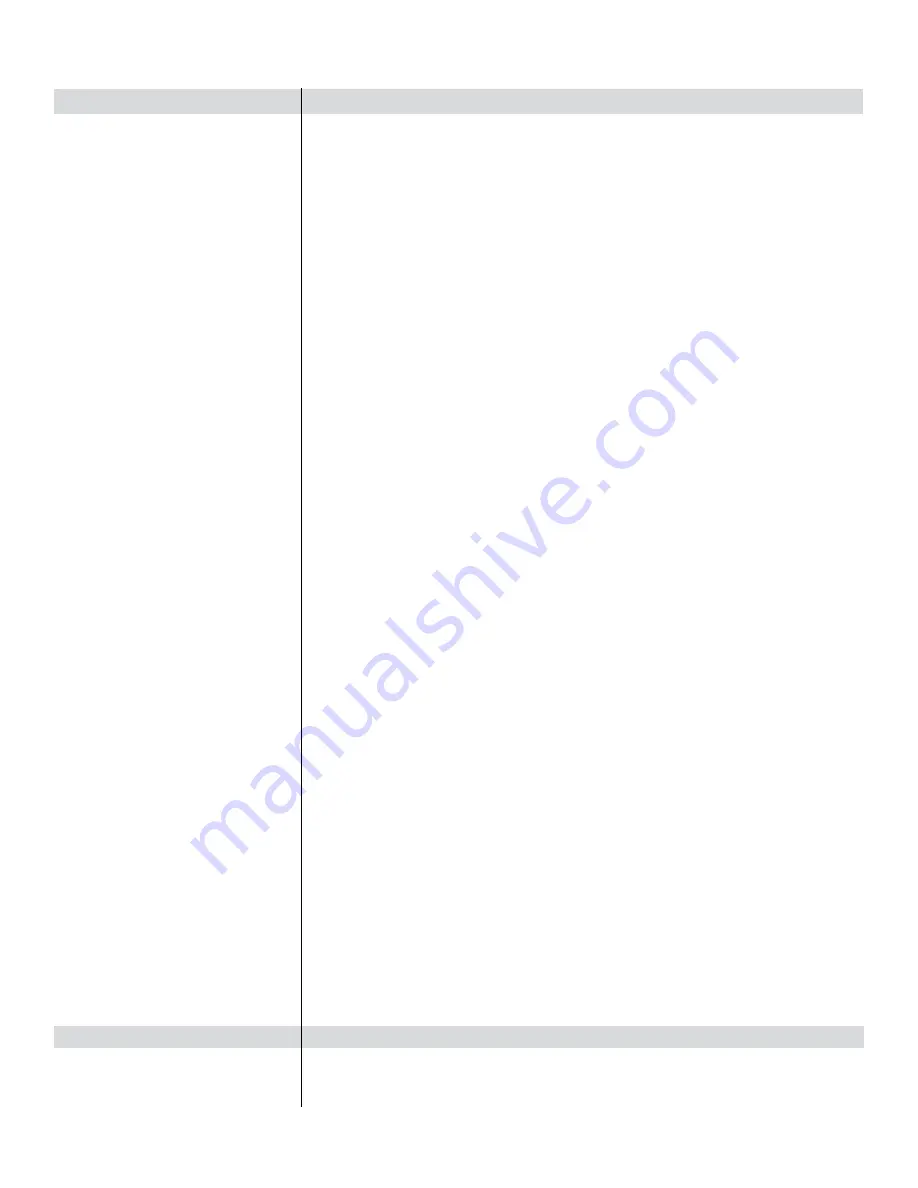
Page 31
Needle Thread Breaks
Corrective Measure
• Check the tension of the top tensioner and bobbin for proper balance
(see pages 19-20).
• Top and bobbin tension not
balanced
• Look for severe twisting of threads when approximately 12 to 15 inches
has been pulled off, with ends pinched together. Cotton threads are
particularly susceptible to dry rot which makes thread brittle. Do not use
poor quality thread, or thread that is rotted or brittle.
• Thread cones/spools are
poor quality or may have
severe twisting or thread rot
• Check that the machine is threaded correctly.
• The machine head has been
threaded incorrectly or thread
spools are not positioned
correctly
• Inspect for accidental double wrapping of thread on thread guides.
• Inspect the thread stand making sure the eyelets of the stand are directly
over the spools.
• Inspect the vertical positioning of the thread cones. Tipped cones can
dramatically affect thread tension and can cause breakage.
• Inspect for particles and remove any lint or debris.
• Particles in tension discs
• Change the bobbin. The slightest hesitation of the bobbin rotation can
be the cause of dramatic tension change and thread breakage. Use
ONLY INSPIRA® bobbins
• Bobbin rotation is not smooth
• Change the needle at least once per quilt. Make sure the needle is in-
stalled to the top of the sight hole in the needle bar.
• Needle is burred, bent or
dull, or installed incorrectly
• Replace the needle with one better suited for the thread. Use the proper
size needle.
• Needle not suited for the
thread
• Move more quickly so stitches don’t overlap or build up. When starting
the machine, begin moving immediately. Sewing in one place too long
will cause the thread to break.
• Hesitating too long at one
point in the pattern
• Timing of the machine is improper. Consult a repair technician at your
local, authorized PFAFF® representative.
• Improper needle/hook
relationship
• If the thread is shredding at the needle plate, check for burrs or jagged
edges. Gently rub with metal cloth to remove the sharp edge. Consult a
repair technician to polish any hard to reach or delicate areas, or if the
burr is inside the hole.
• Damage or burr at the needle
hole in the needle plate or
any other place along the
thread path
• Use needles recommended by PFAFF®. Using the wrong needle with a
smaller shank diameter causes many problems. For example a system
1738 or 287WH needle with a shank diameter of 1.64mm will fit loosely
into the clamp at an angle. This may cause skipped stitches because the
needle is positioned too far away from the hook point. It can also cause
the needle to hit the hook, breaking the needle.
• Wrong type of needle
• The needle is too close to the hook, which causes friction and a possible
collision of the hook point and the needle.
• Other possible causes:
• Needle plate damage.
• Hook damage.
• Broken needle inside needle bar clamp, preventing the needle from
insertion to the top of the clamp.
• Damaged needle bar clamp.
No Visible Display
Corrective Measure
• Check the communication cable that connects the display to the machine
and make sure the connection is secure.
• Cable unplugged