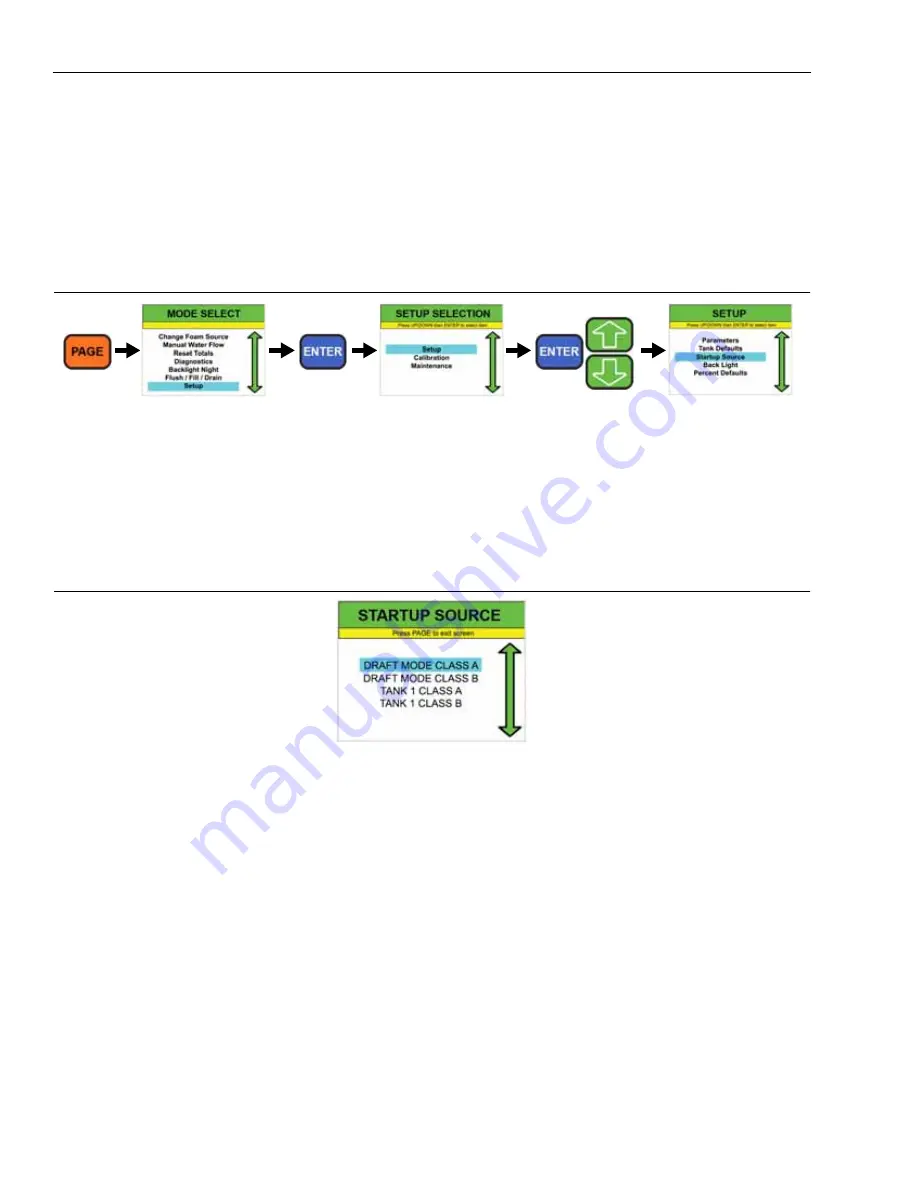
MAINTENANCE
4-10
/ Husky 12 Foam System
© 2017 Pierce Manufacturing Inc. All Rights Reserved.
4-6.3
Set Startup or Default Foam Source
MODE SELECT
→
SETUP SELECTION
→
SETUP
→
STARTUP SOURCE
NOTE:
The default foam source setting is used to determine which tank will open as the default tank, Class
A or Class B. On a single tank system it will change the default setting (Class A or Class B). If
changing a single tank system from A to B default, the foam valve remains plugged into the Class
A harness. If changing the types of foam in the tank, It is imperative to thoroughly flush out and dry
the entire system.
Figure
4-13:
Setup
Screen
Activation
1557E, 1568A, 1569B
1.
From the normal operation screen (Foam Pump Not Running), navigate to the SETUP screen. Refer to
2.
Use the UP/DOWN buttons to highlight Startup Source and press ENTER to bring up the STARTUP SOURCE
screen.
Figure
4-14:
Startup Source Screen
1572
3.
Using the UP/DOWN buttons, highlight the desired startup source.
4.
Press the ENTER button. You will be automatically transfered back to the home screen with that source being
selected.
HOLD ENTER AND
PRESS ARROWS
PRESS
PAGE
HOLD 5
SECONDS
SCROLL TO
SETUP
SCROLL TO
SETUP
Summary of Contents for HUSKY 12 GPM
Page 2: ......
Page 6: ...TABLE OF CONTENTS iv Husky 12 Foam System 2017 Pierce Manufacturing Inc All Rights Reserved ...
Page 8: ...FOREWORD vi Husky 12 Foam System 2017 Pierce Manufacturing Inc All Rights Reserved ...
Page 34: ...OPERATION 3 12 Husky 12 Foam System 2017 Pierce Manufacturing Inc All Rights Reserved ...