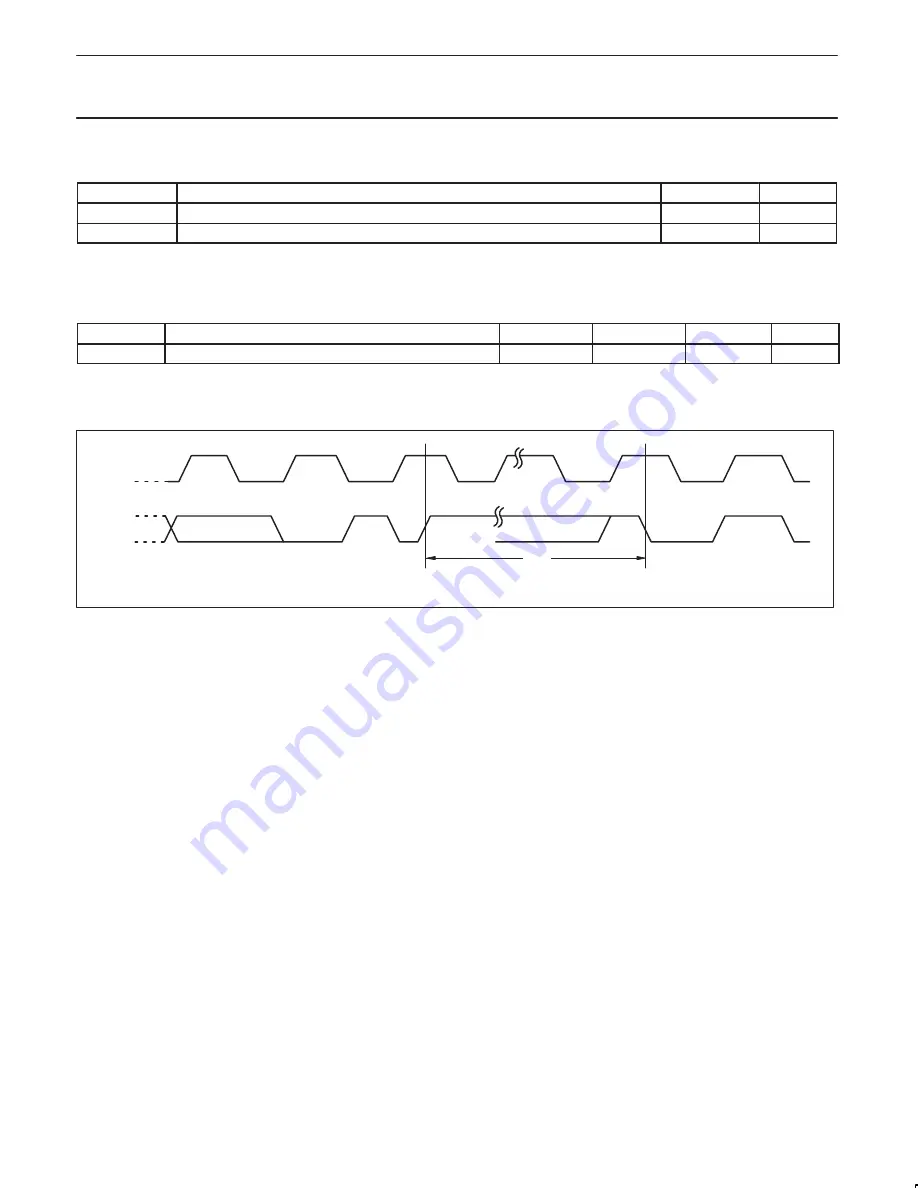
Philips Semiconductors
Product specification
PTN3501
Maintenance and control device
2001 Jan 17
12
POWER-UP TIMING
SYMBOL
PARAMETER
MAX.
UNIT
t
PUR
1
Power-up to Read Operation
1
ms
t
PUW
1
Power-up to Write Operation
5
ms
NOTE:
1. t
PUR
and t
PUW
are the delays required from the time V
CC
is stable until the specified operation can be initiated. These parameters are
guaranteed by design.
WRITE CYCLE LIMITS
SYMBOL
PARAMETER
MIN.
TYP.
(5)
MAX.
UNIT
t
WR
1
Write Cycle Time
–
5
10
ms
NOTE:
1. t
WR
is the maximum time that the device requires to perform the internal write operation.
Write Cycle Timing
SCL
SDA
8th Bit
Word n
ACK
Stop
Condition
Start
Condition
MEMORY
ADDRESS
t
WR
SW00560
Figure 20.