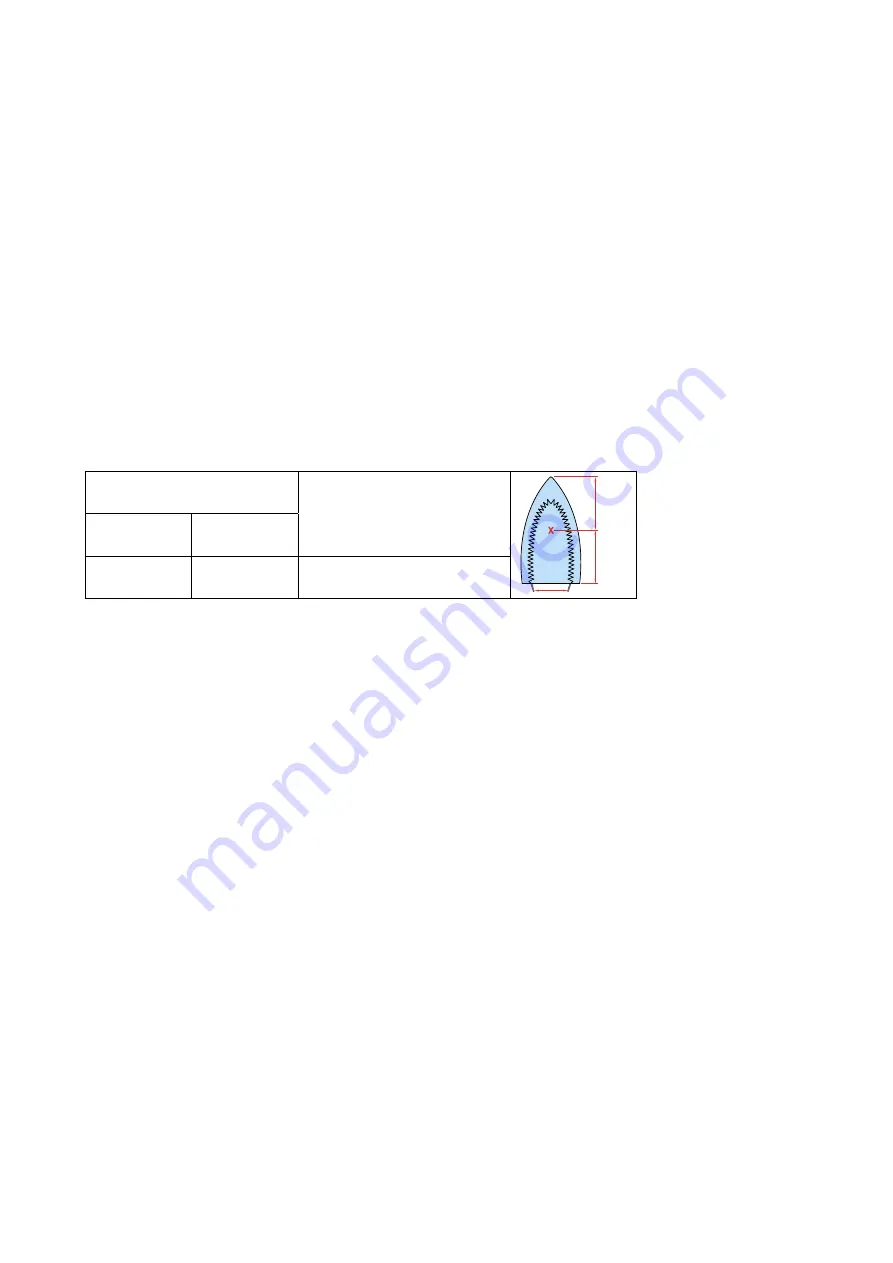
GC9241
10-12
REPAIR INSTRUCTIONS
- Due to the high wattage of the iron, only the specified cord set must be used.
- Should damage be observed on the
HOSE CORD MOUNTED ASSY 15
or
CORD SET 44
, they must be replaced.
Continued usage is not allowed.
- When replacing the
MICROSWITCH ASSY 12
, please dress the 2 attached wires such that they are free of tension. Pulling force
on the wires may affect the steam triggering.
- To avoid damage to the sealing & components of the
BOILER ASSY 36
,
NEVER
clean the boiler assy with vinegar, descaling
agent or other corrosive chemicals.
- When replacing
ELECTROVALVE 37
or
PUMP ASSY 31
, please be reminded to apply loctite at the joints for good sealing.
- After the product has been repaired, it should function properly and has to meet the safety requirements & legal regulations as
laid down & officially established at this moment.
- The following tests are common checks that are conducted on a repaired product before it is returned to the consumer.
1. Soleplate temperature
Check that soleplate temperature is within below requirement.
Measure the temperature of the soleplate after the iron has reached steady state i.e connected to the mains for at least 15 minutes.
The table below shows the temperature requirement.
Soleplate temperature (Deg C)
Materials, for example
Test-
point
==
Minimum
Maximum
120
143
All fabric types
2. Leakage current
Check that leakage current is within IEC requirement.
Measure leakage current between LIVE/NEUTRAL & EARTH.
IEC requirement is that at 230 V supply, the EARTH leakage current must be less than 0.75 mA.
3. Water leakage / Functionality
Check that there is no water leakage from any part of the product during operation.
Check that the functionality of the product (product dependent) eg. steaming, variable steam, SOS, ASO etc is working properly.
4. Loose part
Check that there are no loose parts eg. extra screw in the product that can cause short-circuit or product malfunction.