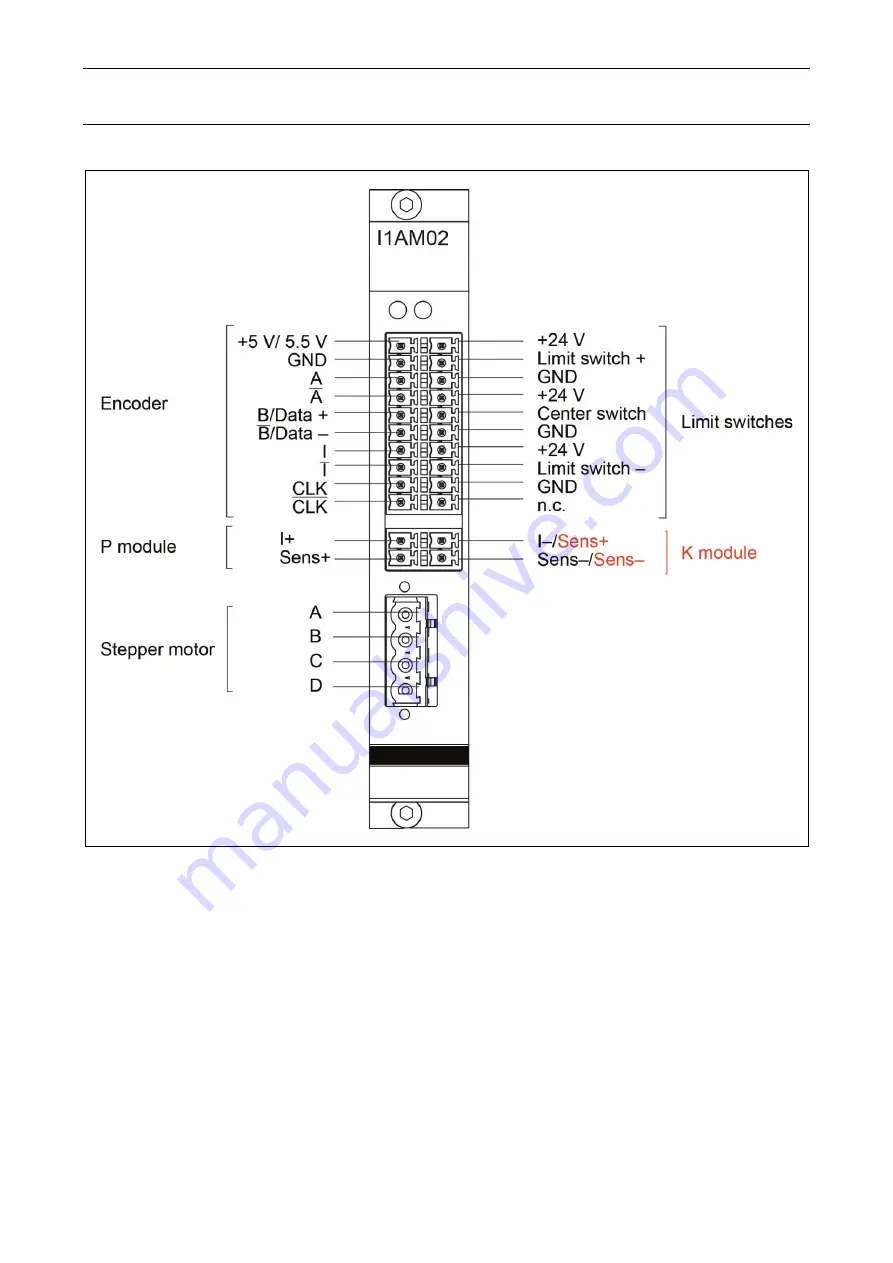
phytron
19
MA 1296-A010 EN
5.2.2 Pin Assignment
In the following the pin assignment:
Fig.2
Pin assignment
Use the specified mating connectors for wiring.
i
CAUTION
– Possible damage!
Damage of the module by wrong connection.
- Do not exchange the 10-pin connector for limit switches with the
10-pin connector for the encoder evaluation.
Summary of Contents for phyMOTIONT I1AM02.1
Page 9: ...phytron 9 MA 1296 A010 EN 4 Technical Data 4 1 Declaration of Incorporation...
Page 10: ...Manual I1AM02 MA 1296 A010 EN 10...
Page 30: ...Manual I1AM02 MA 1296 A010 EN 30 Fig 6 6 wire LVDT RVDT wiring...
Page 31: ...phytron 31 MA 1296 A010 EN Synchronisation Fig 7 Synchronisation wiring...