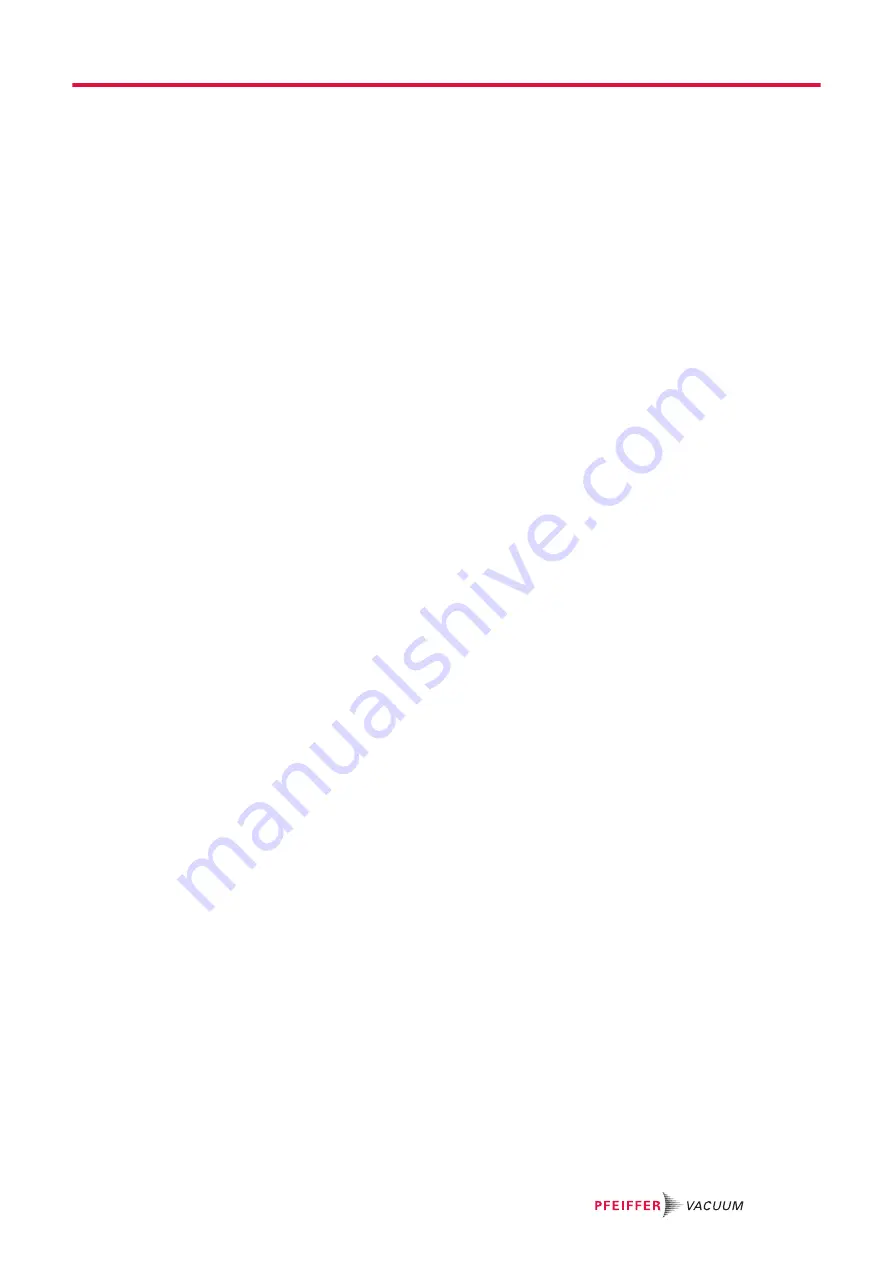
11 Spare parts
► Have the vacuum pump part number, and any other necessary details from the rating plate, to
hand when ordering spare parts.
► Only use original spare parts.
11.1 Set of seals for version with RSSR
The set of seals contains:
● all sealing parts such as O-rings, radial shaft seal rings (without protective sleeve) and supporting
rings,
● flat seals, square washers and profile seals.
Not included are centering rings for connecting the pumps for the suction and pressure side.
11.2 Set of seals for version with axial face seal (axial face seal separate)
The set of seals contains:
● all sealing parts such as O-rings, flat seals, square washers
Not included are centering rings for connecting the pumps for the suction and pressure side.
11.3 Axial face seal, complete
The set of seals contains:
● the seal components with all corresponding O-rings
11.4 Maintenance kit for version with RSSR
The maintenance kit contains:
● all seals in the RSSR area,
● all sealing rings of the filling and drain screws and both O-rings for the device cover and cap,
● the coupling buffer (toothed ring).
11.5 Overhaul kit for versions with RSSR
The overhaul kit contains:
● the set of seals
● the ball bearing, the roller bearing and the protective sleeve
● the circlips, the groove nuts, the sight glasses and the oiler
● the coupling buffer (toothed ring).
11.6 Overhaul kit for versions with axial face seal
The overhaul kit contains:
● the set of seals
● the ball bearing, the roller bearing
● the locking plates, the groove nut and the sight glasses.
11.7 Set of gear wheels
The gear wheel kit includes:
● Main and auxiliary wheel
Spare parts
51/56