Page 77: ...CHAPTER SERVICING 1D5...
Page 103: ...THIS PAGE INTENTIONALLY LEFT BLANK 1E7 PIPER AIRCRAFT PA 28RT 201 201T MAINTENANCE MANUAL...
Page 109: ...THIS PAGE INTENTIONALLY LEFT BLANK 1E13 PIPER AIRCRAFT PA 28RT 201 201T MAINTENANCE MANUAL...
Page 110: ...CHAPTER STANDARD PRACTICES AIRFRAME 1E14...
Page 116: ...THIS PAGE INTENTIONALLY LEFT BLANK 1E20 PIPER AIRCRAFT PA 28RT 201 201T MAINTENANCE MANUAL...
Page 117: ...CHAPTER ENVIRONMENTAL SYSTEM 1E21...
Page 167: ...THIS PAGE INTENTIONALLY LEFT BLANK 1G23 PIPER AIRCRAFT PA 28RT 201 201T MAINTENANCE MANUAL...
Page 168: ...THIS PAGE INTENTIONALLY LEFT BLANK 1G24 PIPER AIRCRAFT PA 28RT 201 201T MAINTENANCE MANUAL...
Page 169: ...CHAPTER AUTO FLIGHT 1H1...
Page 173: ...THIS PAGE INTENTIONALLY LEFT BLANK 1H5 PIPER AIRCRAFT PA 28RT 201 201T MAINTENANCE MANUAL...
Page 174: ...THIS PAGE INTENTIONALLY LEFT BLANK 1H6 PIPER AIRCRAFT PA 28RT 201 201T MAINTENANCE MANUAL...
Page 175: ...THIS PAGE INTENTIONALLY LEFT BLANK 1H7 PIPER AIRCRAFT PA 28RT 201 201T MAINTENANCE MANUAL...
Page 176: ...CHAPTER COMMUNICATIONS 1H8...
Page 185: ...CHAPTER ELECTRICAL POWER 1H17...
Page 229: ...THIS PAGE INTENTIONALLY LEFT BLANK 1J13 PIPER AIRCRAFT PA 28RT 201 201T MAINTENANCE MANUAL...
Page 230: ...THIS PAGE INTENTIONALLY LEFT BLANK 1J14 PIPER AIRCRAFT PA 28RT 201 201T MAINTENANCE MANUAL...
Page 231: ...THIS PAGE INTENTIONALLY LEFT BLANK 1J15 PIPER AIRCRAFT PA 28RT 201 201T MAINTENANCE MANUAL...
Page 232: ...THIS PAGE INTENTIONALLY LEFT BLANK 1J16 PIPER AIRCRAFT PA 28RT 201 201T MAINTENANCE MANUAL...
Page 233: ...CHAPTER FLIGHT CONTROLS 1J17...
Page 297: ...CHAPTER FUEL 2A18...
Page 320: ...CHAPTER HYDRAULIC POWER 2B17...
Page 355: ...CHAPTER LANDING GEAR 2D4...
Page 418: ...CHAPTER LIGHTS 2F19...
Page 430: ...CHAPTER NAVIGATION AND PITOT STATIC 2G7...
Page 444: ...CHAPTER OXYGEN SYSTEM 2G21...
Page 464: ...CHAPTER VACUUM SYSTEM 2H17...
Page 473: ...CHAPTER ELECTRICAL ELECTRONIC PANELS AND MULTI PURPOSE PARTS 2I2...
Page 476: ...THIS PAGE INTENTIONALLY LEFT BLANK 2I5 PIPER AIRCRAFT PA 28RT 201 201T MAINTENANCE MANUAL...
Page 477: ...CHAPTER STRUCTURES 2I6...
Page 495: ...THIS PAGE INTENTIONALLY LEFT BLANK 2I24 PIPER AIRCRAFT PA 28RT 201 201T MAINTENANCE MANUAL...
Page 496: ...CHAPTER DOORS 2J1...
Page 504: ...THIS PAGE INTENTIONALLY LEFT BLANK 2J9 PIPER AIRCRAFT PA 28RT 201 201T MAINTENANCE MANUAL...
Page 505: ...CHAPTER STABILIZERS 2J10...
Page 514: ...CHAPTER WINDOWS 2J19...
Page 519: ...CHAPTER WINGS 2J24...
Page 550: ...CHAPTER PROPELLER 3A18...
Page 565: ...CHAPTER STANDARD PRACTICES ENGINE 3B9...
Page 568: ...CHAPTER POWER PLANT 3B12...
Page 592: ...CHAPTER ENGINE FUEL AND CONTROL 3C12...
Page 610: ...THIS PAGE INTENTIONALLY LEFT BLANK 3D6 PIPER AIRCRAFT PA 28RT 201 201T MAINTENANCE MANUAL...
Page 611: ...CHAPTER IGNITION 3D7...
Page 654: ...3F2 THRU 3F15 INTENTIONALLY LEFT BLANK 3F2 PIPER AIRCRAFT PA 28RT 201 201T MAINTENANCE MANUAL...
Page 655: ...CHAPTER ENGINE INDICATING 3F16...
Page 662: ...THIS PAGE INTENTIONALLY LEFT BLANK 3F23 PIPER AIRCRAFT PA 28RT 201 201T MAINTENANCE MANUAL...
Page 663: ...THIS PAGE INTENTIONALLY LEFT BLANK 3F24 PIPER AIRCRAFT PA 28RT 201 201T MAINTENANCE MANUAL...
Page 664: ...CHAPTER EXHAUST 3G1...
Page 668: ...THIS PAGE INTENTIONALLY LEFT BLANK 3G5 PIPER AIRCRAFT PA 28RT 201 201T MAINTENANCE MANUAL...
Page 669: ...CHAPTER OIL SYSTEM 3G6...
Page 672: ...THIS PAGE INTENTIONALLY LEFT BLANK 3G9 PIPER AIRCRAFT PA 28RT 201 201T MAINTENANCE MANUAL...
Page 673: ...CHAPTER STARTING 3G10...
Page 685: ...THIS PAGE INTENTIONALLY LEFT BLANK 3G22 PIPER AIRCRAFT PA 28RT 201 201T MAINTENANCE MANUAL...
Page 686: ...THIS PAGE INTENTIONALLY LEFT BLANK 3G23 PIPER AIRCRAFT PA 28RT 201 201T MAINTENANCE MANUAL...
Page 687: ...THIS PAGE INTENTIONALLY LEFT BLANK 3G24 PIPER AIRCRAFT PA 28RT 201 201T MAINTENANCE MANUAL...
Page 688: ...CHAPTER TURBINES 3H1...
Page 693: ...THIS PAGE INTENTIONALLY LEFT BLANK 3H6 PIPER AIRCRAFT PA 28RT 201 201T MAINTENANCE MANUAL...
Page 694: ...CHAPTER 91 CHARTS AND WIRING DIAGRAMS 3H7...
Page 704: ...THIS PAGE INTENTIONALLY LEFT BLANK 3H17 PIPER AIRCRAFT PA 28RT 201 201T MAINTENANCE MANUAL...
Page 738: ...3J3 THRU 3J24 INTENTIONALLY LEFT BLANK 3J3 PIPER AIRCRAFT PA 28RT 201 201T MAINTENANCE MANUAL...