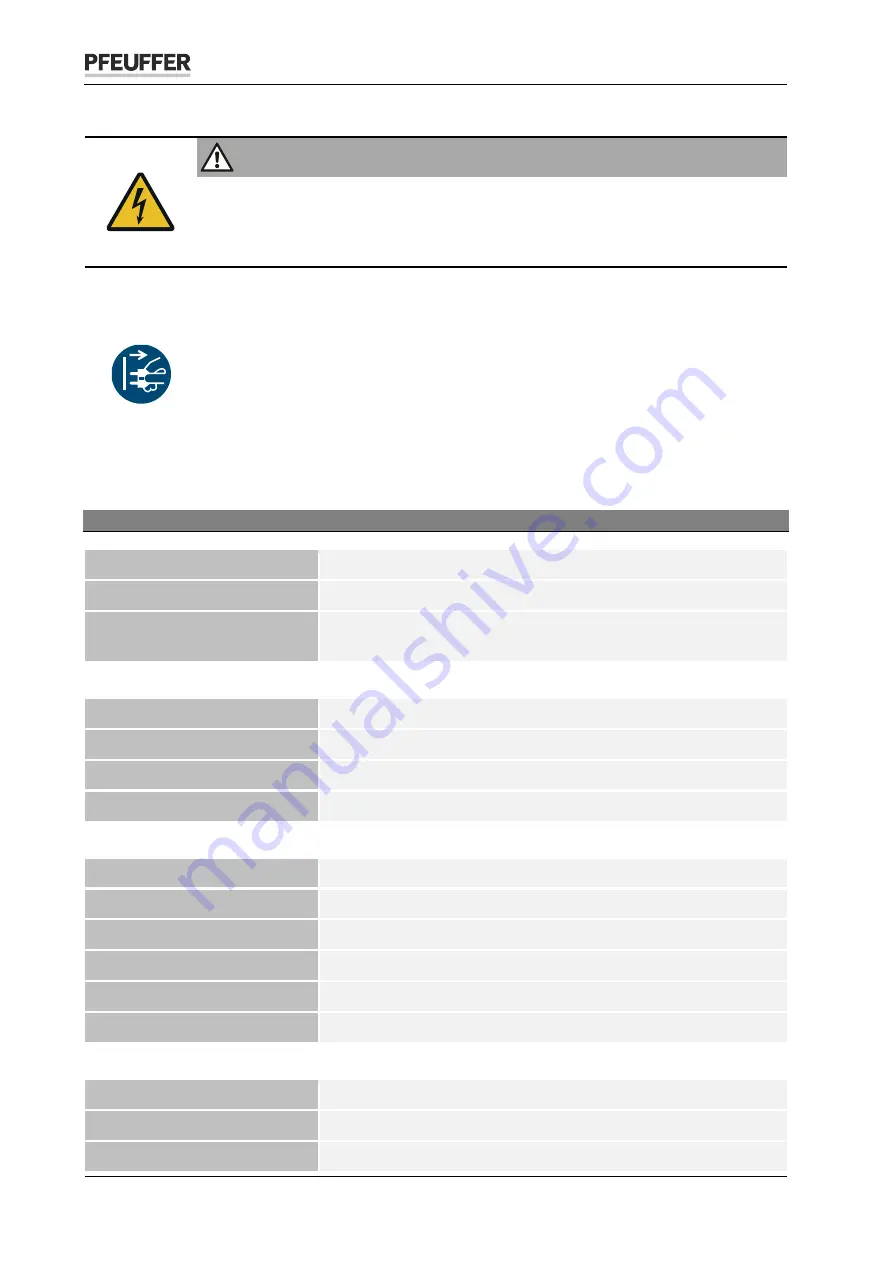
Technical data
14 | 40
Operating instructions sample cleaner SLN 4 | Revision 4
2.9
Deactivation procedure
DANGER
Touching live parts can be fatal!
The following deactivation procedure must be carried out before cleaning, maintaining
or repairing the machine (only by skilled personnel):
Deplete the sample cleaner.
Disconnect the machine from the mains:
Disconnect the plug/socket combination from the power supply.
It must be possible to ensure that the plug remains under the direct supervision of the person in the
hazardous area.
Make sure that water, vapour or dust cannot enter the electronic area when cleaning.
3
Technical data
Sample cleaner
SLN 4
Cleaning and grading all grain crops
Sample quantity
approximately 1 kg
Material/transported material
(sub-supplier)
Grains, peas, rape seed, maize and similar granular bulk goods
3.1
Dimensions and weight
Height
970 mm
Width
580 mm
Length
680 mm
Weight
85 kg
3.2
Power supply
Supply voltage/Frequency
230 V
AC
+ 6% - 10%, 50 Hz
Power consumption
500 VA
Number of phases
1 Ph / PE
Earth conductor
SL (yellow/green) in mains cable
Frequency
± 1%
Installation instructions
Executed as per VDE
3.3
General information
Temperature
+5 °C – +40 °C
Humidity
20 – 80% non-condensing
Acoustic level
L
PA
= 77 dB
(A)
as per measurement report