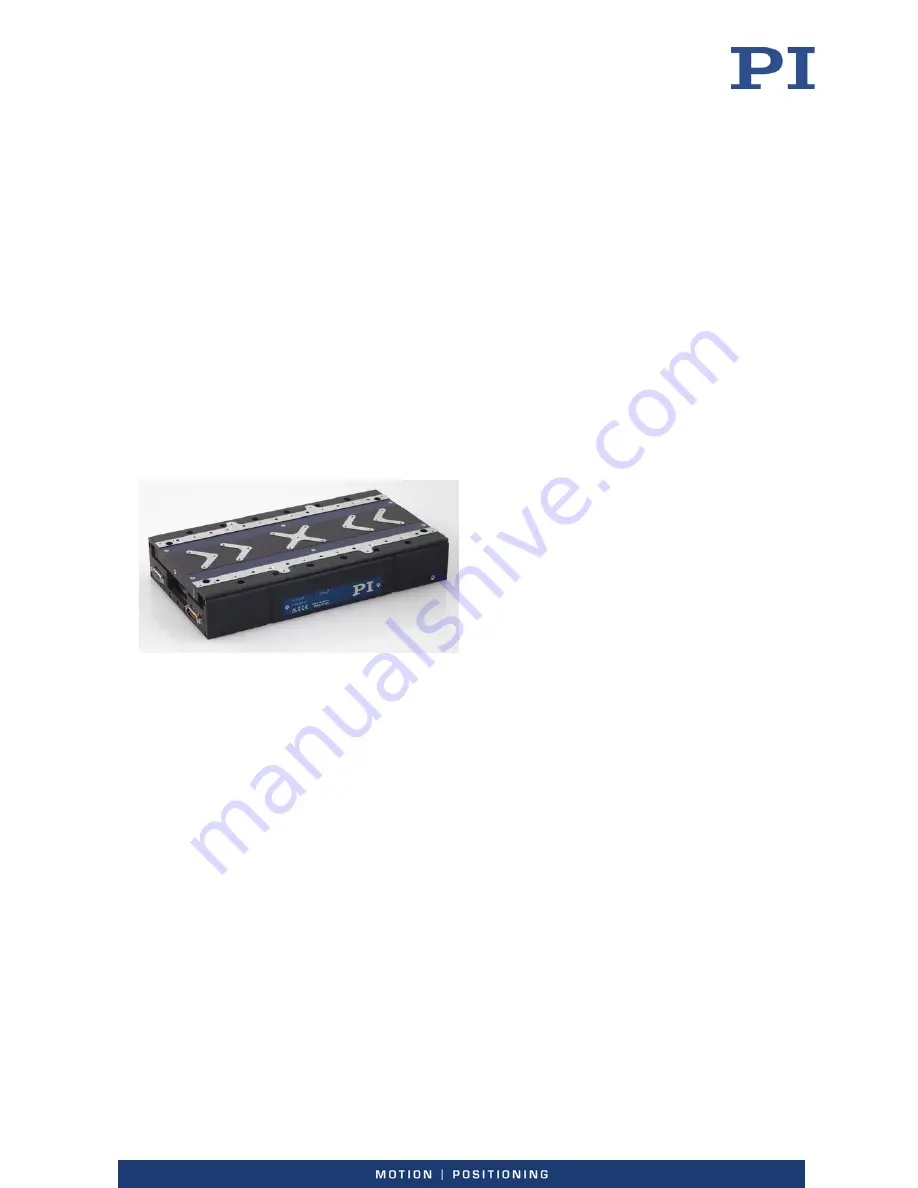
Physik Instrumente (PI) GmbH & Co. KG, Auf der Roemerstrasse 1, 76228 Karlsruhe, Germany
Phone +49 721 4846-0, Fax +49 721 4846-1019, Email [email protected], www.pi.ws
MP160E
V-551 Linear Stage
User Manual
Version: 1.1.1
Date: 05.04.2019
This document describes the following products:
V-551.2D
PIMag® precision linear stage, 160 mm width,
60 mm travel range, 150 N load capacity, PIOne
linear encoder with sin/cos signal transmission,
2 µm sensor signal period, ironless 3-phase
linear motor
V-551.4D
PIMag® precision linear stage, 160 mm width,
130 mm travel range, 150 N load capacity,
PIOne linear encoder with sin/cos signal
transmission, 2 µm sensor signal period,
ironless 3-phase linear motor
V-551.7D
PIMag® precision linear stage, 160 mm width,
230 mm travel range, 150 N load capacity,
PIOne linear encoder with sin/cos signal
transmission, 2 µm sensor signal period,
ironless 3-phase linear motor