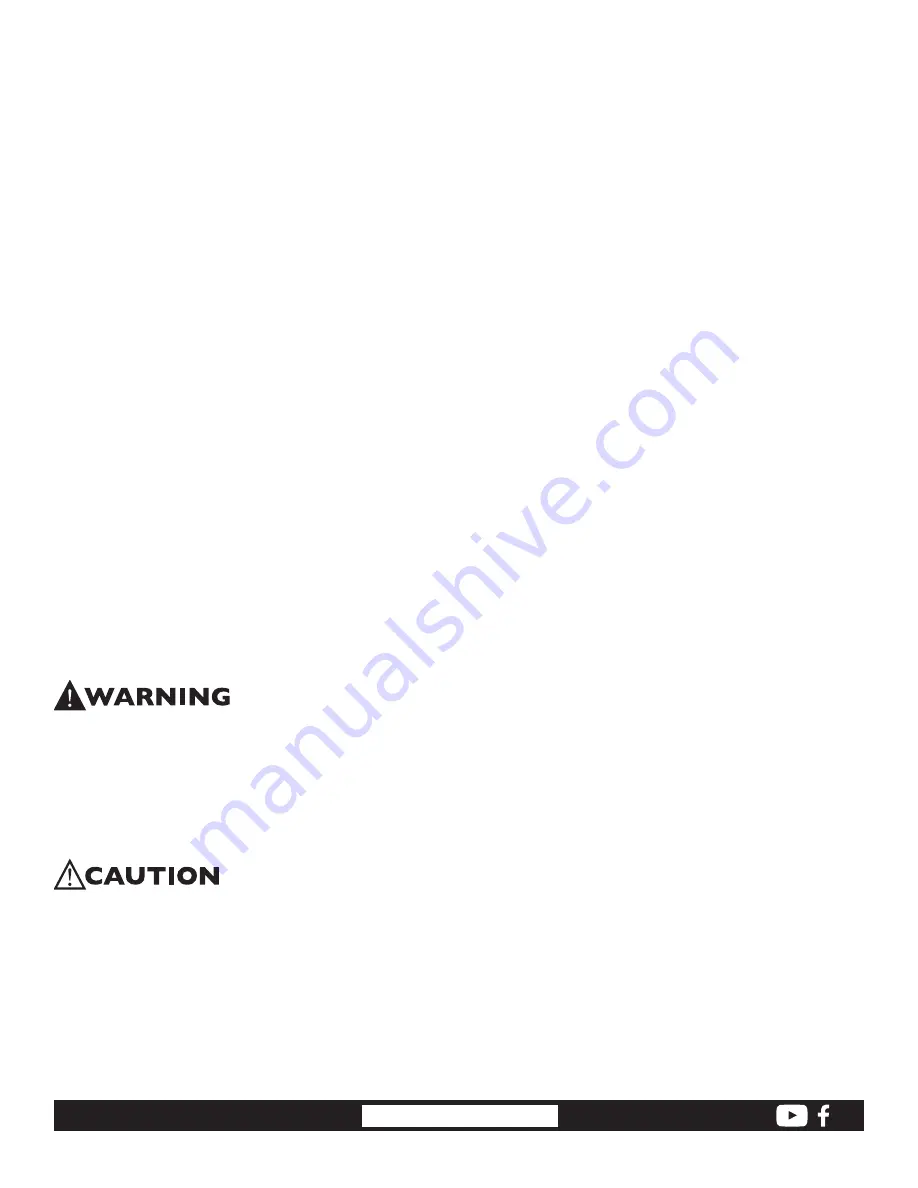
8
USEPHOENIX.COM
1.800.533.7533
4.2 Storage and Freeze Protection
There are two issues to consider when the Phoenix DryMAX
is stored between uses and both pertain to water trapped
in the unit. The first is biological growth and the second is
damage caused by freezing. The effects of the trapped water
can be greatly reduced if precautions are taken to remove
as much as possible before storage.
1. Use the pump PURGE button to reduce the water level in
the reservoir.
2. Stretch the hose flat to drain it completely. Raise one
end above your head and spool hose while draining
water out the other end.
3. To reduce biological growth flush the unit with a
bio-fungicide that is approved for use with copper,
aluminum and polyethylene. To flush:
a. Run the hose to a drain.
b. Plug in the unit but do not turn it on.
c. Remove the air filter. Slowly pour a quart of the
antimicrobial through the heat exchanger
d. Hold in the pump purge switch to reduce the water
level in the reservoir.
e. Flush with water.
4. If the unit will be exposed to freezing temperatures,
after purging, pull back the filter and pour 1 cup (8oz)
of a propylene glycol based anti-freeze through the heat
exchanger. It will flow down into the pump reservoir. Do
NOT purge the solution out of the unit.
5. Dirty filters should be changed prior to long term
storage to prevent biological growth on the filter.
5 Service
WARNING: Servicing the Phoenix DryMAX with its high
pressure refrigerant system and high voltage circuitry
presents a health hazard which could result in death,
serious bodily injury, and/or property damage. Only
qualified service people should service this unit.
CAUTION: Do not operate unit without the top cover in
place.
CAUTION: Do not operate unit without the top cover in
place.
5.1 Technical Description
The Phoenix DryMAX uses a refrigeration system similar
to an air conditioner’s to remove moisture from incoming
air and to add heat to the air that is discharged. Hot, high
pressure refrigerant gas is routed from the compressor
to the condenser coil. The refrigerant is cooled and
condensed by giving up its heat to the air that is about to
be discharged from the unit. The refrigerant liquid then
passes through a filter/drier and capillary tubing which
cause the refrigerant pressure and temperature to drop. It
next enters the evaporator coil where it absorbs heat from
the incoming air and evaporates. The evaporator operates
in a flooded condition, which means that all the evaporator
tubes contain liquid refrigerant during normal operation. A
flooded evaporator should maintain constant pressure and
temperature across the entire coil, from inlet to outlet. The
mixture of gas and liquid refrigerant enter the compressor
after leaving the evaporator coil. The compressor evacuates
the cool refrigerant gas from the accumulator and
compresses it to a high pressure and temperature to repeat
the process.
5.2 Troubleshooting
No dehumidification, control does not light up and unit will
not turn on from power button.
1. Unit unplugged or no power to outlet
2. Defective control board
3. Loose connection in internal wiring
Some dehumidification, air mover runs continuously but
compressor only runs sporadically.
1. Unit is in defrost cycle, DEFROST light on
2. Defrost thermistor defective or loose
3. Loose connection in compressor circuit
4. Defective compressor overload
5. Defective compressor
6. Defective control board
7. Upper housing is not sealed to lower housing
No dehumidification, air mover runs but compressor does
not.
1. Bad connection in compressor circuit
2. Safety float switch closed, check pump reservoir
3. Defective compressor capacitor
4. Defective compressor overload
5. Defective compressor
6. Defective control board
Air mover does not run. Compressor runs briefly but cycles
on and off.
1. Loose connection in blower circuit
2. Obstruction prevents impeller rotation
3. Defective air mover