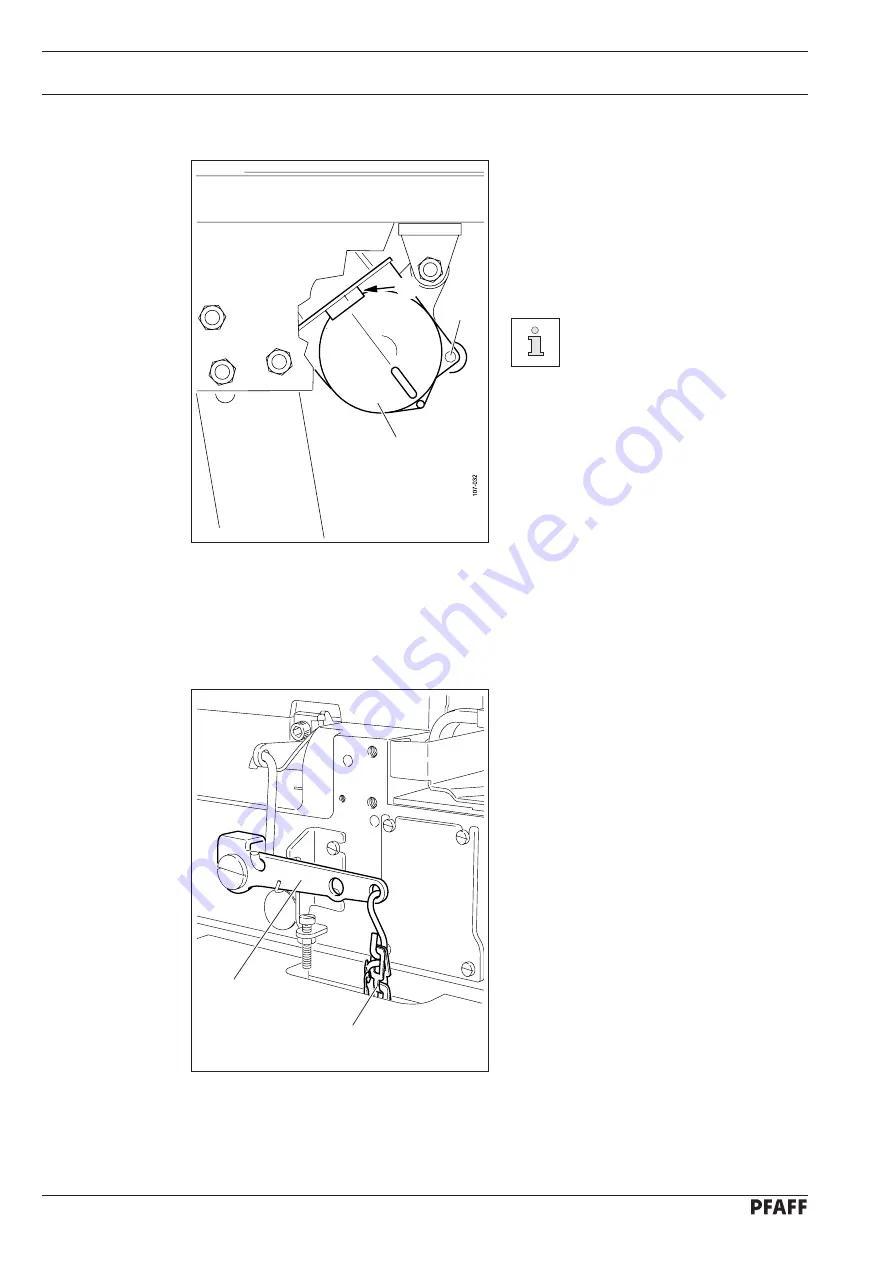
Mounting and commissioning the machine
8 - 9
8
.01.10
Fitting the bottom belt guard.
●
The belt guard
1
must be located to allow
free movement of the motor pulley and
the drive belt.
●
Tighten screws
2
.
Fig. 8-05
shows a Quick-motor.
When using a different motor,
follow the instructions in the
motor manual.
8
.01.11
Chain for securing the pedal
●
Secure chain
1
for raising the sewing foot
to lever
2
and to the right pedal.
Fig. 8 - 06
1
2
1
Fig. 8 - 05
2
2