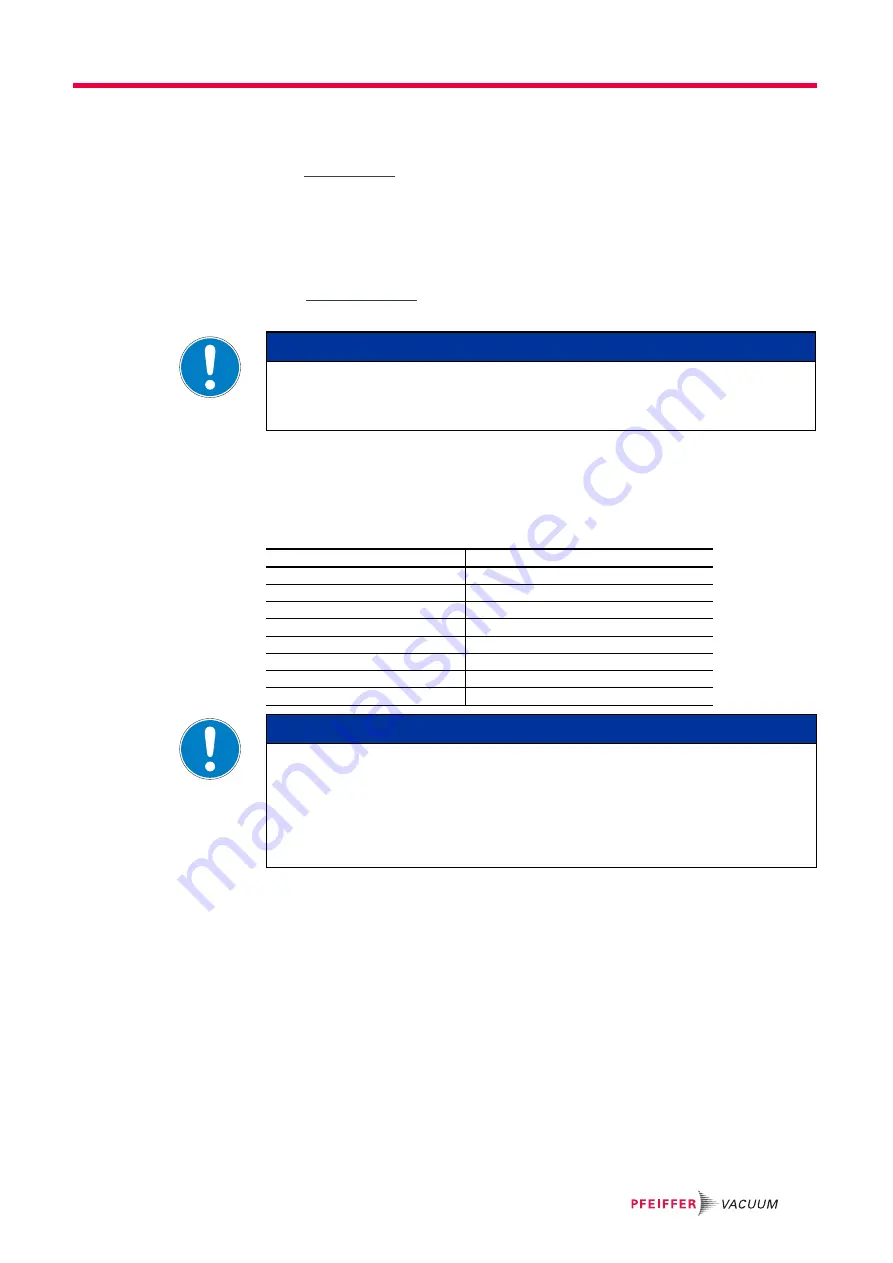
Operation
21
Example for Okta 18000 with 0.5 hPa intake pressure and 8% sealing gas quantity:
This applies to exhaust pressures > 100 hPa:
Adjusting the flush-
ing fluid quantity
Set max. flushing quantity in acc. with the following table; use flow meter.
– On pumping stations without an intermediate condenser or collecting containers
the quantity of fluid should be selected according to the smallest pump in the pump-
ing station:
Dry the pump completely inside after flushing.
6.3
Switching off and venting
In the case of clean processes that convey pure gases, the pump can be switched off in
every pressure range and directly after the process end. When the evacuated medium
in the suction chamber causes strong contamination or deposits, the vacuum pump
should be flushed with air or nitrogen after the process end.
If venting of the vacuum chamber is not required, then the intake port valve must be
closed before switching off the pump in order to prevent venting of the vacuum chamber.
Q
S
Q
S
=
=
= 0,71 Nm
3
/h
18000 ·0,5 ·0,08
1013
S
th
· (p
V
-
p
· A
S
p
0
Q
S
=
Δ
)
NOTICE
High pressure in the sealing gas line when the pump is switched off!
Risk of damage to the pump seals.
Lower sealing gas pressure to < 1200 hPa or stop sealing gas feed immediately.
Pump type
max. flushing quantity
Okta 18000
3 l/min
Okta 8000
2 l/min
Okta 6000
1.75 l/min
Okta 4000
1.5 l/min
Okta 2000
1.0 l/min
Okta 1000
0.5 l/min
Okta 250/500
0.25 l/min
Okta 300/600
0,25 l/min
NOTICE
High pressures are generated in the working chamber of the pump!
Exceeding the specified flushing quantities can lead to destruction of the pump.
Do not exceed the indicated flushing quantity at 3000 hPa in the indicated time peri-
od.
Drain the fluid again.
Always check the vapour compatibility of the downstream pumps.