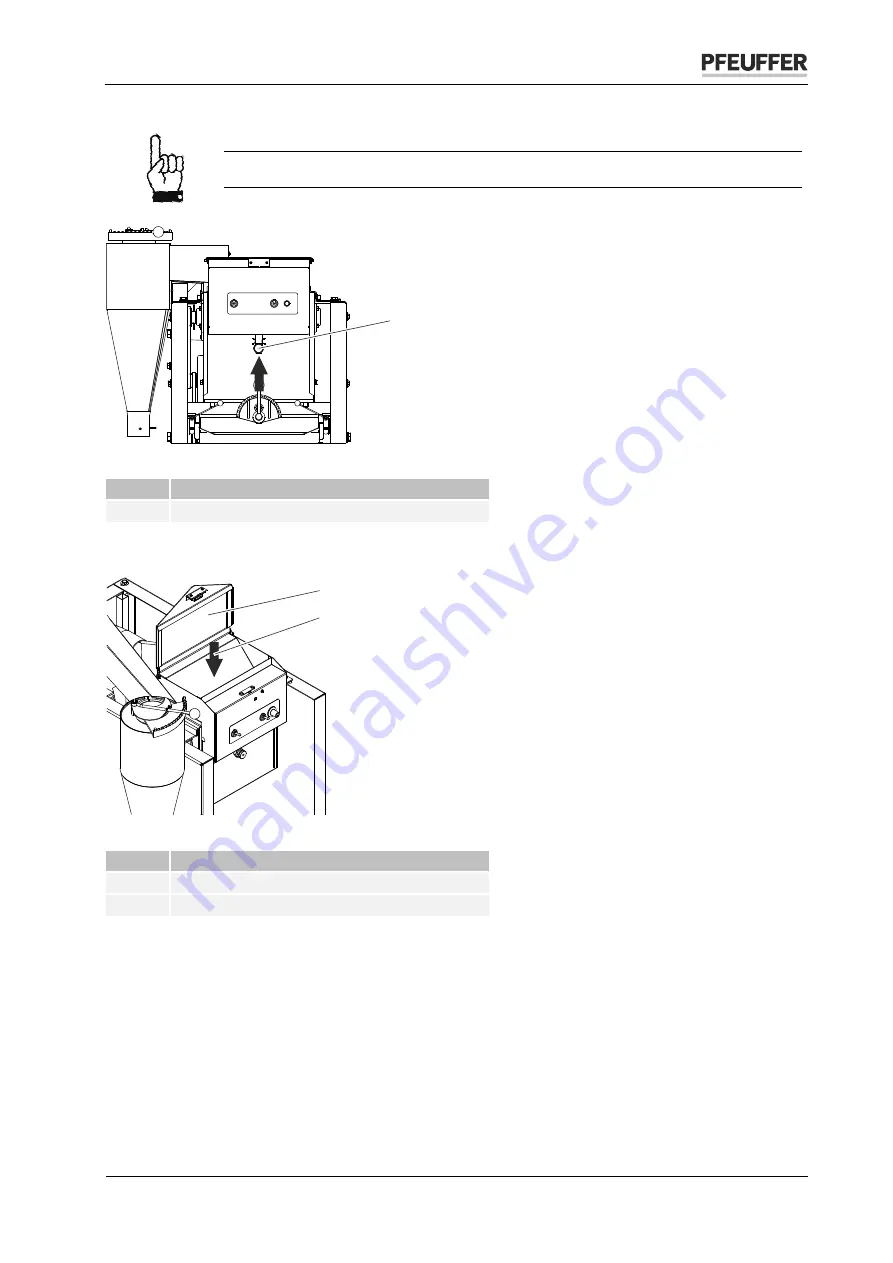
Operation
Revision 3 | Operating instructions sample cleaner MLN
23 | 38
Close the deawner bottom by pressing the locking lever.
The deawner bottom must be manually closed again after every cleaning process!
Figure 12: Locking lever for deawner bottom
Item
Name
1
Locking lever
Open the cover of the filling container and pour the sample in the deawner.
Figure 13: Fill in the sample
Item
Name
1
Filler cap opened
2
Sample
Set the deawner time on the potentiometer.
Close the filler cap and the door of the sample cleaner.
Switch the control switch
ON
.
The sample cleaner starts.
o
A limit switch system is integrated into the filler cap.
The deawner will start only if the filler cap is closed.
1
2
1