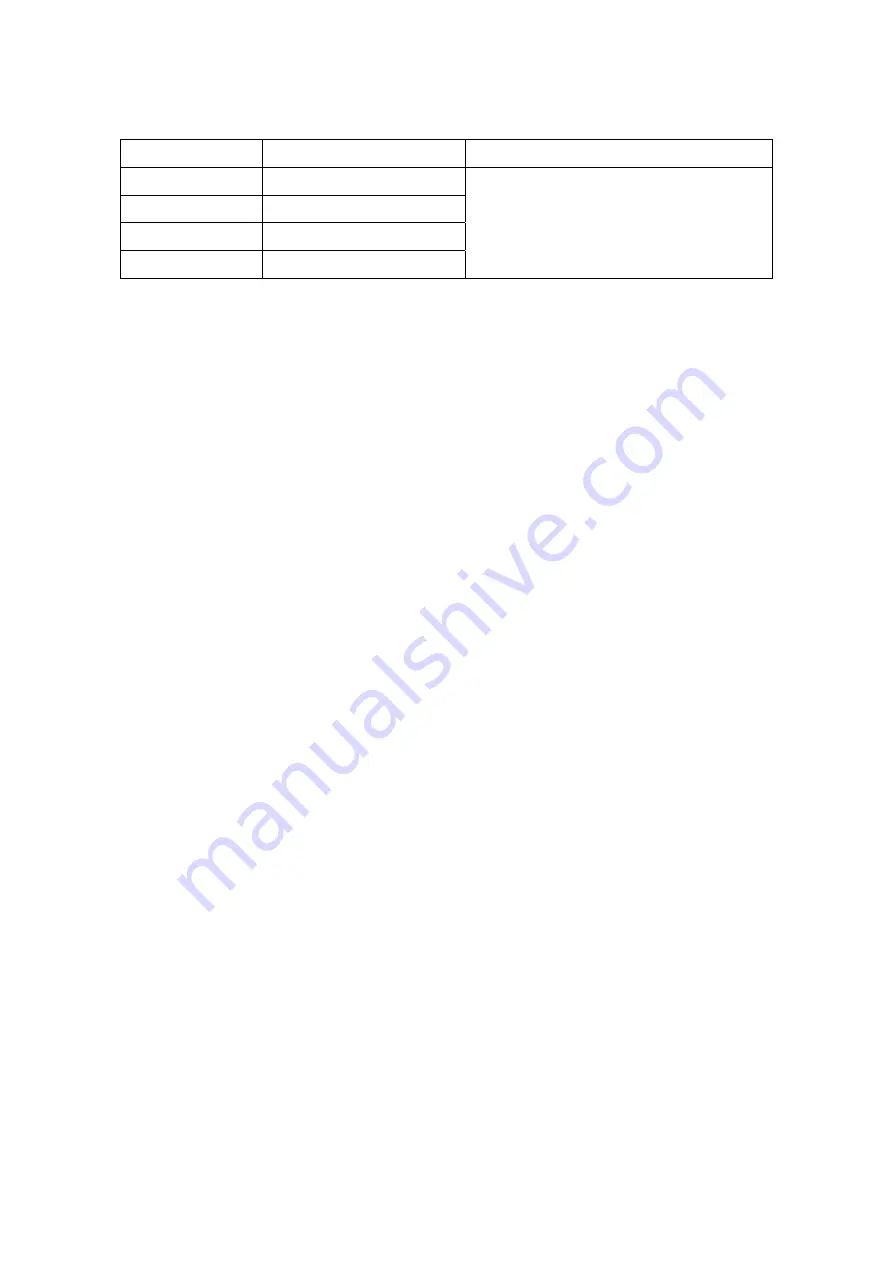
(1) Purge flow
Dry-Vac Model
Amount (
㎥
/min N)
Remark
200 0.55
300 0.55
400
0.8 ~ 0.86
800 Above
1
This purge amount can
Vary as per the pump’s vacuum level
(2) Type of Cooling Purge
①
Standard : Atmosphere purge through air filter
②
Using Heat Exchanger : Recycle process gases from discharge after cooled through the
heat exchanger.
③
Using Inert gases like N2 etc. Instead of atmosphere or cooled process gas.
●
Sealing Purge
This purge is required during the operation and intended to pressurize the front end cover with
Inert gas like N2 so that the process gas or fluid can not enter into the timing gear set and
bearings. You can use either one of two plugs provided on the top of Front End Cover for this
sealing purge connection.
The purge pressure is below 0.5
㎏
/
㎠
G and the leak rate for our Mech. seal is below 3cc/Hr.
Also our Mechanical seal can seal pressure up to 3
㎏
/
㎠
G.
●
Cleaning Purge
This purge is required to clean inside the pump before stopping the pump. Before stopping the
pump, purge N2 gas, steam or cleaning agent for 20 to 30 minutes after closing the main valve
on suction side to clean sticky process materials or process gases. This purge is important
when pumping corrosive/toxic gases or sticky materials like resin.
●
Pump Steam Flushing
After each process, run the pump for 10
∼
20 minutes without load after close main suction
valve (Dry run, Cleaning purge).
This is to remove & clean process gases / condensed vapors the pump during the process.
These process materials build up inside the pump can be the reason for pump overload when
restart the pump for next process.
Also, when restart the pump after a certain period later, these process materials can be cause
for pump seizure or overload.
In this case, flush steam the pump internals & Screws with following procedure instead of
rotating the pump with force.
◐
Steam Flushing Method (after operation)
(1) Process materials that require Steam flushing: Monomer, Polymer, Resin, etc.
(2) Steam pressure: approx. 1
㎏
/
㎠
G
(3) Flushing Procedure
5