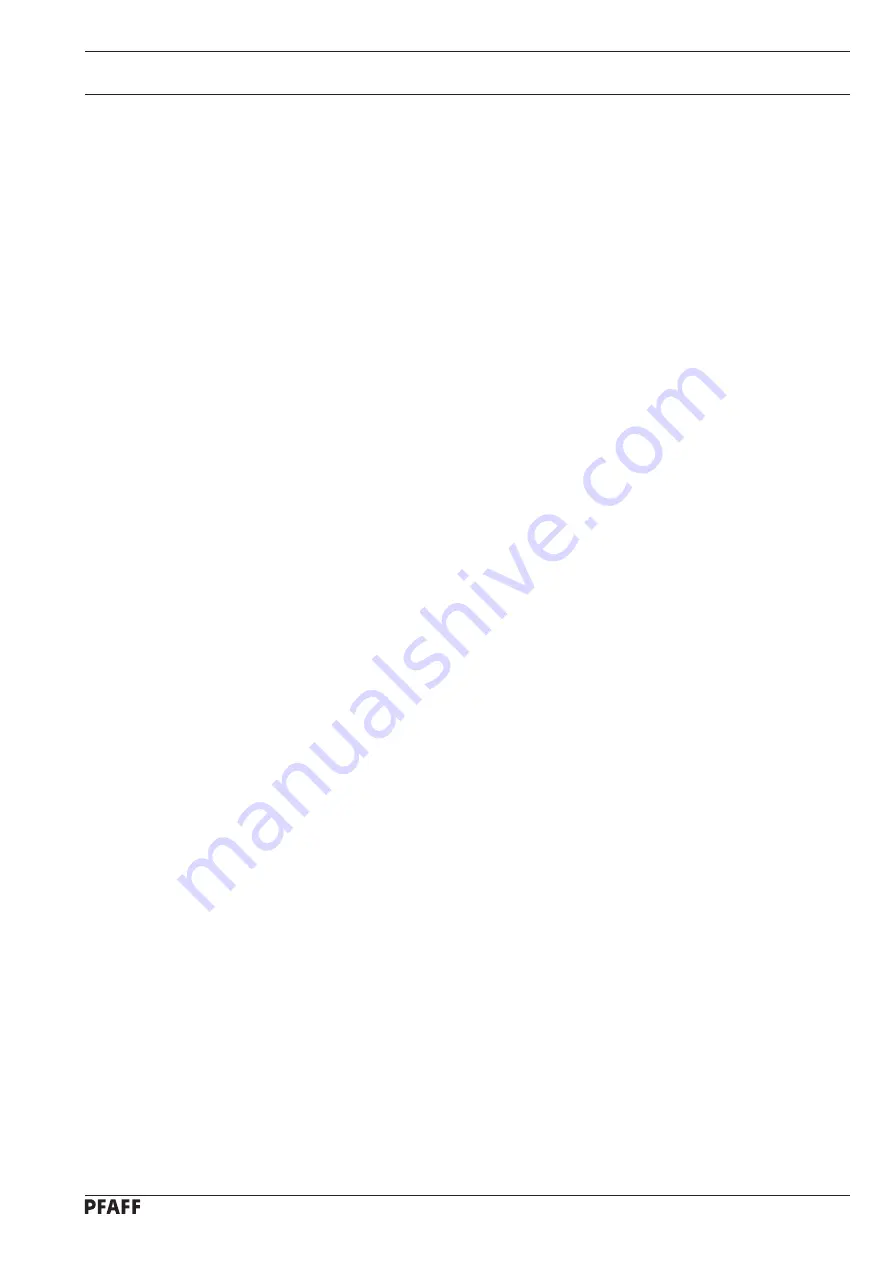
Safety
1 - 1
1
Safety
1
.01
Regulations
This machine is constructed in accordance with the European regulations indicated in the
conformity and manufacturer's declarations.
In addition to this instruction manual, please also observe all generally accepted, statutory
and other legal requirements, including those of the user's country, and the applicable pol-
lution control regulations!
The valid regulations of the regional social insurance society for occupational accidents or
other supervisory authorities are to be strictly adhered to!
1
.02
General notes on safety
●
The machine must only be operated by adequately trained operators and only when the
instruction manual has been fully read and understood!
●
All notices on safety and the instruction manual of the motor manufacturer are to be read
before the machine is put into operation!
●
All notes on the machine concerning danger and safety must be observed!
●
The machine must be used for the purpose for which it is intended and must not be
operated without its safety devices; all regulations relevant to safety must be adhered to.
●
When part sets are changed (e.g. needle, presser foot, needle plate, feed dog or bob-bin),
during threading, when the workplace is left unattended and during maintenance work,
the machine must be disconnected from the power supply by turning off the on/off
switch or removing the plug from the mains!
●
Daily maintenance work must only be carried out by appropriately trained persons!
●
Repairs and special maintenance work must only be carried out by qualified technical
staff or persons with appropriate training!
●
During maintenance or repairs on the pneumatic system the machine must be
disconnected from the compressed air supply! The only exception to this is when
adjustments or function checks are carried out by appropriately trained technical staff!
●
Work on the electrical equipment must only be carried out by technical staff who are
qualified to do so!
●
Work on parts or equipment connected to the power supply is not permitted! The only
exceptions to this are specified in regulations EN 50110.
●
Conversion or modification of the machine must only be carried out under observation of
all relevant safety regulations!