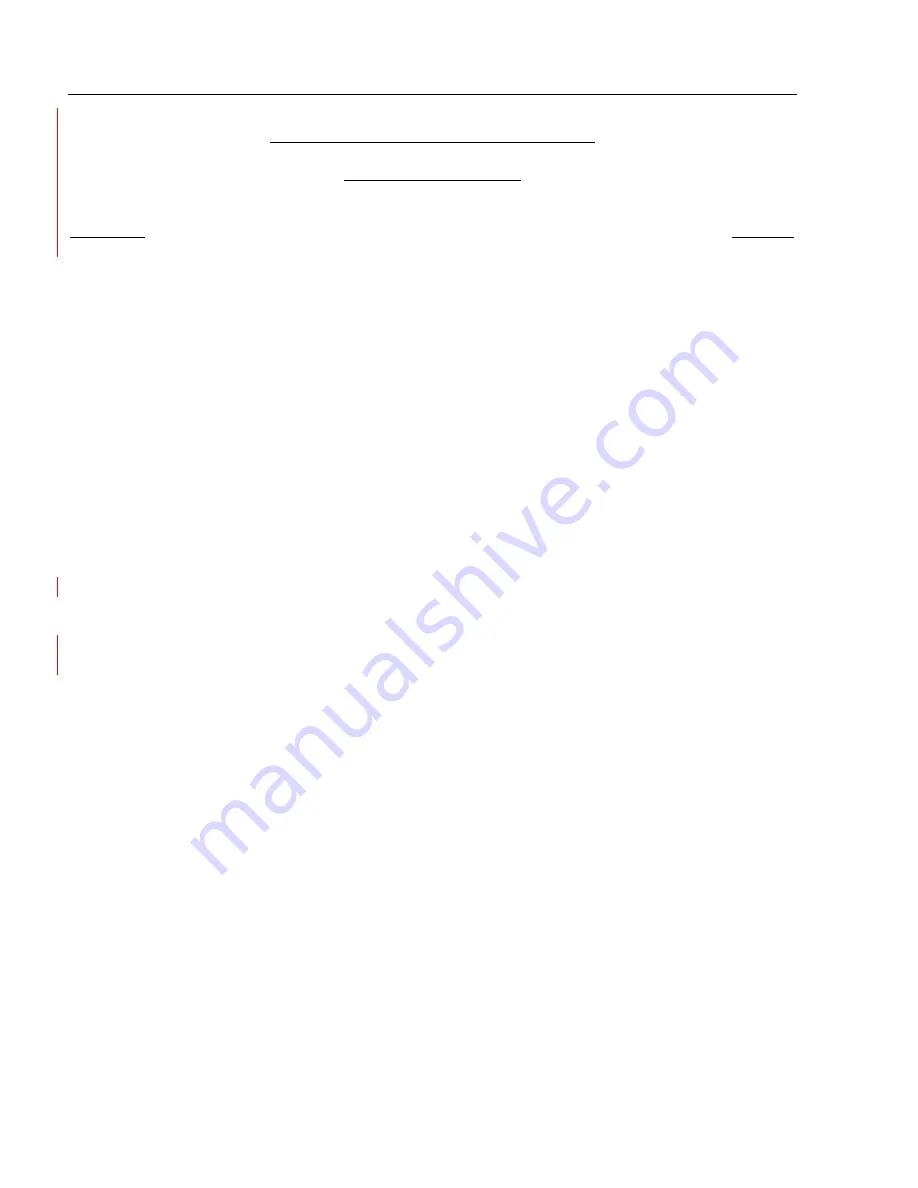
PIPER CHEROKEE SERVICE MANUAL
VIIIA - TABLE OF CONTENTS
01/31/08
3A8
SECTION VIIIA - POWER PLANT (PA-28R)
TABLE OF CONTENTS
Paragraph
Grid No.
8A-1.
Introduction . . . . . . . . . . . . . . . . . . . . . . . . . . . . . . . . . . . . . . . . . . . . .
3A10
8A-2.
Description . . . . . . . . . . . . . . . . . . . . . . . . . . . . . . . . . . . . . . . . . . . . . .
3A10
8A-3.
Troubleshooting . . . . . . . . . . . . . . . . . . . . . . . . . . . . . . . . . . . . . . . . . .
3A10
8A-4.
Propeller . . . . . . . . . . . . . . . . . . . . . . . . . . . . . . . . . . . . . . . . . . . . . . . .
3A11
8A-5.
Removal of Propeller . . . . . . . . . . . . . . . . . . . . . . . . . . . . . . . . . . .
3A11
8A-6.
Cleaning, Inspection and Repair of Propeller . . . . . . . . . . . . . . . .
3A11
8A-7.
Installing Propeller . . . . . . . . . . . . . . . . . . . . . . . . . . . . . . . . . . . .
3A13
8A-8.
Blade Track . . . . . . . . . . . . . . . . . . . . . . . . . . . . . . . . . . . . . . . . . .
3A14
8A-9.
Propeller Governor . . . . . . . . . . . . . . . . . . . . . . . . . . . . . . . . . . . .
3A14
8A-10.
Removal of Propeller Governor . . . . . . . . . . . . . . . . . . . . . . . . . . .
3A14
8A-11.
Installation of Propeller Governor . . . . . . . . . . . . . . . . . . . . . . . . .
3A14
8A-12.
Rigging and Adjustment of Propeller Governor . . . . . . . . . . . . . .
3A15
8A-13.
Engine . . . . . . . . . . . . . . . . . . . . . . . . . . . . . . . . . . . . . . . . . . . . . . . . .
3A16
8A-14.
Removal of Engine . . . . . . . . . . . . . . . . . . . . . . . . . . . . . . . . . . . .
3A16
8A-15.
Installation of Engine . . . . . . . . . . . . . . . . . . . . . . . . . . . . . . . . . . .
3A17
8A-16.
Installation of Oil Cooler . . . . . . . . . . . . . . . . . . . . . . . . . . . . . . . . . . .
3A24
8A-17.
Adjustment of Throttle and Mixture Controls . . . . . . . . . . . . . . . . . . .
3A24
8A-18.
Induction Air Filter . . . . . . . . . . . . . . . . . . . . . . . . . . . . . . . . . . . . . . . .
3B2
8A-19.
Alternate Air Door . . . . . . . . . . . . . . . . . . . . . . . . . . . . . . . . . . . . . . . .
3B2
8A-19a.
50 Hour Inspection . . . . . . . . . . . . . . . . . . . . . . . . . . . . . . . . . . . .
3B2
8A-19b.
100 Hour Inspection . . . . . . . . . . . . . . . . . . . . . . . . . . . . . . . . . . .
3B2
8A-20.
Fuel Injector . . . . . . . . . . . . . . . . . . . . . . . . . . . . . . . . . . . . . . . . . . . . .
3B3
8A-21.
Fuel Injector Maintenance . . . . . . . . . . . . . . . . . . . . . . . . . . . . . . .
3B3
8A-22.
Adjustment of Idle Speed and Mixture . . . . . . . . . . . . . . . . . . . . .
3B5
8A-23.
Fuel Air Bleed Nozzle . . . . . . . . . . . . . . . . . . . . . . . . . . . . . . . . . .
3B6
8A-24.
Removal of Fuel-Air Bleed Nozzle . . . . . . . . . . . . . . . . . . . . . . . .
3B6
8A-25.
Cleaning and Inspection of Fuel-Air Bleed Nozzle . . . . . . . . . . . .
3B6
8A-26.
Installation of Fuel-Air Bleed Nozzle . . . . . . . . . . . . . . . . . . . . . .
3B6
8A-27.
Ignition System Maintenance . . . . . . . . . . . . . . . . . . . . . . . . . . . . . . . .
3B7
8A-28.
Magneto . . . . . . . . . . . . . . . . . . . . . . . . . . . . . . . . . . . . . . . . . . . . . . . .
3B7
8A-29.
Inspection of Magneto . . . . . . . . . . . . . . . . . . . . . . . . . . . . . . . . . .
3B7
8A-30.
Removal of Magneto . . . . . . . . . . . . . . . . . . . . . . . . . . . . . . . . . . .
3B9
8A-31.
Timing Procedure (Internal Timing) . . . . . . . . . . . . . . . . . . . . . . .
3B9
8A-32.
Installation and Timing Procedure (Timing Magneto to Engine) .
3B12
Summary of Contents for Cherokee 140 PA-28-140
Page 4: ...INTRODUCTION 01 31 08 1A4 PIPER CHEROKEE SERVICE MANUAL THIS PAGE INTENTIONALLY BLANK...
Page 19: ...PIPER CHEROKEE SERVICE MANUAL 1A19 SECTION I AIRWORTHINESS LIMITATIONS...
Page 20: ...PIPER CHEROKEE SERVICE MANUAL 1A20 THIS PAGE INTENTIONALLY BLANK...
Page 30: ...PIPER CHEROKEE SERVICE MANUAL 1694 Reissued 1 15 81 HANDLINGANDSERVICING 1B6...
Page 50: ......
Page 57: ......
Page 61: ......
Page 127: ...PIPER CHEROKEE SERVICE MANUAL 1F7 SECTION III INSPECTION MOVED TO GRID 3H1...
Page 128: ...PIPER CHEROKEE SERVICE MANUAL 1F8 GRIDS 1F8 THRU 1G12 INTENTIONALLY BLANK...
Page 138: ...PIPER CHEROKEE SERVICE MANUAL IV STRUCTURES 01 31 08 1G22 THIS PAGE INTENTIONALLY BLANK...
Page 139: ......
Page 150: ...PIPER CHEROKEE SERVICE MANUAL IV STRUCTURES 01 31 08 1H10 THIS PAGE INTENTIONALLY BLANK...
Page 152: ......
Page 197: ...PIPER CHEROKEE SERVICE MANUAL 1K1 INTRODUCTION...
Page 198: ...PIPER CHEROKEE SERVICE MANUAL 1K2 THIS PAGE INTENTIONALLY BLANK...
Page 240: ...PIPER CHEROKEE SERVICE MANUAL V SURFACE CONTROLS 01 31 08 2B6 Figure 5 6 Stabilator Controls...
Page 261: ...PIPER CHEROKEE SERVICE MANUAL 01 31 08 V SURFACE CONTROLS 2C3 Figure 5 12 Rudder Controls...
Page 267: ...PIPER CHEROKEE SERVICE MANUAL 01 31 08 V SURFACE CONTROLS 2C9 Figure 5 16 Rudder Trim Control...
Page 270: ...PIPER CHEROKEE SERVICE MANUAL V SURFACE CONTROLS 01 31 08 2C12 Figure 5 17 Flap Controls...
Page 275: ...PIPER CHEROKEE SERVICE MANUAL 01 31 08 V SURFACE CONTROLS 2C17 THIS PAGE INTENTIONALLY BLANK...
Page 276: ...PIPER CHEROKEE SERVICE MANUAL V SURFACE CONTROLS 01 31 08 2C18 THIS PAGE INTENTIONALLY BLANK...
Page 326: ...PIPER CHEROKEE SERVICE MANUAL VI HYDRAULIC SYSTEM 01 31 08 2E20 THIS PAGE INTENTIONALLY BLANK...
Page 327: ...PIPER CHEROKEE SERVICE MANUAL 01 31 08 VI HYDRAULIC SYSTEM 2E21 THIS PAGE INTENTIONALLY BLANK...
Page 347: ...INTENTIONALLY LEFTBLANK 2F17...
Page 419: ...u i I N 3 a G O u o O 6 o...
Page 431: ......
Page 447: ...pue6L80 Bu uo dn s S3 0 LL 6 L 9...
Page 448: ...OO pue 06 u 6u S S 6 8 LL 9 91 S L...
Page 450: ...9 9 9L 0 s 18 00 a 06 06 06 S9 6 SOS 6 99 uo S Z SZ 00 00 00 68 Z S Z LL 6 8 L 9 N 6 d S33MOi...
Page 497: ......
Page 498: ......
Page 516: ...3A18 INTENTIONALLY LEFT BLANK...
Page 553: ...3C7 INTENTIONALLYLEFTBLANK...
Page 561: ...3C15 INTENTIONALLYLEFTBLANK...
Page 562: ...3C16 INTENTIONALLY LEFT BLANK...
Page 584: ...3D14 INTENTIONALLYLEFTBLANK...
Page 588: ...PIPER CHEROKEE SERVICE MANUAL IX FUEL SYSTEM 01 31 08 3D18 THIS PAGE INTENTIONALLY BLANK...
Page 599: ......
Page 600: ......
Page 604: ...i...
Page 605: ......
Page 608: ...ZZ __...
Page 609: ......
Page 612: ......
Page 613: ...0...
Page 614: ...3E20 INTENTIONALLYLEFTBLANK...
Page 648: ...PIPER CHEROKEE SERVICE MANUAL 3H1 SECTION III INSPECTION...
Page 649: ...PIPER CHEROKEE SERVICE MANUAL 3H2 THIS PAGE INTENTIONALLY BLANK...
Page 653: ...PIPER CHEROKEE SERVICE MANUAL III INSPECTION 01 31 08 3H6 THIS PAGE INTENTIONALLY BLANK...
Page 655: ...PIPER CHEROKEE SERVICE MANUAL III INSPECTION 01 31 08 3H8 THIS PAGE INTENTIONALLY BLANK...
Page 661: ...PIPER CHEROKEE SERVICE MANUAL III INSPECTION 01 31 08 3H14 THIS PAGE INTENTIONALLY BLANK...
Page 674: ...PIPER CHEROKEE SERVICE MANUAL 01 31 08 III INSPECTION 3I3 THIS PAGE INTENTIONALLY BLANK...
Page 675: ...PIPER CHEROKEE SERVICE MANUAL III INSPECTION 01 31 08 3I4 THIS PAGE INTENTIONALLY BLANK...
Page 687: ...PIPER CHEROKEE SERVICE MANUAL III INSPECTION 01 31 08 3I16 THIS PAGE INTENTIONALLY BLANK...
Page 717: ...PIPER CHEROKEE SERVICE MANUAL III INSPECTION 01 31 08 3J22 Figure 3 11 Drain Hole Installation...
Page 740: ...PIPER CHEROKEE SERVICE MANUAL 01 31 08 III INSPECTION 3K21 THIS PAGE INTENTIONALLY BLANK...
Page 741: ...PIPER CHEROKEE SERVICE MANUAL III INSPECTION 01 31 08 3K22 THIS PAGE INTENTIONALLY BLANK...
Page 742: ...PIPER CHEROKEE SERVICE MANUAL 01 31 08 III INSPECTION 3K23 THIS PAGE INTENTIONALLY BLANK...
Page 743: ...PIPER CHEROKEE SERVICE MANUAL III INSPECTION 01 31 08 3K24 THIS PAGE INTENTIONALLY BLANK...
Page 752: ...PIPER CHEROKEE SERVICE MANUAL 01 31 08 III INSPECTION 3L9 THIS PAGE INTENTIONALLY BLANK...
Page 753: ...PIPER CHEROKEE SERVICE MANUAL III INSPECTION 01 31 08 3L10 THIS PAGE INTENTIONALLY BLANK...
Page 767: ...PIPER CHEROKEE SERVICE MANUAL III INSPECTION 01 31 08 3L24 THIS PAGE INTENTIONALLY BLANK...
Page 839: ...THIS PAGE INTENTIONALLYLEFT BLANK 4C24...
Page 898: ......
Page 899: ......
Page 900: ......
Page 901: ......
Page 902: ......
Page 903: ......
Page 904: ......
Page 905: ......
Page 906: ......
Page 907: ......
Page 908: ......
Page 909: ......
Page 910: ......
Page 911: ......
Page 912: ......
Page 913: ......
Page 914: ......
Page 915: ......
Page 916: ......
Page 917: ......
Page 918: ......
Page 919: ......
Page 920: ......
Page 921: ......
Page 922: ......
Page 923: ......
Page 924: ......
Page 925: ......
Page 926: ......
Page 927: ......
Page 928: ......
Page 929: ......
Page 930: ......
Page 931: ......
Page 932: ......
Page 933: ......
Page 934: ......
Page 935: ......
Page 936: ......
Page 937: ......
Page 938: ......
Page 939: ......
Page 940: ......
Page 941: ......
Page 942: ......
Page 943: ......
Page 944: ......
Page 971: ...S I...
Page 975: ...0 b 4...
Page 976: ......
Page 996: ...4K4 INTENTIONALLYLEFTBLANK...