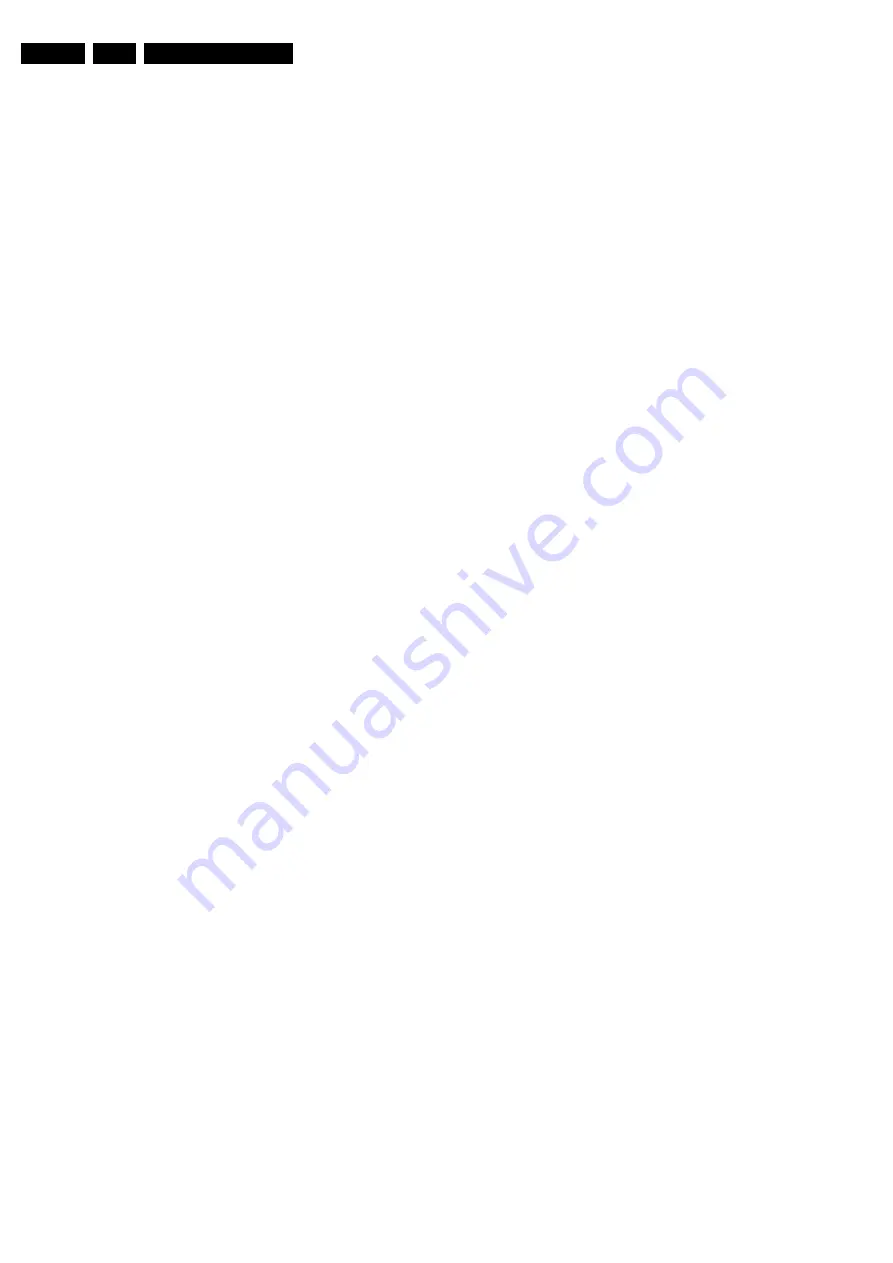
Service Modes, Error Codes, and Fault Finding
5.
5.8.3
ComPair
This chassis does not have an IR transmitting LED (as in MG-
sets). Therefore, a "Service" (ComPair) connector is
implemented at the rear side of the set, which is directly
accessible (as in A10-, EM2E-, EM3E and EM5E-sets). In
addition to this, there is also a blinking LED procedure to show
the contents of the error buffer.
When you use ComPair, you have the possibility to activate a
"stepwise start-up" mode. With this mode, you can initiate the
start-up sequence step by step. This also means that in certain
steps, some protections are not activated. This is sometimes
very convenient during repair.
5.8.4
Protections
Activating SDM via the "service pads" will overrule the
processor-controlled protections, but not the hardware
protections. This means, that the A/D-input protections (5 and
8 V) and the I2C "not-acknowledging" info of the feature box
(FBX) and of the Tuner are overruled.
Caution: When doing this, the service technician must know
what he is doing, as it could lead to damaging the set.
The "ARC"- and/or "BRIDGECOIL" protection are hardly ever
triggered, however:
•
When you suspect the "ARC" protection, look for bad
solder joints and smell. By interrupting resistor 3497, this
protection is disabled (special attention needed!).
•
When you suspect the "BRIDGECOIL" protection, which
can also be due to a too wide picture amplitude, shorten G
and S of the E/W MOSFET 7480. This will disable the
protection. You will now have minimal horizontal amplitude.
Re-align the horizontal amplitude in the SAM menu and
remove the G/S short of TS7480.
5.8.5
Main Supply
The simplest way is, to replace the components of the Main
Supply with repair kit 3122 785 90310.
More detailed way:
1.
Replace FET 7504 and zener 6505.
2.
Remove the SSB panel.
3.
Short B and E of TS7529, in order to put the Main Supply
in "on"-mode (TS7529 is blocking then).
Caution: To prevent that R3403 and TS7443 will be
damaged, first disable the HW-protection of the
deflection circuit. Therefore short circuit C2642 on the
LSP (diagram A4).
4.
Attach a load of 500 O to V_BAT capacitor C2515 (the
supply can not work without a minimum load).
5.
Use a variac, and slowly increase the V_MAINS. Measure
over sensing resistors R3514//15, if a nice sawtooth
voltage becomes available.
6.
Also measure the V_BAT. This may never 141 V.
If it does, there is something wrong in the feedback circuitry
(e.g. regulator 7506).
Note: Be careful when measuring on the gate of FET TS7504.
This circuitry is very high ohmic and can easily be damaged
(first connect ground to measuring equipment, than measure
the gate).
5.8.6
Standby Supply
The simplest way is to replace the components of the Standby
Supply with repair kit 3122 785 90460.
5.8.7
Line Deflection
The simplest way is to replace the components of the Line
Deflection circuitry with repair kit 3122 785 90330.
5.8.8
Frame Deflection
Caution: When the Frame Deflection circuitry is suspected,
one must be careful. Because there is a DC-voltage on the
frame deflection, the beam current could damage the CRT
neck, leading to a defective CRT.
To prevent this from happening, you must:
1.
Interrupt the resistors 3403 and 3404 on the CRT panel
(diagram F1), in order to remove the "filament" voltage
from the tube (no beam current, so no chance of destroying
the CRT).
2.
Interrupt resistor 3403 on the LSP (diagram A4) to disable
the "SUP-ENABLE" line.
3.
Measure with a multi-meter, or better with a oscilloscope,
the functionality of the Frame stage.
4.
After you have found the cause, exchange the defective
component (e.g. TDA8177), and re-solder the interrupted
resistors.
Summary of Contents for 28PW9528
Page 6: ...Directions for Use EN 6 EM5 1E 3 3 Directions for Use ...
Page 7: ...Directions for Use EN 7 EM5 1E 3 ...
Page 8: ...Directions for Use EN 8 EM5 1E 3 ...
Page 9: ...Directions for Use EN 9 EM5 1E 3 ...
Page 10: ...Directions for Use EN 10 EM5 1E 3 ...
Page 11: ...Directions for Use EN 11 EM5 1E 3 ...
Page 12: ...Directions for Use EN 12 EM5 1E 3 ...
Page 13: ...Directions for Use EN 13 EM5 1E 3 ...
Page 14: ...Directions for Use EN 14 EM5 1E 3 ...
Page 15: ...Directions for Use EN 15 EM5 1E 3 ...
Page 16: ...Directions for Use EN 16 EM5 1E 3 ...
Page 32: ...Service Modes Error Codes and Fault Finding EN 32 EM5 1E 5 Personal Notes ...
Page 60: ...60 EM5 1E 7 Circuit Diagrams and PWB Layouts Small Signal Board Diversity Tables ...
Page 134: ...Revision List EN 134 EM5 1E 11 11 Revision List First release ...