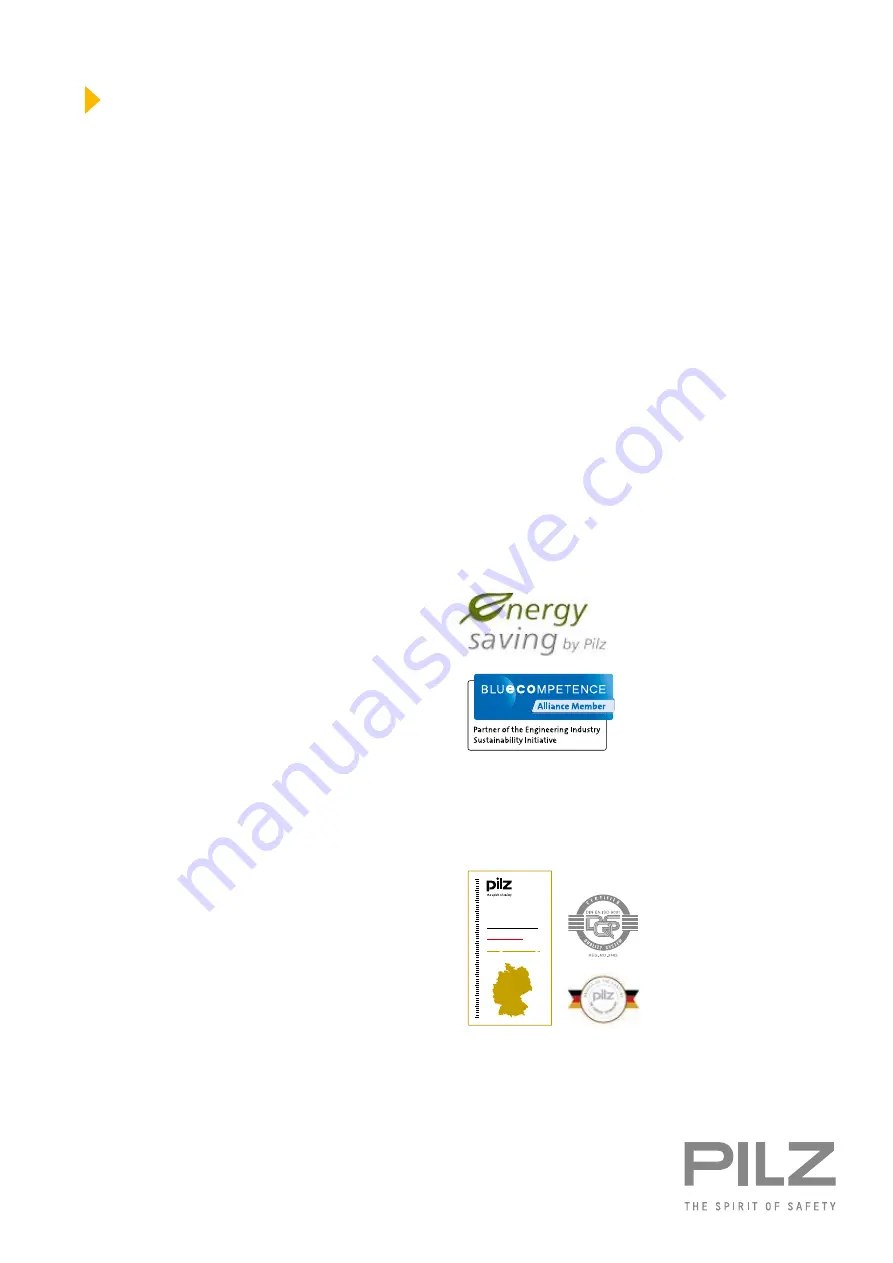
The Best of
German
Engineering
Partner of:
Support
Technical support is available from Pilz round the clock.
Americas
Brazil
+55 11 97569-2804
Canada
+1 888-315-PILZ (315-7459)
Mexico
+52 55 5572 1300
USA (toll-free)
+1 877-PILZUSA (745-9872)
Asia
China
+86 21 60880878-216
Japan
+81 45 471-2281
South Korea
+82 31 450 0680
Australia
+61 3 95600621
Europe
Austria
+43 1 7986263-0
Belgium, Luxembourg
+32 9 3217575
France
+33 3 88104000
Germany
+49 711 3409-444
Ireland
+353 21 4804983
Italy, Malta
+39 0362 1826711
Scandinavia
+45 74436332
Spain
+34 938497433
Switzerland
+41 62 88979-30
The Netherlands
+31 347 320477
Turkey
+90 216 5775552
United Kingdom
+44 1536 462203
You can reach our
international hotline on:
+49 711 3409-444
CMSE
®
, Indur
aNET p
®
, P
AS4000
®
, P
AScal
®
, P
ASconfig
®
, P
ilz
®
, PIT
®
, PLID
®
, PMCprimo
®
, PMCpr
ot
ego
®
, PMCt
endo
®
, PMD
®
, PMI
®
, PNO
Z
®
, P
rimo
®
, PSEN
®
, PSS
®
, PVIS
®
, SafetyBUS p
®
,
SafetyEYE
®
, SafetyNET p
®
, THE SPIRIT OF SAFET
Y
®
ar
e r
egist
er
ed and pr
ot
ect
ed tr
ademarks of P
ilz GmbH & Co. K
G in some countries. W
e would point out that pr
oduct featur
es may var
y
fr
om the details stat
ed in this document, depending on the status at the time of publication and the scope of the equipment. W
e accept no r
esponsibility for the validity, accur
acy
and entir
ety of the t
e
xt and gr
aphics pr
esent
ed in this information. Please contact our T
echnical Suppor
t if you have any questions.
Pilz develops environmentally-friendly products using
ecological materials and energy-saving technologies.
Offices and production facilities are ecologically designed,
environmentally-aware and energy-saving. So Pilz offers
sustainability, plus the security of using energy-efficient
products and environmentally-friendly solutions.
Pilz GmbH & Co. KG
Felix-Wankel-Straße 2
73760 Ostfildern, Germany
Tel.: +49 711 3409-0
Fax: +49 711 3409-133
www.pilz.com
200XXXX-EN-0X
0-0-2-3-000, 2017-00 P
rint
ed in Germany
© P
ilz GmbH & Co. K
G, 2017
1001454-EN-09, 2017-08 Printed in Germany © Pilz GmbH & Co. KG, 2015
Front cover