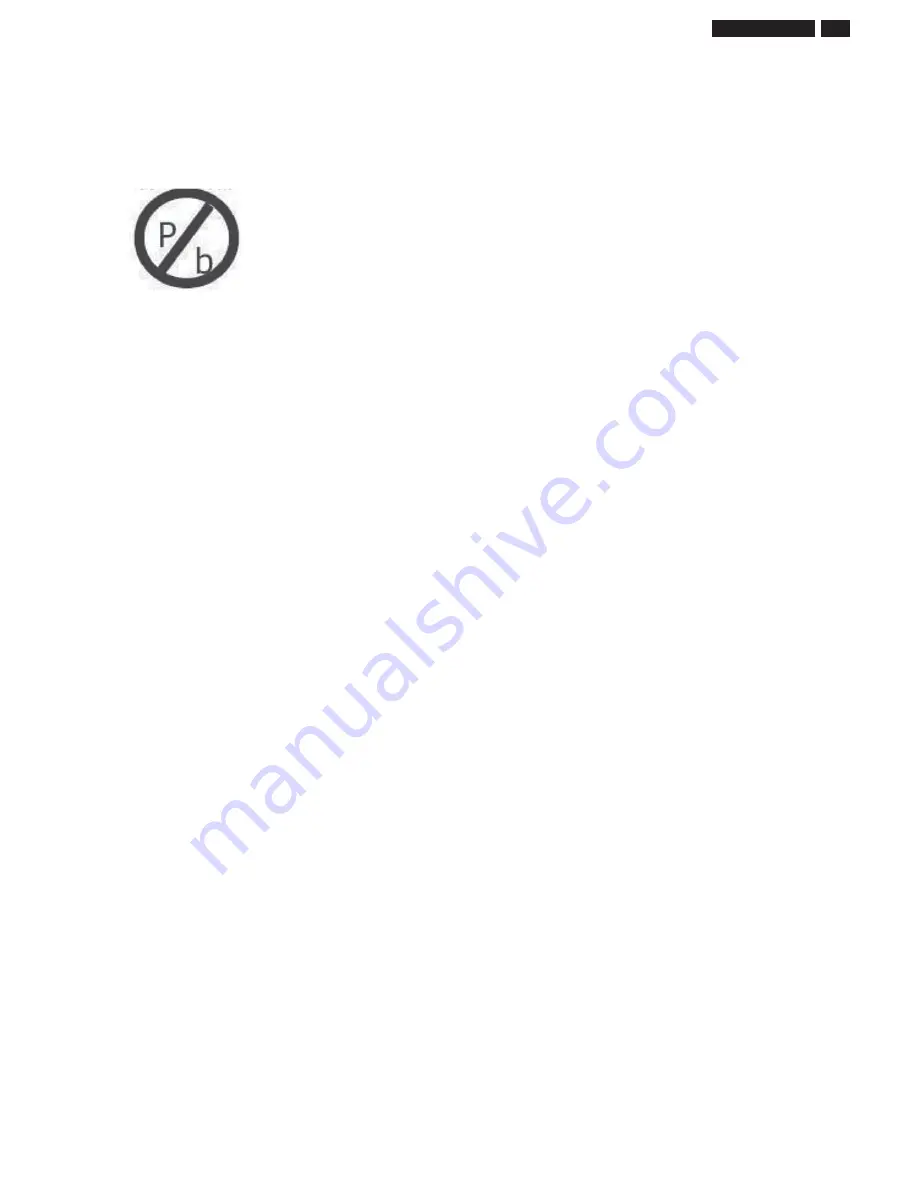
5HSDLU7LSV
3. Lead-free product identification
You can identif lead-free product b Philips-lead-free lo o on PCB.
4. Lead-free product repair instruction
4.1 Use onl lead-free Solder Allo 0622 149 00106(1.2mm SAC305) or 0622 14900108(1.0mm SAC305).
Remark For lead free solderin material please visit
www.alphametals.com
website for details. This is recommended b Philips.
4.2 Use onl ade uate solder tools applicable for lead-free solderin -tin. The solder tool must be able to reach at least a solder-temperature of 400 to
stabili e the ad usted temperature at the solder-tip and to e chan e solder-tips for different applications.
Small Passives/Actives to be removed with thermal twee ers
Automated s stem for IC and BGA repair (Microscope Camera Beam split optics Computer Pro rammer Heat controllers Vacuum s stem Laser
pointer) Solder Hand-Tool (Ad ustable in temperature hei ht Temperature shall be held constant Fle ible tips)
4.3 Ad ust our solder tool so that a temperature around 360 -380 is reached and stabili ed at the solder oint.
Heatin -time of the solder- oint should not e ceed 4 sec. Avoid temperatures above 400 otherwise wear-out of tips will rise drasticall and flu -fluid will
be destro ed. Corrosion of Tool-Spikes can be avoided when usin SAC305 and a temperature of less than 400.
4.4 Mi of lead-free solder-tin/parts with leaded solderin -tin/parts is possible but not recommended. If not to avoid clean carefull the solder- oint from old
tin and re-solder with new tin.
4.5 Use onl ori inal spare-parts listed in the Service-Manuals. Standard-material (consumables) can also be purchased at e ternal companies.
4.6 Special information for lead-free BGA-ICs this ICs will be delivered in so-called dr -packa in to protect the IC a ainst moisture and with lead-free
lo o on it. This packa in ma onl be opened shortl before it is used (soldered). Otherwise the bod of the IC ets wet inside and durin the heatin
time the structure of the IC will be destro ed due to hi h (steam-) pressure. If the packa in was opened before usa e the IC has to be heated up for
some hours (around 90 ) for dr in (Take attention for ESD-protection )
5. Rework on BGA (Ball Grid Arra ) ICs
General
Althou h (LF)BGA assembl ields are ver hi h there ma still be a re uirement for component rework. B rework we mean the process of removin
the component from the PWB and replacin it with a new component. If an (LF) BGA is removed from a P WB the solder balls of the component are
deformed drasticall so the removed (LF)BGA has to be discarded.
Device Removal
As is the case with an component that it is essential when removin an (LF) BGA the board tracks solder lands or surroundin components are not
dama ed. To remove an (LF)BGA the board must be uniforml heated to a temperature close to the reflow solderin temperature. A uniform temperature
reduces the chance of warpin the PWB.
To do this we recommend that the board is heated until it is certain that all the oints are molten. Then carefull pull the component off the board with a
vacuum no le. For the appropriate temperature profiles see the IC data sheet.
Area Preparation
When the component has been removed the vacant IC area must be cleaned before replacin the (LF) BGA. Removin an IC often leaves var in
amounts of solder on the mountin lands. This e cessive solder can be removed with either a solder sucker or solder wick. The remainin flu can be
removed with a brush and cleanin a ent. After the board is properl cleaned and inspected appl flu on the solder lands and on the connection balls of
the (LF)BGA
Note Do not appl solder paste as this has shown to result in problems durin re-solderin .
Device Replacement
The last step in the repair process is to solder the new component on the board. Ideall the (LF) BGA should be ali ned under a microscope or
ma nif in lass. If this is not possible tr to ali n the (LF)BGA with an board markers. To reflow the solder appl a temperature profile accordin to
the IC data sheet. So as not to dama e nei hbourin components it ma be necessar to reduce some temperatures and times.
More Information
For more information on how to handle BGA devices visit this URL http //www.at ourservice.ce.philips.com (needs subscription). After lo in select
Ma a ine then o to Workshop Information. Here ou will find Information on how to deal with BGA-ICs.
241
%
4L
3
LC
'
Summary of Contents for 241B4LPCB/00
Page 5: ...241B4LP LCD 5 Troubleshootingʳ ...
Page 6: ...6 241B4LP LCD Troubleshooting ...
Page 16: ... 3 4V UHTXHQWO VNHG 4XHVWLRQV ...
Page 17: ... 3 4V UHTXHQWO VNHG 4XHVWLRQV ...
Page 20: ... 3 6HUYLFH WRRO DUGZDUH 3 0 FRGH 1 ...
Page 21: ... 3 6HUYLFH WRRO 6RIWZDUH ZULWLQJ WRRO DV ULWHU V4 54 ZULWLQJ WRRO 4 9 ...
Page 25: ...241B4LP LCD 25 DDC Instructions Step 2 Press Open File then choose 241B4LP DDC FILE Fig 5 ...
Page 32: ... 3 LUPZDUH 8SJUDGH IRU 38 6WHS 3UHVV XWR WR XSJUDGH 6WHS 8SJUDGH 2 ...
Page 34: ...34 241B4LP LCD LULQJ LDJUDP ...
Page 35: ...241B4LP LCD 35 ORFN LDJUDP ...
Page 41: ...S calar Diagram C B A 41 241B4LP LCD ...
Page 44: ...44 241B4LP LCD Power Diagram C B A ...
Page 46: ...Control Diagram C B A 46 241B4LP LCD ...
Page 48: ...L D D r C B A 48 241B4LP LCD ...
Page 50: ...Control Diagram C B A 50 241B4LP LCD ...
Page 52: ...JACK Diagram C B A 52 241B4LP LCD ...
Page 54: ...TX Diagram C B A 54 241B4LP LCD ...
Page 77: ...lo e e 241B4LP LCD 77 ...