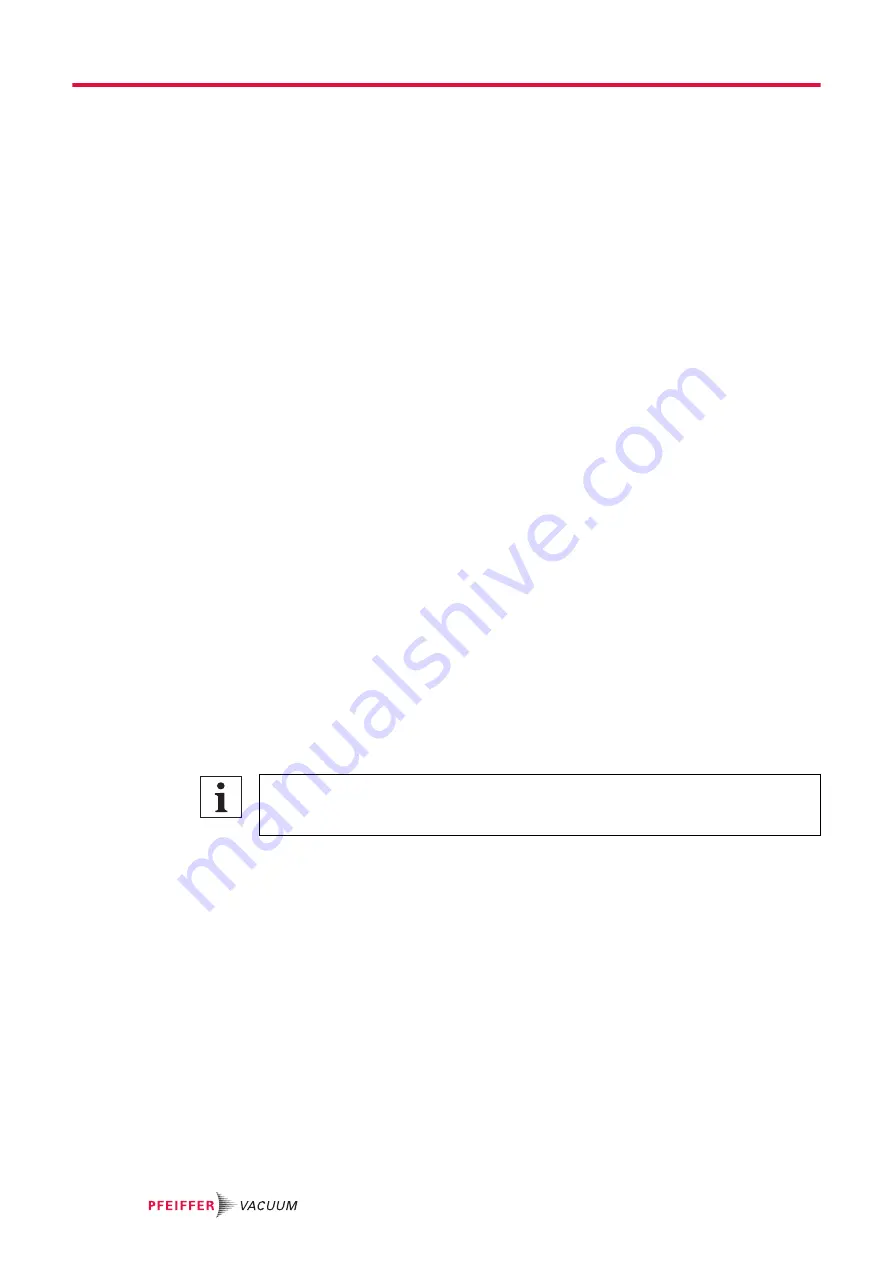
Required aids
● Collection vessel (> 0.5 l)
Draining the operating fluid
1. Unscrew the filler screw.
– Be careful with the O-ring.
2. Place a collection receptacle below the drain hole.
3. Unscrew the drain screw.
– Be careful with the O-ring.
4. Allow operating fluid to drain into collection receptacle.
Agitate remaining operating fluid
1. Screw in the filler screw.
– Be careful with the O-ring.
2. Screw in the drain screw.
– Be careful with the O-ring.
3. Switch on the vacuum pump with the vacuum flange open for a maximum of 5 seconds.
Drain remaining operating fluid
1. Unscrew the drain screw.
– Be careful with the O-ring.
2. Gently tilt the vacuum pump.
3. Drain remaining operating fluid.
4. Screw in the drain screw.
– Replace the O-ring.
– Tightening torque:
6 Nm
5. Dispose of old operating fluid according to applicable regulations.
Filling fresh operating fluid
1. Screw the drain screw in up to the stop.
– Be careful with the O-ring.
– Tightening torque:
6.0 Nm
2. Fill new operating fluid.
3. Check level.
4. Screw the drain screw in completely.
– Be careful with the O-ring.
– Tightening torque:
0.3 Nm
7.4.3 Rinsing and cleaning the rotary vane vacuum pump
Cleaning by changing the operating fluid
Pfeiffer Vacuum recommends, in cases of heavy contamination with process residues,
cleaning the inside of the vacuum pump with several operating fluid changes.
Prerequisites
● Fresh operating fluid filled
Required tools
● Allen key,
WAF 5
● Calibrated torque wrench (tightening factor ≤ 2.5)
Required aids
● Collection vessel (> 0.5 l)
Change operating fluid for cleaning
1. Operate the vacuum pump with the gas ballast open, until it is warm.
2. Perform an operating fluid change.
3. Check the pollution level and repeat the changing of the operating fluid if necessary.
4. Replace the corresponding filter elements wherever the accessory is installed.
Maintenance
38/62