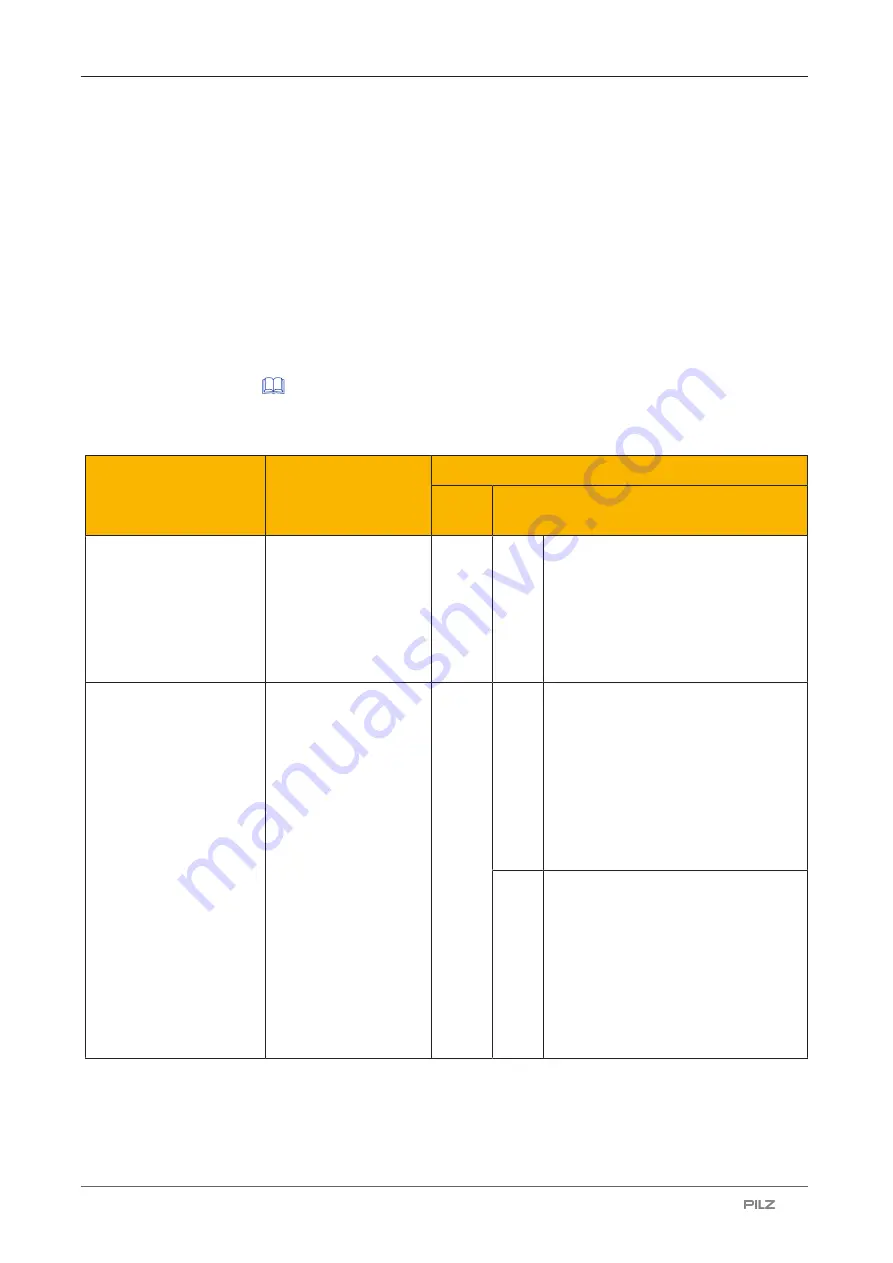
Wiring
System Description Service Robotics Modules
1004870-EN-05
| 86
8
Wiring
8.1
Connections for external devices
An industrial robot that is constructed using service robotics modules from Pilz can be ex-
panded using external devices such as emergency stop pushbuttons, reset buttons, safety
gates etc., depending on the application. The behaviour during a restart can also be con-
figured via the wiring, for example.
The system or plant integrator is tasked with determining the suitable equipment and suit-
able protective measures for the industrial robot depending on the application. Please note
the requirements of any application-dependent circuit diagram (see
diagram [
).
The following FS inputs for connection, prompting, reset and configuration of external
safety devices are pre-prepared:
Device
Implementation
(safety control sys-
tem)
Operating manual for robot control module PRCM1
Mod-
ule
Terminal configuration
Reset emergency stop
external
PSSu E F 4DI:
}
Digital FS input
}
Single-channel
}
No test pulse
A1.1
21
}
Label in circuit diagram:
Reset emergency stop external OK
}
Terminal 21: Input I1
}
Terminal 22: +24 V periphery supply
}
Delivery condition: No external wir-
ing
Emergency stop external
PSSu E F 4DI:
}
Digital FS input
}
Dual-channel
}
Test pulse via safety
control system
A1.2
11
}
Label in circuit diagram for channel
1:
Emergency stop external channel 1
OK
}
Terminal 11: Input I0
}
Terminal 12: Test pulse output T0
}
Delivery condition: Jumper terminals
11-12
14
}
Label in circuit diagram for channel
2:
Emergency stop external channel 2
OK
}
Terminal 14: Input I2
}
Terminal 13: Test pulse output T1
}
Delivery condition: Jumper terminals
13-14