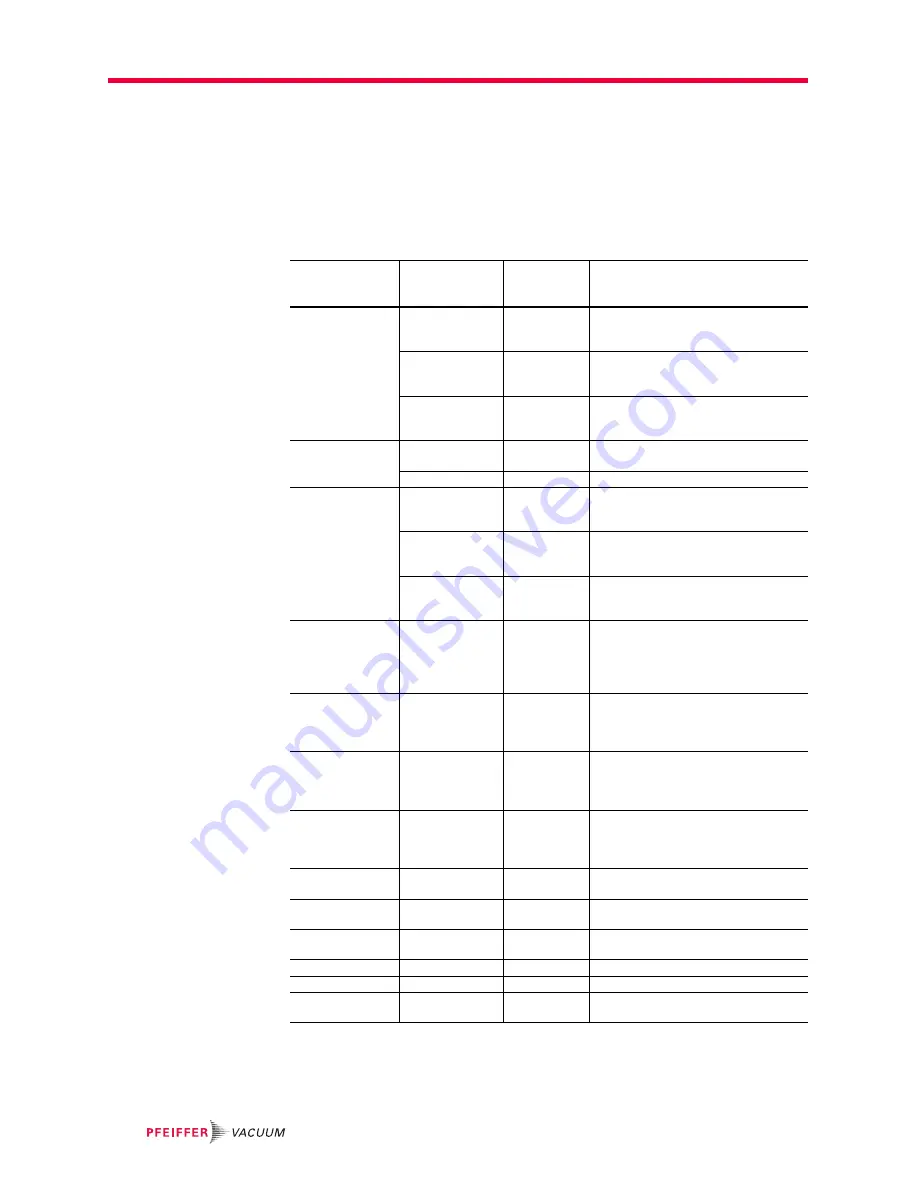
32
Spare parts
11 Spare parts
11.1 Spare parts packages
The spare parts packages listed here are only applicable for standard models.
Please state all information on the rating plate when ordering spare parts. Other spare
parts than those described in this manual must not be used without the agreement of
Pfeiffer Vacuum.
Spare parts pack/
spare parts
Revision index /
Version
No.
consisting of the parts correspondent
to exploded views on the following
pages
Sets of seals
"A"
PK E00 023 -T 48, 106, 144, 240, 242, 244, 246, 248, 250,
251, 254, 256, 258, 260, 262, 264, 266,
269, 270
"C"
PK E00 025 -T 48, 102, 144, 147, 240, 242, 244, 245, 246,
247, 248, 250, 251, 255, 256, 258, 260,
262, 264, 266, 269, 270
"C"/DUO 255 M
PK E00 027 -T 48, 102, 144, 147, 240, 242, 244, 245, 246,
247, 248, 250, 251, 254, 255, 256, 258,
260, 262, 264, 266, 267, 269, 270
Maintenance kit
"A"
PK E01 033 -T 29, 59, 60, 142, 144, 145, 173, 250, 254,
260, 264, 266, 269
"A"/DUO 255 M
PK E01 035 -T 59, 60, 228, 247, 250, 256, 264, 269
Overhaul kit
"A"
PK E02 036 -T PK E00 023 -T, 15, 17, 24, 29, 30, 31, 38,
52, 53, 56, 59, 60, 65, 70, 81, 85, 88, 98,
99, 142, 145, 173, 206
"C"
PK E02 038 -T PK E00 025 -T, 17, 24, 29, 30, 31, 38, 52,
53, 56, 59, 60, 65, 70, 81, 85, 88, 98, 99,
142, 145, 148, 173, 230
"C"/DUO 255 M
PK E02 051 -T PK E00 027 -T, 17, 24, 29, 30, 31, 38, 52,
53, 56, 59, 60, 65, 70, 81, 85, 88, 98, 99,
142, 145, 148, 173, 230
Pumping system, P3 DUO 255
PK E03 013 -T 22, 23, 24, 25, 26, 27, 28, 29, 30, 31, 32,
33, 34, 36, 37, 38, 39, 41, 42, 43, 44, 48,
52, 53, 54, 56, 57, 58, 59, 60, 254, 256,
258, 260, 280, 282, 287, 288, 294, 296,
312, 338
Pumping system, P3 DUO 255 M
PK E03 050 -U 22, 23, 24, 25, 26, 27, 28, 29, 30, 31, 32,
33, 34, 36, 37, 38, 39, 41, 42, 43, 44, 48,
52, 53, 54, 56, 57, 58, 59, 60, 254, 260,
280, 282, 287, 294, 296, 338
Pumping system, D1 DUO 255
PK E03 014 -T 22, 23, 24, 25, 26, 27, 28, 29, 30, 31, 32,
33, 34, 36, 37, 38, 39, 41, 42, 43, 44, 48,
52, 53, 54, 56, 57, 58, 59, 60, 254, 260,
280, 282, 287, 294, 296, 338
Pumping system, D1 DUO 255 M
PK E03 051 -U 22, 23, 24, 25, 26, 27, 28, 29, 30, 31, 32,
33, 34, 36, 37, 38, 39, 41, 42, 43, 44, 48,
52, 53, 54, 56, 57, 58, 59, 60, 254, 260,
280, 282, 287, 294, 296, 338
Fore-vacuum safety
valve set
DUO 255 -/M
PK E04 008 -T 59, 79, 80, 81, 82, 83, 84, 85, 88, 98, 99,
262, 264
Exhaust valve set,
stage I
DUO 255 -/M
PK E05 011 -T
56, 59, 60
Exhaust valve set,
stage Ii
DUO 255 -/M
PK E05 013 -T 48, 52, 53, 54, 258, 294
Coupling set
DUO 255
PK E06 006 -T 170, 171, 173, 175
Set of vanes
DUO 255 -/M
PK E08 028 -T 30, 31, 38
Filter insert for gas
ballast valve
DUO 255 -/M
P 0996 094
123