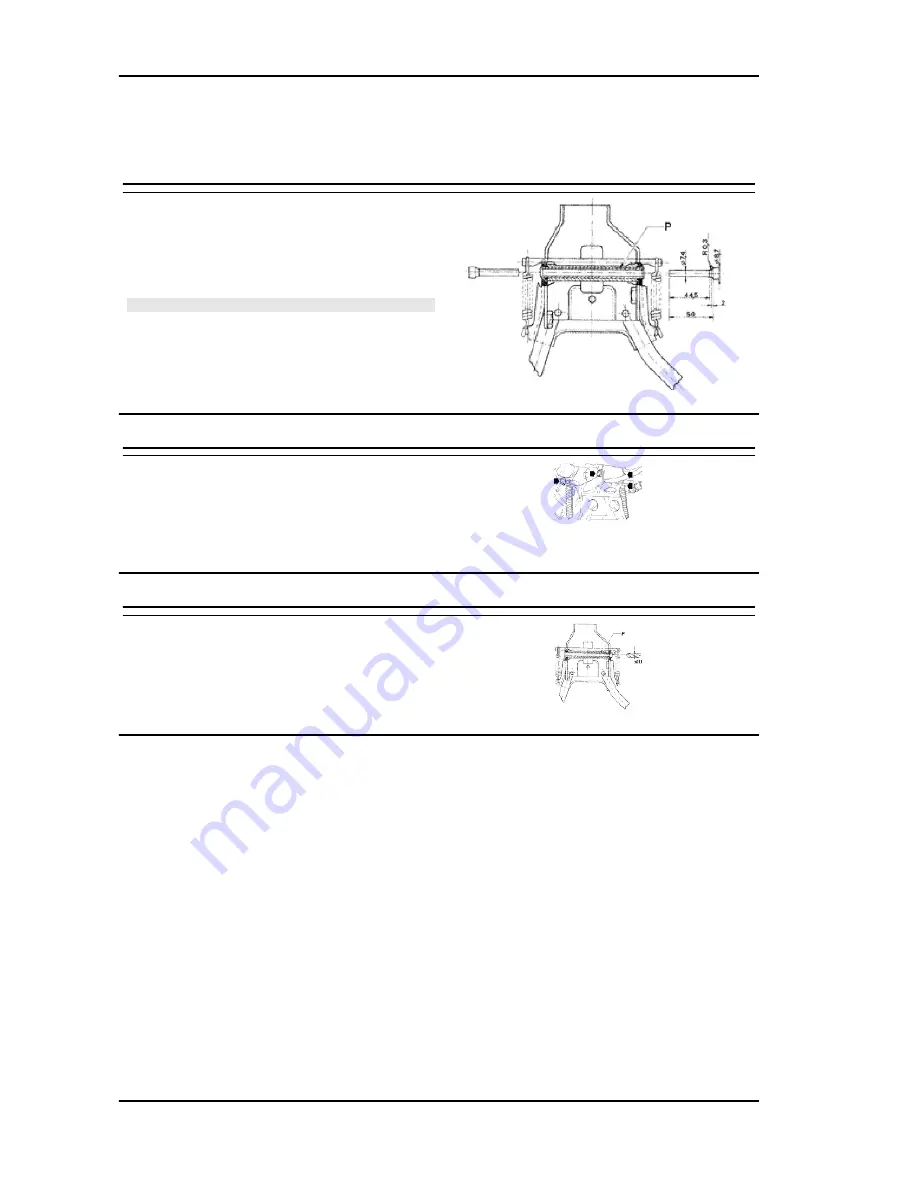
Centre-stand
Assembly and staking of stand pivot pin to bracket
- Caulk the end of the pin «P» between the two
punches shown in the figure.
- After caulking it must be possible for the stand to
turn freely.
N.B.
UPON REFITTING USE NEW O-RING AND PIN, GREASE
THE SPRING ATTACHMENTS AND THE PIN.
Changing the complete stand
- Work on the screws shown in the figure.
- When refitting, secure to the prescribed torque.
Locking torques (N*m)
Stand screw torque
18.5 to 19 Nm
Expelling stand pivot pin from bracket
- Remove the stand support bracket from the en-
gine.
- Drill a 5 mm hole in the bracket so that the pin
«P» can come out.
Suspensions
Liberty 50 4tempi
SUSP - 132
Summary of Contents for Liberty 50 4tempi 2008
Page 1: ...WORKSHOP MANUAL 633104 Liberty 50 4tempi ...
Page 4: ......
Page 6: ...INDEX OF TOPICS CHARACTERISTICS CHAR ...
Page 16: ...INDEX OF TOPICS TOOLING TOOL ...
Page 24: ...Stores code Description 494929Y Exhaust fumes analyser Tooling Liberty 50 4tempi TOOL 24 ...
Page 25: ...INDEX OF TOPICS MAINTENANCE MAIN ...
Page 37: ...INDEX OF TOPICS TROUBLESHOOTING TROUBL ...
Page 43: ...INDEX OF TOPICS ELECTRICAL SYSTEM ELE SYS ...
Page 61: ...INDEX OF TOPICS ENGINE FROM VEHICLE ENG VE ...
Page 64: ...INDEX OF TOPICS ENGINE ENG ...
Page 94: ...Engine Liberty 50 4tempi ENG 94 ...
Page 127: ...INDEX OF TOPICS SUSPENSIONS SUSP ...
Page 133: ...INDEX OF TOPICS BRAKING SYSTEM BRAK SYS ...
Page 141: ...INDEX OF TOPICS CHASSIS CHAS ...
Page 154: ...INDEX OF TOPICS PRE DELIVERY PRE DE ...
Page 158: ...INDEX OF TOPICS TIME TIME ...
Page 195: ...T Tank 152 177 Transmission 9 40 65 75 168 Turn indicators Tyres 10 V Vehicle 8 62 ...