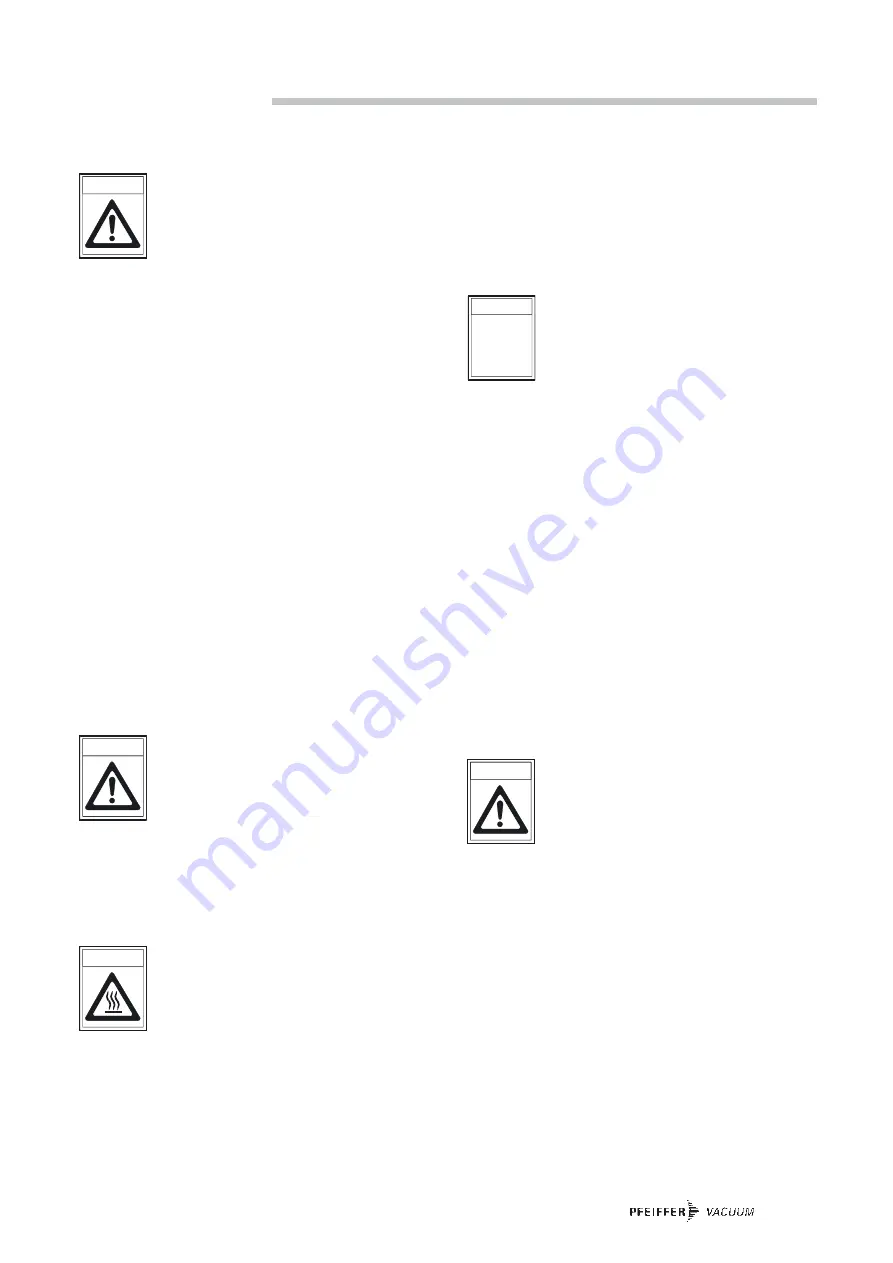
13
➡
Drain off remaining operating fluid.
➡
In the case of serious contamination, the operating fluid
will have to be changed several times.
➡
Screw in operating fluid drain screw 43 with O-ring.
When carrying out servicing work, take the following
precautions:
Always ensure the pump cannot be switched
on when carrying out any work on the pump. If
necessary, remove the pump from the system to
carry out inspection work.
➡
Only dismantle the pump as far as is necessary in order to
repair defects.
➡
Dispose of used operating fluid in compliance with local
regulations.
➡
When working with synthetic operating media, toxic
substances and substances contaminated with corrosive
gases, the relevant instructions governing their use must
be observed.
➡
Only use benzine or similar agents for cleaning pump
parts. Do not use soluble cleaning agents.
6.1. Changing The Operating Fluid
The rate of deterioration of the operating fluid depends on the
pump applications.
➡
The level of deterioration of organic operating fluids (for
example P3) can be read off from the colour scale in
accordance with DIN 51578 on the supplementary sheet
PK 800 219 BN/B, on request.
– The colour scale enables precise colour determination.
➡
Fill a specimen in a test tube or some similar vessel and
test by holding against the light.
➡
Where the discolouration is dark yellow to red brown
(equivalent to 4 ... 5 on the scale) change operating fluid.
Where organic operating fluids, for example P3,
are involved, the operating fluid should be
changed every 8000 h; at least once a year!
Replacing The Operating Fluid
➡
Switch off the pump.
➡
Unscrew operating fluid drain screw 43 and drain
operating fluid.
The operating fluid temperature can be as high
as 80 °C. During maintenance and repair work,
process related toxic gases and vapours can
escape from the operating fluid which may
become contaminated with harmful substances
(radioactive, chemical etc.).
Disposal of used operating fluid is subject to the relevant
regulations.
➡
Screw in operating fluid drain screw 43.
➡
Allow pump to run for about 10 seconds with open vacuum
flange.
WARNING
CAUTION
WARNING
6. Maintenance
6.2. Cleaning The Oil Filter
Also clean the oil filter 181 every time you chan-
ge the pump fluid.
➡
Unscrew screws 184 and remove the cover 183, take care
with the o-ring.
➡
Unscrew screws 185 and lift the oil filter 181 out of the
pump on flange 186.
➡
Dismantle the oil filter as shown below and clean the star-
shaped filtering sieve 187 in benzine (naphtha) or similar
cleaning agent.
➡
Reassemble in reverse order.
Filling in operating fluid
➡
Check the drain plug 43 for tight seat.
➡
Remove operating fluid filler screw 42.
➡
Fill up the new operating fluid; refer to rating plate for
correct quantity (UNO 250 A --> 30 l, DUO 250 A --> 23 l).
➡
Replace operating fluid filler screw 42; be careful with the
O-ring.
➡
Check operating fluid level at the sight glass as per
section 4.1..
Operating fluid can contain substances from
the medium pumped. Operating fluid must be
disposed of in accordance with the local
respective regulations.
Please request safety instruction data sheets for operating
fluids from Pfeiffer Vacuum.
WARNING
☞
PLEASE NOTE